PEKO Adopts 5S Lean Manufacturing Methodology Company-Wide
PEKO to improve efficiency with 5S, a visually oriented system of cleanliness, organization, and arrangement that facilitates greater productivity, safety, and quality.
PEKO is excited to announce the implementation of 5S lean manufacturing methodology, a new company-wide continuous improvement initiative to improve workplace organization and efficiency and eliminate waste.
This 5S initiative kicked off in February 2021 with the objective of optimizing productivity, ensuring an effective operational flow in production environments, and laying the groundwork for the successful implementation of lean manufacturing.
PEKO's 5S program includes the following steps:
1. Sort: Sorting out necessary and unnecessary items and eliminating what is not needed.
2. Set in Order: Arranging all necessary items in a location that is visually designated.
3. Shine: Cleaning equipment and organizing work areas to maintain on a continuous basis.
4. Standardize: Developing procedures and standards to consistently maintain the first 3 S's.
5. Sustain: Gain organizational commitment to properly maintain correct 5S procedures.
The Company is providing training in the form of classroom instruction and hands-on interaction with production employees. 5S tools being utilized include sorting, red-tagging, creating logs, cleaning (machines, floors, walls, shelves, etc.), creating shadow boards, and setting schedules for cleaning, auditing, and educating the workforce.
The benefits of 5S include:
- Work areas are safer and cleaner because tripping hazards and other dangers are eliminated.
- Production downtime is minimized because tools and materials have been organized and streamlined for improved workflow.
- Floor space is utilized more effectively because unneeded items are eliminated.
- Company culture is improved because the initiative fosters better teamwork and enthusiasm.
"Implementation of 5S has enhanced our company's morale, efficiency, safety, and increased cost savings," said Adriana Mousso, Lean Manufacturing Specialist at PEKO. "The 5S program is another example of our commitment to continuously examine and improve every aspect of our operations which in turn adds value for our customers."
PEKO has dedicated a team of individuals responsible for enforcing the continuous implementation of these 5S principles. 5S audits are being performed on a rotating and regular basis by department employees.
PEKO Precision Products is a leading contract manufacturer providing turnkey manufacturing solutions for machinery, equipment, and major electro-mechanical assemblies. PEKO's capabilities span the entire product lifecycle, including design, engineering, development, machining, sheet metal fabrication, electrical integration, assembly, and full-scale production.
Featured Product
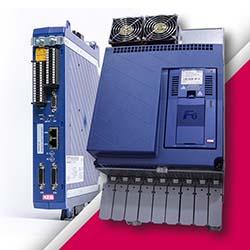
KEB VFDs for High Speed Motor Control
KEB's VFDs are the key to unlocking peak performance in your high-speed machinery. Engineered for precision control, even without feedback sensors, our F6 and S6 drives utilize advanced software and high-frequency output. This ensures smooth operation, reduced vibration, and optimal efficiency. Whether you're building turbo blowers, power generation systems, or other high-speed applications, KEB VFDs deliver the reliability and performance you need.