MIT Food Computers
From MIT: The Food Computer is a controlled-environment agriculture technology platform that uses robotic systems to control and monitor climate, energy, and plant growth inside of a specialized growing chamber. Climate variables such as carbon dioxide, air temperature, humidity, dissolved oxygen, potential hydrogen, electrical conductivity, and root-zone temperature are among the many conditions that can be controlled and monitored within the growing chamber. Operational energy, water, and mineral consumption are monitored (and adjusted) through electrical meters, flow sensors, and controllable chemical dosers throughout the growth period.
Each specific set of conditions can be thought of as a climate recipe, and each recipe produces unique results in the phenotypes of the plants. Plants grown under different conditions may vary in color, size, texture growth rate, yield, flavor, and nutrient density. Food Computers can even program biotic and abiotic stresses, such as an induced drought, to create desired plant-based expressions... (project homepage)
Comments (0)
This post does not have any comments. Be the first to leave a comment below.
Featured Product
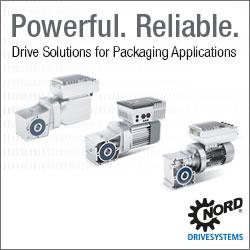