helping streamlining SAE competition results with 3D printing and composite materials
CRP USA will be attending the PRI Trade Show 2019 along with Pro-System Inc., booth #1041, Green Hall. To the great interest of show attendees from every type of racing discipline, it will be disclosured - non only, but also - how it is possible to manufacture different oil pans using laser sintering technology and high performance composite material and to defeat Formula SAE challenges via Additive Manufacturing
CRP USA will be attending The PRI Trade Show 2019 (Indiana Convention Center, Indianapolis, from 12th to 14th December 2019) at booth 1041, Green Hall, with Alcon Specialist Brakes & Clutches and Pro-System Inc.
For the last four years of SAE competition, UVic Formula Motorsport team has been using 3D printed oil pans that were purposely engineered to be manufactured by CRP USA's laser sintering 3d printing process and Windform® TOP-LINE composite materials.
The oil pans for the 2016, 2017 and 2018 vehicle were printed using Carbon-composite material Windform® XT 2.0.
It worked "amazingly" on the 2016 and 2017 race car as the 3D printed oil pans allowed UVic team to significantly lower the engine, and thus decrease the vehicles overall centre of gravity improving the performance of the car.
During a test day with their 2018 vehicle, the engine overheated causing the oil temperature to increase beyond the limits of the designed pan. During the post inspection it was found that any thin walled surfaces deformed quiet significantly, meaning that the baffle walls of the pan were significantly warped, and one of the sections of the mating flange had been pulled into the pan creating a significant leak.
The team decided to re-evaluate all of the Windform® TOP-LINE range of high performance materials available from CRP USA for the 2019 vehicle, and chose to go with Carbon-filled Windform® SP composite material due to its higher melting point as compared to Windform® XT 2.0. However, the team increased the thickness of the mating flange to allow for a large amount of surface area for an aluminum pressure flange.
The changes resulted in a more robust oil pan.
Featured Product
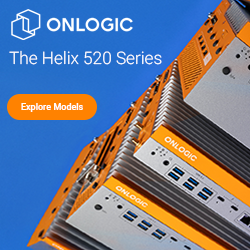