6 Implications of the Chip Shortage for Auto Manufacturing
The past few years have proved challenging for the auto manufacturing industry. Automakers faced a slew of obstacles amid the COVID-19 pandemic, but few were as far-reaching and disruptive as the chip shortage.
Median semiconductor inventories fell from 40 days in 2019 to less than five in 2021. Even as chip manufacturing has regained momentum, automakers still face demand far outpacing their semiconductor supply. Uncertainty still surrounds the chip supply chain and auto industries, and this shortage will undoubtedly have lasting effects.
Where Does the Chip Shortage Come From?
The current semiconductor shortage comes from a perfect storm of disruptions. About 81% of semiconductor contract manufacturing came from Taiwan and South Korea in 2020. When the COVID-19 pandemic struck, companies close to the outbreak’s epicenter were among the first to close, pausing much of the world’s chip supply.
Demand for these technologies skyrocketed at the same time. Connected electronics became increasingly popular in consumer and commercial markets as companies embraced remote work worldwide. Car sales dropped due to declining travel, and steep demand increases in other sectors further strained the already thin semiconductor supply.
New challenges arose as lockdown restrictions loosened and chip manufacturing capacity rose. Roughly 60% of the global neon supply comes from Ukraine, which now faces disruption from the ongoing conflict with Russia. Vehicle demand has also started to rise again, increasing the pressure on automakers’ existing backlogs.
These factors will continue to strain semiconductor supplies for some time. Here are six implications that will have on the automotive industry.
1.Declining Revenue
The most direct impact of the ongoing chip shortage is falling revenue among automakers. Manufacturers still have lower semiconductor inventories and long, disruption-prone logistics routes between them and their chip suppliers. Consequently, they won’t be able to produce as many vehicles, leading to lower new car sales.
Global vehicle production fell by more than 14 million units between 2019 and 2020. While levels increased in 2021, they lag pre-pandemic output by more than 10 million units. Automakers can expect that trend to continue throughout 2022 and possibly beyond as demand rises.
Leading automotive manufacturers could see $110 billion in losses in 2022 due to the chip shortage. Automakers may see higher revenues than in 2021 and 2020, but they should anticipate lower-than-usual sales.
2.Repeated Shortages
Similar shortages will likely recur in the future, given the nature of the situation. Semiconductor manufacturers have accelerated production to make up for their considerable backlogs, operating at more than 90% capacity in many facilities. Disruptions with raw material suppliers could have cascading impacts at those levels, leading to another bullwhip effect.
Demand may also fluctuate over the next few years due to availability and prices. Prices may decrease as production regains steam and cars become more available, leading to more purchases.
However, that demand could pass production levels again, given the current shortage’s extent. That would lead prices to rise. More consumers may turn to alternatives as it becomes harder and more expensive to buy a new car. This pattern of rising and falling demand will make it difficult to manage inventories and supply chains, leading to repeated but likely smaller shortages.
3.Emphasis on Lower-Tech Vehicles
One possible solution to these challenges is to focus on producing and selling vehicles with fewer semiconductors. Some chip usage is unavoidable for modern safety features, but many semiconductors cars use aren’t essential. Automakers might ship vehicles without extra features to stretch their inventories further.
Wireless charging, lumbar support, automatic starting and other features demand chips but are technically luxuries. Automotive manufacturers can easily cut them out and still have a reliable, functional vehicle to sell. Switching to these lower-tech options would help satisfy the demand for new cars without straining chip supply chains beyond their current level.
This strategy does come with some setbacks since today’s consumers have come to expect many of these features. Demand for electric vehicles is also rising, with some automakers investing upwards of $867 million to enable electrification, but these models require more semiconductors. Consequently, focusing on lower-tech models could affect sales and profits.
4.Product Redesigns
A more long-term solution is to redesign vehicles to deliver the same features with fewer semiconductors. Cars will grow increasingly high-tech and automakers could use systems that run several functions through the same semiconductor. It will become easier to enable these more efficient designs as electronics advance.
Volkswagen Group of America Chief Executive Scott Keogh hinted at this future at the Reuters Events Automotive Summit. He mentioned Volkswagen is looking at using more modules with fewer chips, moving away from the idea that each system needs a dedicated chip. Other automakers will likely follow a similar strategy to prevent future semiconductor shortages.
These redesigns will require more R&D spending initially and may need more expensive chips. However, they’ll help the industry reduce its dependence on these technologies over time, mitigating future disruptions.
5.Restructured Supply Chains
Another positive change that will result from the chip shortage is a widespread move to restructure supply chains. The COVID-19 pandemic may be a once-in-a-lifetime level disruption, but it revealed how fragile the current system is. Most of the world’s chips come from a few centralized locations, so shortages would’ve happened eventually.
Recent legislature aims to increase domestic semiconductor manufacturing, giving automakers closer suppliers. Disruptions will be less impactful as more manufacturers source these technologies from nearby facilities. Shorter logistics routes will enable faster responses and lower supply chain costs.
Automakers will likely move away from lean principles to hold more reserve inventories, mitigating future shortages. In that same vein, the sector will likely embrace distributed sourcing and reduce single dependencies.
6.Growing Supply Chain Visibility
The automotive industry will and should place more emphasis on supply chain visibility. It’s unreasonable to think that any company could have predicted the COVID-19 pandemic, but more transparency would’ve helped mitigate the shortage.
Auto manufacturers need to understand factors driving consumer demand and have more real-time insight into suppliers. That transparency should reach raw material sources to help avoid the bullwhip effect. Enabling this level of visibility will require closer collaboration with supply chain partners and technologies like the Internet of Things (IoT) and artificial intelligence (AI).
IoT devices can provide real-time data that AI interprets to offer insight into potential supply chain or demand disruptions. Manufacturers can then adapt as necessary to mitigate their impacts.
The Chip Shortage Will Have Long-Term Implications
The semiconductor shortage will likely outlast the pandemic, with ripple effects lasting years into the future. Automakers must anticipate these challenges and adapt to mitigate them and prevent similar situations.
The chip shortage poses substantial obstacles, but it’s also a learning opportunity. Manufacturers that understand these disruptions’ causes can evolve to become more resilient.
Comments (0)
This post does not have any comments. Be the first to leave a comment below.
Featured Product
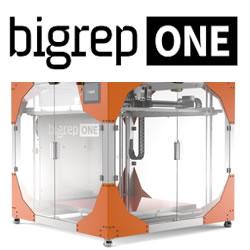