HORIZON MICROTECHNOLOGIES RECEIVES ESA SPARK FUNDING TO ADVANCE 3D PRINTING AND METALLISATION TECHNOLOGY FOR SPACE APPLICATIONS
The Spark funding will enable Horizon to refine its technology and demonstrate that its 3D-printed, metallised components are capable of meeting the extreme requirements of the space environment. By developing components that can withstand the harsh, unserviceable conditions of space, Horizon is proving that its technology is not only innovative but mature enough to address the ultimate engineering challenge.
(4th December 2024, Karlsruhe, Germany) Horizon Microtechnologies can today announce that it has secured funding in the framework of the European Space Agency's (ESA) SPARK programme administered by the Center for Satellite Navigation Hesse GmbH, CESAH. This funding marks a significant milestone in Horizon's journey, fuelling the development of its advanced 3D printing and metallisation technology to meet the rigorous demands of space applications.
The Spark funding will enable Horizon to refine its technology and demonstrate that its 3D-printed, metallised components are capable of meeting the extreme requirements of the space environment. By developing components that can withstand the harsh, unserviceable conditions of space, Horizon is proving that its technology is not only innovative but mature enough to address the ultimate engineering challenge.
"Receiving ESA Spark funding is a powerful step forward for Horizon," says Andreas Frölich, Horizon's CEO. "Space applications demand the highest standards of performance, longevity and reliability, and this support from ESA through CESAH is a testament to the potential we have to drive innovation in space technology."
Horizon's unique approach integrates the precision and design flexibility of 3D printing with advanced metallisation processes. For space applications, this means lighter, more compact components that maintain structural integrity and functionality, even in extreme conditions. Weight reduction, or SWaP (Size, Weight, and Power), is a crucial factor in space missions, as every gram counts toward efficiency. With Horizon's technology, components can be made lighter without sacrificing durability — a game-changer for space design and mission success.
Additionally, Horizon's technology supports the creation of monolithic components with complex geometries that would be challenging to achieve with traditional manufacturing techniques. This opens the door to novel design options, enabling engineers to build components that are both functionally robust and optimised for space constraints.
Frölich continues, "This project does more than just position Horizon's technology within the space sector, it also paves the way for broader industry adoption. Success in space — the most demanding of environments — provides a compelling proof-of-concept for sectors such as telecommunications, aerospace, and defence, where reliability and endurance are paramount. If Horizon's components can thrive in space, they can certainly meet the high standards of terrestrial applications."
Looking ahead, the ESA-supported project represents a vital step in Horizon's mission to advance 3D printing and metallisation technology for high-performance applications. By participating in the ESA Spark program, Horizon is building a foundation of credibility and performance that will drive the company toward even greater achievements.
Frölich concludes, "Horizon Microtechnologies is thrilled to embark on this next phase of growth, backed by ESA Spark funding and inspired by the possibilities of space innovation. As the company continues to push the boundaries of what is possible with 3D-printed, metallised components, we invite our partners, customers, and the wider technology community to join us on this exciting journey."
www.3dmicrofabrication.com
Featured Product
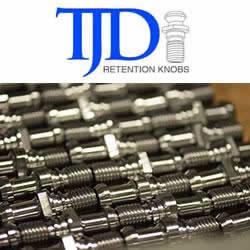