INTERROGATING YOUR MICRO MOLDING SUPPLIER TO ENSURE OPTIMIZED OUTCOMES
In today's ever-evolving technological landscape, the demand for precision-engineered micro molded parts has skyrocketed. From medical devices to electronics, industries seek micro parts that are consistent in quality and can be produced in large volumes.
Paul Runyan, VP of Sales, Accumold
In today's ever-evolving technological landscape, the demand for precision-engineered micro molded parts has skyrocketed. From medical devices to electronics, industries seek micro parts that are consistent in quality and can be produced in large volumes. However, with the growth in demand, there's a parallel increase in micro molding companies, making the selection process for customers quite challenging. To ensure you're partnering with a company proficient in delivering volume and repeatability, here are some essential questions you need to pose.
What is your experience in micro molding?
Micro molding transcends the simple notion of miniaturization. It embodies the art of achieving impeccable precision and navigating the inherent complexities of creating minute components. A company seasoned in this field will inherently possess a deep-rooted understanding of the nuanced challenges and subtleties that the micro molding process presents, ensuring they produce components that meet the highest standards of quality and functionality. Core assets to look for with any micro molder are an integrated tooling department (do they manufacture their own tools?); experience with the micro molding press of their choice (do they have the right equipment and experience level to operate the technology?); and thirdly the quality equipment and know how to prove the micro component is in specification (can they prove capability in production and hold the micro tolerances on the print?) These are the three key aspects of traditional micro molding so any lack of confidence in these areas may cause problems when you reach the commercialization period of a project.
What materials do you specialize in, and what are their shrinkage rates?
Material shrinkage during molding varies depending on the specific material used. Grasping these differential shrinkage rates is fundamental in the manufacturing process, as it directly impacts the dimensional precision of the final product. The divergence in shrinkage rates poses a significant challenge for manufacturers, especially in the realm of micro molding where precision is paramount. Accurately predicting and understanding these rates is not just a matter of technical knowledge; it's a prerequisite for achieving the desired dimensions and tolerances in the final product. A slight deviation, even in the micrometers range, can render a part useless or incompatible for its intended application. Therefore, a deep comprehension of material-specific shrinkage rates is a cornerstone of ensuring that the final micro-molded product is dimensionally accurate, fit for purpose, and meets the rigorous standards of quality and precision.
An innate understanding and experience of working with as big a library of thermoplastic resins as possible is vital for a micro molder to offer an optimal service. This experience means that the micro molder is able to ask you the right questions to ensure the correct material is used. For example, what environmental conditions will the part need to operate under? Does it need to withstand solder reflow temperatures or other high-heat situations? Does it touch the human body or other bio-materials? Are there lubricity or hydroscopic properties to include or exclude?
Can you provide references or case studies from previous projects?
Assessing a company's track record offers invaluable insights into their proficiency and reliability. Historically, the way a company has executed its projects can often serve as a trustworthy predictor of its ability to deliver in the future. By scrutinizing their past endeavors, one can ascertain the firm's expertise and aptitude in managing comparable tasks, allowing for an informed decision-making process when selecting a potential partner or vendor for new micro molding projects. Most micro moulding companies will publish white papers on their website and many will have examples of prior legacy parts that show the micro scale and tight tolerances on their website. Ask your short-listed micro molder whether they can get close to fulfilling the following.
• Parts up to 1/2" (13mm) in the largest dimension
• Small parts around 800µm (0.031") x 300µm (0.012") x 380µm (0.015")
• Thin wall sections near .004" (.1mm)
• Feature aspect ratios around 6:1
• Part volumes 0.005"3 (0.08 cm3) or less
• Gate size as small as 0.004" (0.1mm)
• Ejector pins as small as 0.010" (0.254mm)
• Full understanding of gate and ejection location
• Full understanding of effect material selection can have on fill and definition of features
How do you ensure repeatability in production?
