WAYLAND ADDITIVE TAKES POLE POSITION AS EBEAM-BASED METAL AM SYSTEMS PROLIFERATE AT FORMNEXT
Wayland Additive showcased its Calibur3 technology at the recent Formnext exhibition, and the company was struck by the enormous interest in its metal AM technology — driven by the NeuBeam process — which overcomes many of the pitfalls associated with traditional eBeam and laser powder bed fusion (PBF) metal AM processes.
(15th December 2021, Huddersfield, U.K.) Wayland Additive showcased its Calibur3 technology at the recent Formnext exhibition, and the company was struck by the enormous interest in its metal AM technology — driven by the NeuBeam process — which overcomes many of the pitfalls associated with traditional eBeam and laser powder bed fusion (PBF) metal AM processes.
Will Richardson, CEO at Wayland comments, "Formnext was a great event for us, and it was encouraging to see that despite the recent COVID-related issues, industry and innovation have not stood still. One big and obvious trend is the resurgence of eBeam technologies, with a number of recently introduced technologies showing themselves for the first time in Frankfurt. I think it is fair to say that Wayland leads this charge, not just in terms of the maturity and commercial availability of our offering — with Wayland being the only company to have a physical production machine in place at the event — but also in terms of evolving the eBeam process to overcome the significant issues that hold back adoption of legacy and alternative eBeam technologies."
Wayland's innovative NeuBeam process has been designed to overcome the lack of stability both in terms of the machines and their output, which has traditionally been a drawback for eBeam technologies. This is a consequence of both process issues and the constraints of existing machine capabilities. Competing metal AM processes, most notably L-PBF also bring production challenges.
Ian Laidler, CTO at Wayland says, "With the laser PBF process residual thermal stress, low productivity, the challenge of process monitoring, limited part volume, and limited process control parameters restrict the process dynamics and the optimisation options that are available to the user. This in turn has led to machine makers and customers turning to material scientists to develop new materials dedicated to the AM process, in an attempt to overcome such limitations. It is interesting to note that huge sums of money are now being spent in the industry trying to develop "forgiving" materials in order to get around the issues presented by both laser PBF and traditional eBeam PBF systems. This may be one way of solving the problem, but the strategy of relying on bespoke materials for targeted applications may further add to the cost of AM. Powder producers need to be able to produce large volumes in order to reduce costs, rather than providing a wide range of specialist alloys. With the eBeam process, the problem of powder charging — that alliance between the machine and the material — means that the process stability and breadth are immediately and severely compromised."
NeuBeam delivers on all of the advantages of metal eBeam PBF technology, while overcoming the troublesome issues that have traditionally limited wider adoption.
Richardson continues, "The most fundamental issue with eBeam AM technology has always been the unstable nature of the processes and Wayland has categorically resolved this. The Wayland team comprises decades of experience with eBeam research, development and implementation in the semi-conductor industry. This has allowed us to address and solve the charging issues that have, until now, restricted eBeam processes, with the fully neutralized NeuBeam process. The other key feature of NeuBeam is that it is a hot part process rather than a hot powder bed process like traditional eBeam processes. Therefore, Calibur3 can efficiently produce parts that are free of residual stresses because the high temperatures are only applied to the part and not the whole powder bed, ensuring free-flowing powder post-build (no sinter cake) and stress-free parts with reduced energy consumption. This makes the process considerably more flexible in terms of part geometries and cost-efficient because heat treatments and other post processing steps are dramatically reduced. NeuBeam is also material agnostic and is therefore able to process a much wider palette of metal materials that alternative eBeam processes, including refractory metals."
NeuBeam also offers significant advantages over other technologies with built-in real-time in-process monitoring, allowing for rapid material development or tuning of microstructures by adapting the solidification during manufacture. With NeuBeam the process temperature is not constrained by sintering the powder bed, allowing the process temperature to be optimized to the material microstructure and/or the application. Being a true thermal process, everything in the build chamber is able to be monitored, and it is possible to see the true temperature of the whole powder bed in-process as a build takes place. The thermal history of the material being processed can also be seen, as can the topography of the surface so that defects can be detected — and reported — as they occur.
www.waylandadditive.com
About Wayland Additive
NeuBeam technology has been developed in-house from the ground up by a team of physicists that have worked for many decades with electron beam technology and industrial systems in the semi-conductor industry. The science, combined with extensive expertise and experience has allowed Wayland Additive to develop a very capable and reliable system rather than imitating existing systems or adapting off-the-shelf components and re-purposing them.
Featured Product
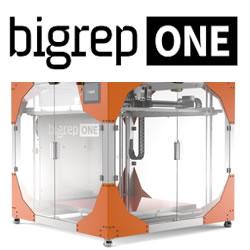