5 Ways Machine Learning Is Improving Manufacturing
Artificial intelligence (AI) is one of the fastest-growing technologies in the business world today. AI is a broad umbrella, covering many specific technologies, and machine learning is one of the most promising of these. Machine learning in manufacturing, although relatively new, has already shown significant potential.
Manufacturing today is becoming increasingly data-centric as Industry 4.0 takes off. As this trend continues, industrial machine learning algorithms have more to offer. Experts believe AI could create $2 trillion in new value across the global manufacturing industry, most of which comes from machine learning processes.
These figures are impressive, but estimations mean little without real-world, concrete applications. With that in mind, here are five examples of how machine learning is improving manufacturing today.
1. Forecasting Demand
One of the most common ways in which manufacturers use machine learning is demand forecasting. Machine learning algorithms can predict when consumer behavior will shift, informing manufacturers about how to prepare for the future. They can then accelerate or slow the production of some items to prevent surplus or shortages.
These predictions enable facilities to embrace lean manufacturing with a minimal risk of disruption. The COVID-19 pandemic highlighted the dangers of just-in-time manufacturing, as sudden supply and demand changes brought some production to a halt. Machine learning in manufacturing can help mitigate these risks because it lets manufacturers predict these shifts and prepare accordingly.
By the very nature of machine learning, these forecasts will become more accurate over time. The more manufacturers use them, the more these algorithms will learn, leading to more reliable and longer-term predictions. These exponential benefits will help early adopters of this technology outperform competitors further down the road.
2. Optimizing Workflows
Many people would assume manufacturing has become increasingly efficient over time. But this isn’t entirely the case.
Average manufacturing capacity utilization has declined since 1970, despite improvements in other areas. Industrial machine learning can help reverse this trend by revealing how to optimize workflows.
Machine learning solutions let manufacturers create digital twins of their facilities, then model different scenarios in them. These “what if” simulations show how various changes would affect productivity, space utilization, and other factors. Manufacturers can then determine the best course of action before disrupting workflows, making more effective changes.
There’s no one-size-fits-all solution to workflow optimization, so these digital twins are an ideal resource for workflow improvements. They reveal what would be the most effective given a facility’s specific needs, goals, and resources. Manufacturers can then be sure their changes will lead to positive outcomes without potentially costly trial and error.
3. Predicting Maintenance Needs
Another one of the most promising applications of machine learning in manufacturing is predictive analytics. Machine learning algorithms can predict when equipment will fail by analyzing performance data from sensors within machines. These predictions enable manufacturers to adopt an optimal approach to repairs, avoiding the downsides of both corrective and schedule-based maintenance.
Corrective maintenance isn’t ideal because the cost of unexpected downtime and fixing breakdowns is typically higher than maintaining equipment. Preventive maintenance on a schedule prevents these breakdowns but could result in unnecessary downtime from unneeded repairs. Predictive maintenance provides the best of both worlds by avoiding unnecessary repairs and breakdowns.
By adopting predictive maintenance, manufacturers keep equipment in optimal condition while driving down repair-related costs. According to a Deloitte study, it can increase equipment uptime by 10% to 20% while reducing maintenance costs by 5% to 10%. Some companies have seen savings as high as $300,000 per asset after implementing this machine learning-based approach to repairs.
4. Improving Quality Control
Quality control is a crucial part of any manufacturing operation, as spotting defects before products ship minimizes costs and satisfies customers.
Traditionally, workers perform most if not all quality checks. But manual quality control is inherently flawed. People require time to analyze products closely enough to notice minor defects, and repetitive work can lead to boredom, which generates mistakes.
Machine learning quality control systems compare products to ideal models, taking a data-based approach to quality assurance. One study found that these inspections increase defect detection rates by 90% compared to humans. The same systems can also lead to a 50% increase in productivity, as machines can recognize flaws far faster than people.
As machine learning algorithms gather more data, they can identify the source of various defects. This information can then help manufacturers adjust their processes to prevent similar cases in the future. Automating this task with machine learning also frees workers to focus on other tasks, improving overall productivity.
5. Enabling More Personalization
In recent years, manufacturers have been moving towards higher levels of personalization. Consumers’ increasing reliance on digital services has led them to expect highly personalized products and services, but this can be challenging to provide. Machine learning in manufacturing can help manufacturers meet these demands, improving satisfaction and fostering loyalty.
Just as machine learning models can predict trends from consumer behavior, they can determine their unique needs and wants. If a client puts in a specific request, machine learning algorithms can analyze it to determine how best to produce it. These models could even infer features that customers want that they didn’t mention explicitly.
Using machine learning to glean this information, manufacturers can produce hyper-personalized solutions for their customers. Since consumers are willing to pay 25.3% more on average for personalization, this can help manufacturers outperform competitors. As industrial machine learning models advance, they’ll enable even more customization, leading to exponential benefits.
Industrial Machine Learning Is Reshaping Manufacturing
Machine learning, by nature, becomes more accurate and helpful as it sees more use. As machine learning in manufacturing continues to rise, these tools will advance, and new use cases will emerge. Industrial machine learning has already made remarkable progress among manufacturers today, and these compounding benefits will take it further.
Machine learning’s potential is so vast that, before long, it could reshape the entire industry. Despite its limited implementation today, this technology has already helped manufacturers overcome persistent problems in the sector. As more facilities embrace it and its possibilities expand, machine learning could become a standard throughout the industry.
Comments (0)
This post does not have any comments. Be the first to leave a comment below.
Featured Product
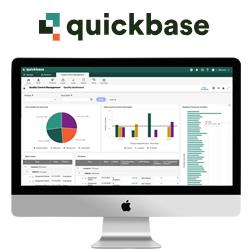