Repeatability stands as a fundamental pillar in the realm of micro molding. It's not just about crafting intricate components but ensuring that every single piece, even in high-volume production runs, meets the same exacting standards of quality and precision. Such consistency safeguards the reliability of the products, emphasizing the importance of meticulous process control in micro molding projects.
What quality control measures do you have in place?
In the precise domain of micro molding, rigorous quality checks cannot be overemphasized. Given the minute scale and the demand for exactness, any minor oversight can lead to significant product discrepancies. Thus, it's imperative for companies to have a robust quality assurance system in place, ensuring that every micro-molded component aligns perfectly with the set specifications and standards, guaranteeing reliability and excellence in every production run. Micro mold quality assurance begins at the start of each project with design for manufacturability (DfM) reviews to ensure the project is off on the right foot. Then, early in the production process, it is important scrutinize production quality and the robust nature of the process and verify the plan for inspecting and measuring outcomes. From there, its important to develop control plans that address critical features, FMEA results, and other quality requirements. Most experienced micro molders are able to use high-tech and low-tech measurements, and precision gage pins or high-resolution in-line vision systems as necessary. It is also important to use high magnification microscopic measurements to verify tool and finished part dimensions. Proper product handling is also a necessary consideration in quality assurance. Surface contamination can be a nuisance - or a catastrophe - for delicate component features. For these types of parts, automation and clean room molding options are recommended.
How do you handle mold design and validation?
The efficacy of the mold design and its validation process is pivotal in determining the quality of the final micro-molded product. An optimized and streamlined design process not only guarantees superior outcomes but also offers the dual benefits of cost efficiency and swifter turnaround times. Companies that invest in refining these processes are better positioned to deliver high-quality products while achieving operational savings and timely deliveries.
What is your production capacity and lead time?
Ensuring a company's capability to meet specific volume demands and adhere to set timelines is paramount in a production partnership. This not only reflects their operational efficiency but also their commitment to client satisfaction. By verifying these capabilities upfront, one can establish a foundation for a reliable and seamless collaboration, minimizing potential disruptions and guaranteeing timely product deliveries. Most customers look for scale - can my suppliers meet my production demands and hold the required tolerances?; capability--- does my micro molder have the assets in place to be successful in micro in size, micro in tolerance, and/or micro featured parts; sustainability - will my supplier be viable long term with a strong balance sheet.
How do you manage tool maintenance and longevity?
Consistent maintenance of molds is a critical step in ensuring their prolonged usability and efficiency. By upkeeping the molds, companies can assure that the quality of the products remains consistent over time. Additionally, this diligent approach helps in preempting and minimizing sudden production disruptions. In essence, regular mold maintenance serves as a safeguard against compromised product quality and unplanned production halts, ensuring a smooth and dependable manufacturing process.
Do you offer any post-molding services like assembly or packaging?
In the intricate world of micro molding, ensuring a company's capabilities and expertise is paramount for clients who require high-volume and repeatable production. While the molding process itself is essential, what happens after the molding can significantly influence the quality and reliability of the final product. For prospective customers of micro molding companies, it's vital to inquire about post-molding services. Depending on the precise needs of a project, these subsequent services can be the defining factor in achieving the desired specifications and finish for micro molded parts. As such, customers should prioritize asking detailed questions about a company's post-molding procedures and capabilities to guarantee that the end product not only meets the set standards but is also delivered consistently across large batches.
How do you address unforeseen challenges during production?
The realm of micro molding, given its intricate nature, often presents unpredictable challenges. The minute dimensions and precision required can lead to unexpected complexities during the production process. In such a nuanced field, the true measure of a micro molding company isn't just in its ability to produce but also in its capacity to swiftly adapt and address these unforeseen challenges. As customers navigate the market, they should recognize that a company's adaptability and proactive problem-solving approach can significantly set it apart from competitors, making it a crucial differentiator when selecting a reliable partner in micro molding.
Do you have any certifications relevant to my industry?
