The Complete Guide to Batch Production: How It Streamlines Manufacturing
Discover how batch production boosts efficiency, quality, and flexibility in modern manufacturing, with tools like Origin ensuring traceability and compliance across the supply chain.
Today, companies are under constant pressure to balance efficiency, quality, and flexibility. Batch production is proving to be a powerful solution. Positioned between the extremes of one-off production and high-volume continuous manufacturing, batch production allows for both scale and adaptability.
What is Batch Production?
At its core, batch production involves manufacturing products in fixed quantities or "batches" rather than a continuous stream. Each batch is processed through one stage of production before moving on to the next, ensuring uniformity across the batch. This technique is widespread in industries such as pharmaceuticals, food and beverages, textiles, cosmetics, and chemicals, where consistent quality and compliance are critical.
Unlike mass production systems, batch manufacturing offers manufacturers the ability to switch between products and formulations with greater ease. A skincare company, for instance, may produce a batch of moisturiser, clean its equipment, and then initiate a new batch of serum, all within the same facility. This flexibility allows manufacturers to respond swiftly to market demands, customise offerings, and limit production to what is necessary, reducing excess inventory.
How It Streamlines Manufacturing
The value of batch production lies in its ability to offer operational control without sacrificing productivity. Because the production occurs in self-contained lots, it becomes significantly easier to identify, monitor, and correct errors or inconsistencies. In regulated industries, where even minor deviations can lead to compliance failures or recalls, this level of control is invaluable.
From a cost perspective, batch production reduces waste and optimises the use of raw materials. Manufacturers can run limited quantities based on forecasted demand, avoiding overproduction and minimising storage costs. Furthermore, it enables careful quality checks between batches, which can be adjusted or improved without shutting down the entire line.
The Role of Technology
Today's batch production environments are far more sophisticated than those of the past. The integration of smart manufacturing tools — from automated mixers and programmable logic controllers to cloud-based ERP and MES platforms — has transformed batch systems into agile, data-driven ecosystems.
One of the most significant advancements in this space is traceability. With growing scrutiny on sourcing, sustainability, and compliance, knowing exactly where a product originated and how it was processed is crucial. Tools like Origin, a blockchain-based track and trace solution, have brought unprecedented transparency to batch production. By recording every step of the product journey, from raw materials to final packaging, Origin helps manufacturers maintain integrity, meet regulatory requirements, and reassure consumers about product authenticity.
Learn more about Origin: https://acviss.com/origin/
In the pharmaceutical and food sectors, digital batch records have largely replaced paper-based logs, making it easier to conduct audits, trace product history, and ensure adherence to Good Manufacturing Practices (GMP). The integration of IoT sensors enables real-time monitoring of temperature, humidity, and other critical parameters, ensuring each batch remains within specification throughout the process.
Benefits and Limitations
Batch production delivers clear benefits across productivity, quality, and compliance. It supports short production runs for limited editions or seasonal demand, facilitates innovation through controlled experimentation, and ensures rapid detection and isolation of defects. In case of a quality issue, affected products can be traced to a specific batch, greatly simplifying recall processes and protecting the brand.
However, the system is not without its challenges. Transitioning between batches often requires equipment cleaning and reconfiguration, leading to downtime. If scheduling is poorly managed or forecasts are inaccurate, manufacturers may still face inefficiencies and bottlenecks. Additionally, the per-unit cost of batch production can be higher compared to mass production, especially for simple, high-demand items.
To counter these drawbacks, manufacturers are turning to lean production principles, predictive analytics, and skilled workforce training. These measures help streamline operations, reduce changeover time, and ensure that batch production remains both competitive and sustainable.
A Strategic Advantage in Modern Manufacturing
As markets become more dynamic and customer preferences more fragmented, the ability to produce in small, controlled quantities while maintaining high standards is a strategic necessity. Batch production meets this need without locking manufacturers into rigid, high-cost systems.
For businesses looking to balance responsiveness with quality, especially in highly regulated or consumer-sensitive industries, batch production is not just an alternative, it's a competitive edge. Combined with smart technologies and transparent tracking solutions like Origin, it offers a future-ready approach to manufacturing that is as efficient as it is resilient.
Featured Product
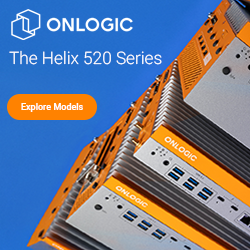
OnLogic's Helix 520 Series of Scalable Fanless Computers
The Helix 520 series utilizes the latest Intel Core Ultra processors with integrated edge AI capabilities to deliver exceptional performance and industrial-grade reliability for demanding applications in automation, robotics, machine vision, and more. Its unique modular design allows for flexible scaling of CPU and GPU performance, while robust connectivity and expansion options ensure seamless integration.