WAYLAND ADDITIVE SHOWCASES ADVANCES IN REVOLUTIONARY NEUBEAM® TECHNOLOGY AT FORMNEXT 2024
As one of the leading innovators in metal eBeam additive manufacturing (AM), Wayland Additive continues to push the boundaries of what’s possible in production applications.
(31st October 2024, Huddersfield, UK) Wayland Additive is thrilled to announce its presence at Formnext 2024, where it will be exhibiting its cutting-edge NeuBeam® technology, as featured on the Calibur3, in Hall 12.0, on stand B139. As one of the leading innovators in metal eBeam additive manufacturing (AM), Wayland Additive continues to push the boundaries of what's possible in production applications.
Over the past few years, Wayland's revolutionary NeuBeam® process has already gained significant traction in the market, with multiple commercial sales signalling the technology's readiness for widespread industrial adoption. Unlike other AM systems, NeuBeam®'s stabilised electron beam (eBeam) process in the Calibur3 system has been meticulously developed from the ground up, specifically for production purposes. This approach reflects the vast experience and fresh thinking brought by Wayland's development team, many of whom hail from the semiconductor industry.
Peter Hansford, Chief Revenue Officer at Wayland, comments: "The future of AM for production continues to evolve and expand. Working with the team at Wayland, I believe we are now started to fulfil the long-awaited potential of AM with a broader spectrum of metal materials. With NeuBeam®, we haven't just adapted existing technology, we've created something entirely new and stable, designed to meet the needs of serious production applications without being limited by the materials."
NeuBeam® technology unlocks the potential of eBeam metal AM through three key pillars: process stability, flexibility, and advanced in-process monitoring. The process is hot-part rather than hot-bed, significantly reducing residual stresses and making powder removal much easier. This gives users unprecedented flexibility to choose the temperature and melt strategy that best suits the part, material selection and application, rather than being confined by the process itself.
Hansford continues: "Our early commercial successes are proof that NeuBeam® is resonating with customers. Early adopters are working with a truly groundbreaking process, not a repurposed or copied one. NeuBeam® offers an open, transparent process, allowing manufacturers to print what they need, rather than being constrained by process limitations."
Formnext attendees will have the opportunity to see a Calibur3 metal AM system and the parts it has produced on the stand at Formnext, as well as learning how NeuBeam® is reshaping the metal AM landscape. "We're not interested in delivering black-box solutions," adds Hansford. "We will be at Formnext to form partnerships and develop tailored solutions for our customers, ensuring they get the best out of metal AM and achieve real production success."
Attendees at Formnext 2024 are also invited to join Wayland Additive's presentation given by Head of New Technologies at Wayland Martyn Hussey. The talk is entitled "Active Charge Neutralisation in ‘NeuBeam' Electron Beam PBF" and will be hosted on the Technology Stage in Hall 12.0 E42 11.00 - 11.15 on Wednesday 20th November. The Active Charge Neutralisation (ACN) technology, which is a core component of the NeuBeam® eBeam AM process, and which is successfully deployed in the Calibur3 production machine, will be discussed in detail during the session, highlighting the significant advantages it brings in reducing build times, improving process stability, and enhancing powder morphology.
Visit Wayland Additive at Hall 12.0, stand B139 at Formnext 2024 to explore the future of metal additive manufacturing.
www.waylandadditive.com
Featured Product
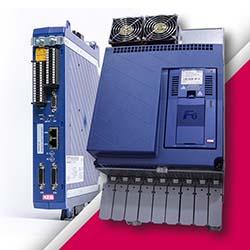