3D Printing: Head and Shoulders Above the Rest
Oskar Zielinski works in the research & development department at Arcam EBM – a GE Additive company in Gothenburg, Sweden. He is responsible for the maintenance, modification and repair of electron beam melting systems.
He recently put an Arcam Q20plus electron beam machine through its paces and created a statue of GE’s founder, Thomas Edison using Titanium (Ti64). The whole build took 90 hours and stands an impressive 387 millimeters tall.
Oskar created 25 pieces and generated different net structures inside each layer to test the capabilities of the machine. All 4,300, 90-micron layers were printed in one go, with only a little support between the outer skins of the slices and nets were all free floating without any supports at all.
The different net structures inside show the amazing filigree work of electron beam melting.
A time lapse showing the statue being printed layer by layer was captured from inside the machine using an Arcam LayerQam that is normally used for defect detection in printed parts.
“I am really happy with the result; this final piece is huge. I keep wondering though what Thomas Edison would have thought if someone would have told him during the 19th century about the technology that exists today,” said Oskar.
Oskar Zielinski with Thomas Edison statue
About GE Additive
GE Additive – part of GE (NYSE: GE) is a world leader in additive design and manufacturing, a pioneering process that has the power and potential to transform businesses. Through our integrated offering of additive experts, advanced machines and quality materials, we empower our customers to build innovative new products. Products that solve manufacturing challenges, improve business outcomes and help change the world for the better. GE Additive includes additive machine providers Concept Laser and Arcam EBM; along with additive material provider AP&C.
Comments (0)
This post does not have any comments. Be the first to leave a comment below.
Featured Product
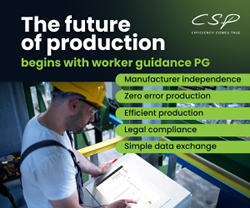