Ugogo Expands Into the AM Reseller Business
Ugogo Represents the World's Most Disruptive AM Technologies
August 10, 2022, Boston, MA - Frank Marangell, a veteran in the Addative Manufacturing (AM) industry and Steven Rizzo, an 8-year AM sales leader, bring years of 3D printing knowledge to building a reseller organization. The Ugogo business model is dedicated to selling AM products. Beyond system sales, Ugogo is a customer-oriented organization offering streamlined services and one stop shopping for 3D printers and consumables. Unlike other resellers, that tend to focus on software, Ugogo is focusing on AM technologies for manufacturing.
"3D printing technologies are rapidly advancing but customers are not able to purchase the next generation of AM solutions because many of those great companies are not well represented in the US market. Ugogo is here to change that" stated Frank Marangell, Ugogo's CEO.
Ugogo offers their customers next generation technologies. They have partnered with innovative choices in the AM market that will easily compete with the status quo. Advanced 3D printing companies partnered with Ugogo: BCN- desktop printers, Bigrep- large format printing, Photocentric -LCD technology, Raplas-SLA technology, Roboze-FFF-technology, Sintratec-SLA technology, Core Technologies 4D Additive- AM software, and NFrontier-3D printing design
"As our industry continues to consolidate there is a disconnect between a customer's application and the available AM systems. It's the dilemma of fitting a square peg into a round hole. At Ugogo we can hand pick advanced technologies that provide precise customer solutions to boost their productivity." According to Steven Rizzo.
Ugogo is concentrating its efforts on the core 3D printing markets which include aerospace, automotive, dental, medical, industrial and manufacturing, providing their customers with advanced 3D printing innovations.
Featured Product
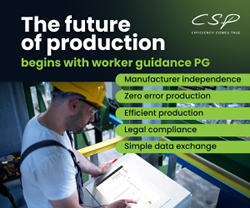