In industries where precision and compliance are paramount, such as healthcare, the importance of certifications cannot be overstated. These certifications serve as more than just badges of honor; they are tangible evidence that a company consistently meets and upholds industry-specific standards and practices. By obtaining and maintaining these credentials, a company signals its dedication to excellence and its commitment to delivering products or services that are safe, reliable, and of the highest quality. For stakeholders, certifications act as a reassuring benchmark, indicating that they are partnering with an entity that understands and respects the nuances and demands of their particular industry. Companies should look for the following ISO standards when choosing a reputable micro molder. ISO 13485, ISO 9001, and ISO 14001 certificates which should be updated with the certificate of registration effective date, expiration date, and certification number displayed on their website or available to be reviewed.
What technologies and machinery do you employ in the micro molding process?
In micro molding, the role of modern technology cannot be emphasized enough. Employing up-to-date technology not only elevates the overall quality of the molded products but also boosts efficiency, ensuring that projects are completed in a timely manner. Furthermore, the latest technological advancements play a pivotal role in guaranteeing repeatability — a critical factor when producing high-volume batches that must maintain consistent specifications. Thus, for companies or individuals seeking a partner in the micro molding industry, the adoption and application of contemporary technology or the bespoke in-house development of cutting edge technology solutions by a firm stands as a key indicator of its ability to deliver superior and consistent results.
How do you handle design changes or iterations during the project?
In the dynamic landscape of product development and manufacturing, design iterations are often an inevitable part of the journey. As such, a company's ability to be flexible and swiftly accommodate these design changes becomes paramount. Such flexibility not only demonstrates a company's commitment to customer satisfaction but also leads to significant savings in both time and resources. By pre-emptively addressing and integrating modifications, potential roadblocks are avoided, ensuring a smoother and more efficient production process. Therefore, when selecting a micro molding partner, it's wise to prioritize those that showcase this adaptability, as it can greatly influence the overall success and cost-effectiveness of a project.
How do you stay updated with industry trends and technological advancements?
In today's rapidly evolving business environment, a company's commitment to continuous learning and adaptation becomes a hallmark of its long-term viability. Such companies don't just rest on their past laurels; instead, they are in a relentless pursuit of knowledge, ensuring they remain at the forefront of industry trends and innovations. By fostering a culture of ongoing education and adaptability, they position themselves to offer solutions that are not only effective but also attuned to modern requirements and challenges. For clients and partners, collaborating with such forward-thinking entities often translates to better outcomes, innovative approaches, and a shared journey of growth and evolution.
SUMMARY
Finding the right micro molding company requires due diligence and a deep dive into their capabilities and methodologies. The answers to these questions will not only give you confidence in your partner but also ensure that your micro molded parts are of high quality, delivered on time, and produced repeatably. Remember, it's not just about finding a vendor but forging a partnership for mutual success.
www.accu-mold.com
Paul Runyan is VP of Sales at Accumold. Accumold has grown to a 130,000 square foot fortified facility designed for assurance of supply, employs over 350 staff, and is a net exporter shipping all over the world every day from its Ankeny, IA, USA facility which runs 24 hours a day, 7 days a week.
Featured Product
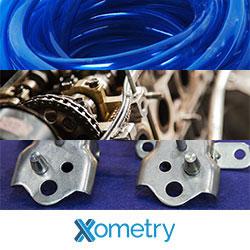
Get RFQs on Die Casting, Stamping, and Extrusion With Xometry, Your Source for Custom Parts
Xometry is your source for custom parts. Now, in addition to getting instant quotes on 3D Printing, CNC Machining, Sheet Metal, and Injection Molding, customers can create and send RFQs for die casting, stamping, and extrusion work to our nationwide network of pre-vetted manufacturers with just a 2D drawing. You will receive and be able to review responses from qualified shops within 7 days on an advanced web-based RFQ management platform. To learn more go directly to our site to issue and RFQ today. Stop wasting time managing RFQs through email and by phone, and start issuing RFQs at scale and in the cloud.