Digital platforms: the present and future of the manufacturing industry to transform and automate processes
Today it's commonly consented that digital technology applied to manufacturing development stands out as the principal resource to alleviate hardships and bolster the resilience and preparedness of manufacturing and supply networks.
Worldwide manufacturing and supply networks are undergoing a digital revolution within Smart Manufacturing and Industry 4.0; nowadays, there's a bigger demand for greater efficiency, flexibility, and competitiveness, all in a rapidly changing global marketplace. These changes are shapeshifted through new technologies, which empower organizations to make data-driven decisions, improve operations, reduce costs, and meet the demands of today's consumers.
Given that circumstance, day to day these companies adopt new digital tools and explore the opportunities presented by big tech milestones such as artificial intelligence (AI) to establish digital supply networks; this disruption scenario, just to be precise, reached new heights when the world was confronted with one of the most significant disruptions in modern history—the COVID-19 pandemic.
Now, numerous businesses are grappling with existential post-pandemical threats and striving to survive in the short term; just in 2020 alone, an estimated loss of US$30 billion occurred from the result of development projects for the manufacturing industry. One of the most affected markets was the US automotive market. With sales higher than 17 million vehicles in the years previous to COVID-19, the country represented the second-largest market of automobiles in the world (The Wall Street Journal, 2019).
To provide a greater context, it's implied that when COVID-19 broke out, more than 400,000 employees and suppliers of the automotive industry were severely affected, with incalculable accumulated losses up until today.
As of today, the pandemic has left many new lessons and perspectives for the manufacturing industry worldwide. Today it's commonly consented that digital technology applied to manufacturing development stands out as the principal resource to alleviate hardships and bolster the resilience and preparedness of manufacturing and supply networks.
Newly developed manufacturing companies are deploying more intelligent and smart technologies, and the productivity of their system has been found to have increased by 17-20%.
This increment is directly associated with the premise of the companies to boost competitiveness, having shorter responses to market changes while lowering costs; clear and cut, it's process innovation through technology that's pushing the transformation in the manufacturing industry.
Under the goal of helping the industry's companies to accomplish effectiveness, new tools and solutions arise, such as Kiuey, from PPAP Manager Corp.; from its operations launching, this company technology has developed different SaaS (software as a service) products to streamline the critical supplier quality management processes in every industry possible.
With its initial digital product, PPAP Manager from Kiuey (now part of the different set of module-based platforms known as "Kiuey"), the company has arranged to develop a consistent and diverse customer base that nowadays brings significant data to the industry trend of using digital technologies to improve manufacturing workflows.
As of 2023, Kiuey reports that companies can save between 40%-50% of the time and resources usually spent manually managing these same processes. This company listing includes high-impact organizations from the electronics, automotive, medical devices, aerospace, and consumer goods industries.
This is just one example of how new companies are delivering solutions for an ever-evolving landscape.
As 2023 reaches its end, the manufacturing landscape in the USA is transforming seismic proportions. As we gear up for the start of 2024, the world of manufacturing management stands at the threshold of change; that's why it's essential to gain insights that redefine strategies, boost competitiveness, and ensure compliance, now more than ever.
Featured Product
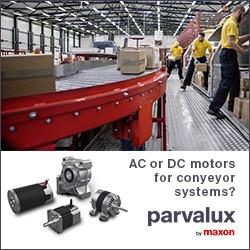