3D printing hack: Researchers crash drone with sabotaged propeller
Conner Forrest for TechRepublic: University researchers were able to sabotage a drone by hacking the computer controlling the 3D printer that made its parts, according to a research paper released Thursday. By changing the design of the propellor before printing, they caused the $1,000 drone to "smash into the ground" and break, shortly after take off.
The paper, titled dr0wned - Cyber-Physical Attack with Additive Manufacturing, was a joint effort from researchers at Ben-Gurion University of the Negev (BGU), the University of South Alabama, and Singapore University of Technology and Design. In the paper, the researchers explained how they committed the cyberattack, and what the attack could mean for the future of 3D printing security.
Using a phishing attack, the researchers gained access to the PC that was connected to the 3D printer. Cont'd...
Comments (0)
This post does not have any comments. Be the first to leave a comment below.
Featured Product
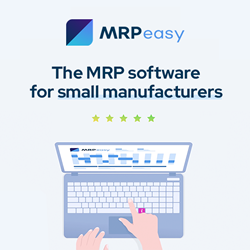