3D PRINTING & THE SUPPLY CHAIN
There were a number of reasons why Jellypipe — an advanced and virtual 3D printing ecosystem which draws together 3D printing users, service suppliers, and experts — was developed, but one in particular is becoming a prominent area of interest in light of the current global COVID-19 pandemic.
The key motivation behind Jellypipe is to stimulate the use of 3D printing as an alternative to traditional manufacturing processes. Today a growing number of robust plastic and metal 3D printing technologies exist with the accuracy and repeatability required for use in end-use part and component production, and the palette of materials is extensive. The ability to make innovative and complex geometries impossible using conventional manufacturing processes in a speedy and cost-effective way is also a key driver.
But the conversation in 2020 has very obviously moved on to the way that 3D printing can affect global supply chains. COVID-19 has caused us all to look at ourselves, the ways we live, our social and business interactions, but none more so than business owners with global supply chains that have been shown to be fragile and which introduce vulnerabilities that can seriously affect operations, viability, and profitability.
Going Local Globally
The most obvious way that unwieldy supply chains can be reduced is to localise supply, and try and get part production as close as possible to the point of consumption. Attempting to do this via traditional manufacturing methods will not work. The very reasons that caused manufacturing to be offshored, mainly cheap labour, means bringing it back on-shore ratchets up the manufacturing costs.
But there is another driver, and a very important one. Far flung manufacturing facilities benefitting from low labour costs operate on a model of “pile them high, sell them cheap”. They cater for true mass manufacturing. “You can have this part in any colour so long as its black, and any shape so long as it is the exact shape of all the other millions of parts we manufacture.”
3D printing promotes mass customisation, or what someone once called the “economies of one” rather than the “economies of scale”. The ability to customise parts facilitates simplified product differentiation, and allows for small quantity production by companies. The number of suppliers required will be reduced drastically due to the flexibility that 3D printing can deliver. The focus becomes customer satisfaction and the ability to respond quickly and in an agile way to shifting customer demand.
Another potential advantage of 3D printing to the supply chain is that the technology can simplify some production processes, it having the ability to manufacture a part in one 3D printing process rather than by assembling several components which may require different supply chains. It is a decentralised manufacturing technique that will alter the distribution network. Because of this, the level of complexity and overhead required of a product or supply chain can be reduced, and consequently the operation of the supply chain is more efficient, and the flexibility of 3D printing offers more variety of end products.
Democratisation
The big play here is that 3D printing is disruptive enough of a technology to facilitate a new industrial revolution. There are game changers throughout history. The development of the assembly line changed manufacturing forever. The worldwide web allowed everyone to be a publisher and have a voice, not just the select few. 3D printing allows everyone to be a manufacturer. It democratises manufacturing, and with this democratisation the effect on the supply chain and on the ability to manufacture at the point of consumer demand is obvious.
And here we come to the important concept of printing on demand. This has an enormous impact on inventory and logistics. There is no need to have vast warehouses with thousands of identical products stacked up awaiting demand. Instead, wherever a product is needed it can be made using 3D printing to order. This collapses and simplifies the supply chain, adding new efficiencies to the manufacturing process.
These efficiencies are far reaching and numerous, and stretch from the overall cost of distribution and assembly, to the innovative nature of the product produced and the time and cost elements of such part production, at the same time minimising scrap, facilitating customisation, and improving assembly cycle times.
Quite fundamentally, it has the ability to completely destroy the global supply chain, and rebuilds it as a new entirely local system.
Manufacturing via 3D printing and the supply chain surrounding 3D printing overcomes the traditional constraints on traditional manufacturing and the traditional supply chain, namely that they only work when applied to the efficiencies of mass manufacture, the need for low-cost high volume assembly workers, and the need for building infrastructure to support each part of the production and distribution process.
3D Printing’s Sweet Spot
3D printing has a sweet spot. Its real value and its ability to turn the traditional manufacturing regime on its head rotate around the fact that it caters for low volume, customer-specific products, products that can be complex in ways unattainable via traditional manufacturing. It eliminates the need for high volume production facilities and a high number of low-paid assembly workers, effectively taking out probably more that 50% of the traditional supply chain straight away. It effectively draws a massive question mark over the very foundation of the traditional supply chain model, it no longer making sense or being financially efficient to send products across the globe to customers when production can take place locally almost anywhere in the world at the same or less cost.
Jellypipe has a part to play in this shift of emphasis away from traditional manufacturing and supply chains and towards the use of 3D printing. It exists as a holistic ecosystem of the entire 3D printing community, and reduces the barriers to entry that exist and put a brake on the adoption of the technology for production or parts and components. The current global pandemic has highlighted the advantages of local manufacturing and the rationalisation of global supply chains, and the Jellypipe community is consistently addressing these issues and coming up with viable solutions for manufacturers worldwide.
Comments (0)
This post does not have any comments. Be the first to leave a comment below.
Featured Product
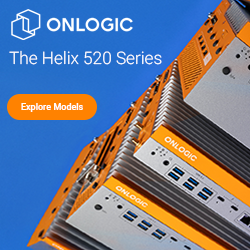