SECS/GEM for Non-GEM/SECS Equipment: Enabling Connectivity and Control
Discover how to integrate non-GEM/SECS equipment into the SECS/GEM environment for seamless communication, data exchange, and enhanced control in manufacturing operations. Explore conversion units, custom software development, and equipment-specific adapters as solutions.
In the manufacturing industry, equipment communication and control are critical for efficient operations and process optimization. The Semiconductor Equipment Communications Standard/General Equipment Model (SECS/GEM) protocol has long been the industry standard for enabling communication between manufacturing equipment and factory control systems. However, not all equipment is equipped with native SECS/GEM capabilities, presenting a challenge for integration and data exchange. In this blog post, we will explore SECS/GEM for non-GEM/SECS equipment and discuss various approaches to enable connectivity and control.
Understanding SECS/GEM
SECS/GEM is a standardized communication protocol widely used in semiconductor manufacturing environments. It provides a structured framework for equipment and host systems to exchange information, enabling real-time data collection, recipe management, equipment control, and more. SECS/GEM facilitates communication through messages, which are predefined data structures carrying specific information between the equipment and the host system.
Challenges with Non-GEM/SECS Equipment
While SECS/GEM offers numerous benefits, many older or non-semiconductor equipment may lack native support for the protocol. Upgrading or replacing such equipment can be costly and disruptive to manufacturing processes. However, integrating non-GEM/SECS equipment into the SECS/GEM environment is possible through various methods.
SECS/GEM Conversion Units
SECS/GEM conversion units act as intermediaries between non-GEM/SECS equipment and the host system. These units typically include hardware and software components that translate between the proprietary protocol of the equipment and the SECS/GEM protocol used by the host system. The conversion unit acts as a bridge, enabling seamless communication and data exchange between the two systems.
Custom Software Development
Another approach involves developing custom software to interface with non-GEM/SECS equipment. This method requires a thorough understanding of the proprietary protocol used by the equipment, as well as the SECS/GEM protocol. The custom software acts as a middleware layer that translates the communication between the equipment and the host system, allowing seamless integration.
Equipment-specific SECS/GEM Adapters
Some equipment manufacturers offer equipment-specific SECS/GEM adapters or add-on modules that can be retrofitted to existing non-GEM/SECS equipment. These adapters are designed to provide SECS/GEM compatibility without requiring a complete replacement of the equipment. They often come with preconfigured settings and interfaces, simplifying the integration process.
Benefits of SECS/GEM Integration
Integrating non-GEM/SECS equipment into a SECS/GEM environment offers several benefits:
Enhanced Data Collection: SECS/GEM integration allows real-time data collection from non-GEM/SECS equipment, providing valuable insights for process monitoring, yield improvement, and predictive maintenance.
Standardization: By integrating non-GEM/SECS equipment into the SECS/GEM environment, manufacturers can standardize their communication protocols across the factory, streamlining operations and reducing complexity.
Equipment Control and Monitoring: SECS/GEM integration enables centralized control and monitoring of non-GEM/SECS equipment, allowing operators to manage equipment settings, initiate actions, and receive status updates from a single interface.
Seamless Integration with Host Systems: With SECS/GEM integration, non-GEM/SECS equipment becomes seamlessly compatible with other SECS/GEM-enabled equipment and factory control systems, fostering a connected and efficient manufacturing ecosystem.
Conclusion
SECS/GEM is a powerful communication protocol that has revolutionized semiconductor manufacturing. While not all equipment supports native SECS/GEM capabilities, integrating non-GEM/SECS equipment into the SECS/GEM environment is possible through conversion units, custom software development, or equipment-specific adapters.
Featured Product
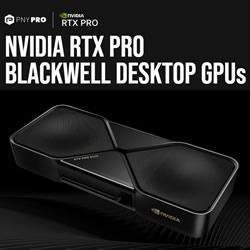