How to Implement a Successful Predictive Maintenance Program in Your Factory
Maximize equipment uptime and minimize downtime with a successful predictive maintenance program. Implement a proactive approach to maintenance by utilizing data and technology to predict equipment failures and prevent them from occurring. Start by identifying critical equipment, establishing a data collection system, and training personnel on data analysis. Implementing a predictive maintenance program can result in increased efficiency, reduced costs, and a safer work environment.
Implementing a successful predictive maintenance program in your factory can result in significant cost savings, increased uptime, and better overall equipment efficiency. In this article, we'll outline the key steps you need to take to ensure your predictive maintenance program is effective and efficient.
Define your goals
The first step in implementing a successful predictive maintenance program is to define your goals. You should identify the critical equipment in your factory and set specific goals for each piece of equipment. These goals should include reducing maintenance costs, improving equipment uptime, and reducing unplanned downtime.
Choose the right technology
Once you have defined your goals, the next step is to choose the right technology for your predictive maintenance program. There are various technologies available, including vibration analysis, thermography, and ultrasonics. Each technology has its own advantages and disadvantages, and it's essential to choose the technology that is best suited for your factory's equipment.
Collect data
Data collection is a critical step in a predictive maintenance program. You need to collect data on your equipment's performance, such as temperature, vibration, and noise levels. This data will be used to analyze the equipment's performance and predict when maintenance is required.
Analyze the data
Once you have collected data, you need to analyze it to identify trends and patterns. This analysis will enable you to predict when equipment maintenance is required and schedule maintenance accordingly. Analyzing the data will also help you identify potential equipment failures before they occur, allowing you to take preventative action.
Schedule maintenance
Based on the data analysis, you can schedule maintenance proactively, ensuring that equipment is maintained when required, rather than waiting for a breakdown to occur. Scheduling maintenance in this way can result in significant cost savings and increased equipment uptime.
Monitor the program
Once your predictive maintenance program is in place, it's important to monitor it regularly to ensure it's working as intended. You should track the performance of your equipment and compare it to your goals to identify any areas where improvements can be made.
Continuously improve
Finally, it's essential to continuously improve your predictive maintenance program. You should regularly review your data collection, analysis, and maintenance scheduling processes to identify opportunities for improvement.
In conclusion, implementing a successful predictive maintenance program in your factory can result in significant cost savings and increased equipment uptime. By following the steps outlined in this article, you can ensure that your predictive maintenance program is effective and efficient. Remember to define your goals, choose the right technology, collect data, analyze the data, schedule maintenance, monitor the program, and continuously improve.
Featured Product
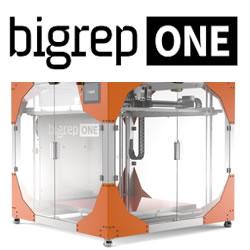