Why Automated Optical Inspection Is a Winner in PCB Quality Control
Printed circuit board (PCB) manufacturers operate within an increasingly challenging marketplace that requires dealing with frequent supply chain shortages, rising customer demands and increased output requirements. Excelling in PCB quality control is a meaningful way to maintain competitiveness despite these conditions. Many decision-makers have increasingly invested in automated optical inspection (AOI) at their facilities. This approach leads to numerous benefits.
Better Results During an Emerging Worker Shortage
Although many people weigh in about material shortages in the semiconductor supply chain, the increasing threat of a labor shortage is a less common conversation topic. However, sources suggest the situation could reach a crisis point by 2030. At least one chipmaker has already delayed the planned opening of a new factory due to insufficient workers to install and operate the facility’s specialized equipment.
Automated optical inspection does not wholly tackle the problem, but it’s a worthy solution to assist during these challenging times that may worsen before they improve. As employees face rising workloads, they may need to juggle more tasks. This could make them more tired, stressed and less likely to catch PCB quality control issues. However, automated inspection solutions supplement their efforts, lowering the chances of faulty products reaching the market.
Similarly, AOI products could reduce the training needed for new workers to learn about best practices while checking PCBs. Even if those employees make occasional mistakes, the automated tools will likely fill many gaps created by oversights or blunders.
Although this type of automation does not remove the need for human oversight, it often reduces the number of team members previously required to do quality control checks. Those employees can be reskilled for other roles. Such approaches make workplaces more versatile, even as shortages loom.
Continuous Improvement of PCB Quality Control Processes
Automated optical inspection significantly tightens PCB quality control while allowing companies to pursue data-driven improvements. Some factories may even increase production volumes after beginning to use AOI. Doing so enables getting the same or better results during post-production checks.
Creating lasting quality improvements requires decision-makers to understand how various choices made within the manufacturing process contribute to the results. Selecting laminates with low thermal expansion rates maintains high PCB performance and stability, resulting in more satisfaction.
Most AOI platforms allow users to track statistics such as the percentage of components that pass or fail. Leaders can dig into those details and use the specifics to implement new processes, training programs or other improvements. These tools can also detect near-microscopic flaws humans don’t immediately notice.
Leaders should examine how automated optical inspection fits into their existing processes. Similar solutions like X-ray machines support cost management and elevate factory productivity. Implementing AOI can show decision-makers what’s working best and which areas to target for improvement.
Encouraging a culture of continuous improvement allows managers to address issues promptly and learn about their root causes. The alternative is that customers may find high percentages of flawed PCBs, causing them to lose confidence in a company’s products and reliability.
Treating PCB quality control as a constant priority rather than something often overlooked also urges employees to show accountability and take pride in their work. Even the most advanced AOI platform will not solve all a company’s internal issues. However, it can substantially lessen them, especially when all parties commit to excellence.
Strategic Tech Investments Strengthen Companies
Automated optical inspection is a significant competitiveness driver, especially since many leading companies have integrated it into processes. Leaders will get the best results when they think about which existing weaknesses to overcome. Alternatively, they can consider how the technology will allow the company to meet new needs.
Those overseeing a Massachusetts-based PCB company took the latter approach when they recognized the organization had reached a tipping point after broadening its operations and customer base. Although the company was using some AOI equipment at the time, leaders recognized and sought to address shortcomings by investing in updated options.
The facility’s two-dimensional machines could not detect certain defects. A complete reliance on manual inspections to catch those issues caused slowdowns and prevented growth. The chosen new equipment had 3D vision technology that provided 100% coverage for each solder joint and component. They also gathered data pinpointing why defects occurred, giving leaders actionable information to prevent further problems.
Artificial Intelligence Can Enhance Automated Optical Inspection
AOI may also minimize how often flawless PCBs fail inspections and vice versa. Having fewer false alarms maximizes productivity and can safeguard a company’s reputation. One of the most common ways to achieve that goal is to use well-trained artificial intelligence (AI) algorithms to increase performance and accuracy.
Researchers in The Netherlands examined the results achieved when using several machine learning models to minimize false positives. The training and testing data included more than 25,000 instances of AOI platforms categorizing error-free components as defective.
The results showed machine learning could reduce the solder quality of through holes failing automated checks.
Artificial intelligence can also support PCB quality control in other ways, such as if robots move components into the right position or orientation before inspections begin. While discussing the company’s AOI tool that incorporates artificial intelligence, an Omron executive explained the need to proceed carefully when using AI with optical inspection processes.
He mentioned the need to operate methodically and determine when AI could genuinely help. Artificial intelligence has pros and cons in manufacturing environments. Considering safe and effective ways to use it will help leaders decide if and when to use AI with automated optical inspection tools.
It’s Time to Consider Automated Optical Inspection
Although bringing AOI into a PCB manufacturing plant takes time and thought, this decision often proves worthwhile for improving internal processes and results. Leaders can enhance the likely outcomes by setting measurable goals and monitoring the progress.
Giving employees ample time to learn how to work with AOI tools is also necessary, particularly when automation significantly changes a worker’s tasks and responsibilities. Asking people for feedback will help them feel more involved in the transition. Finally, decision-makers should consider gradually implementing the technology and scaling once the results justify it. That will motivate them to make future investments.
Comments (0)
This post does not have any comments. Be the first to leave a comment below.
Featured Product
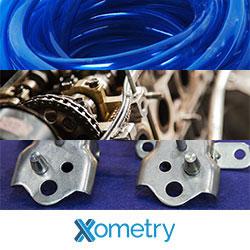