Rethink Manufacturing with 3D Systems' Production Workflow Solutions at RAPID+TCT 2019
3D Systems will showcase its unique metal solutions that help manufacturers scale factory productivity. Attendees can also explore the company's powerful software portfolio that enables seamless 3D digital workflow integration.
Attendees of the RAPID+TCT event this year can view 3D Systems' (NYSE: DDD) digital manufacturing solutions and talk with the company's experts in booth 1227. In addition to the latest Figure 4® configuration, as well as new Figure 4 and selective laser sintering (SLS) material offerings for production solutions, 3D Systems will showcase its unique metal solutions that help manufacturers scale factory productivity. Attendees can also explore the company's powerful software portfolio that enables seamless 3D digital workflow integration. In addition, there will be an opportunity to learn more about 3D Systems' On Demand services which provide customers with options to outsource manufacturing capabilities, or supplement factory capacity.
New Production-grade Nylon Material for Expanded Applications
3D Systems is announcing DuraForm® ProX EX NAT (planned availability June 2019). This new material joins the company's portfolio of production-grade nylons for its SLS 3D printers. DuraForm ProX EX NAT is a tough, impact-resistant natural colored PA 11 nylon material that handles the rigors of repeated cycling and use, even in harsh environments. It enables consistent production of natural white color parts that can replace injection molded ABS and polypropylene. Its durability makes it especially suitable for applications like snap fits and living hinges requiring hundreds of open-close cycles, as well as testing in real-life scenarios like crash tests or other stress simulations.
3D Systems' Customers Showcase Manufacturing Transformation
There will also be several opportunities to hear 3D Systems' customers speak about the benefits they're realizing from the company's solutions including:
Vyomesh Joshi, 3D Systems' president and CEO, will moderate a customer panel focused on the Industrialization of Additive Manufacturing, Wednesday, May 22, 12:30-1:30 pm. During this session, hear from Stewart-Haas Racing, rms Company and Nokia to learn how 3D printing is driving manufacturing transformation at these companies.
Dr. Ken Gall, chair of the Department of Mechanical Engineering and Materials Science, Duke University, will deliver a session titled "Compressive and Tensile Fatigue Behavior of Gyroid-Based Titanium Alloy Scaffolds Produced by Direct Metal Printing" on Wednesday May 22, 11:45-11:55 am.
Customer and application engineering presentations will run in 3D Systems' booth throughout the event.
Jim Hall, chief engineer, Jay Leno's Garage will present his experiences with 3D scanning with Faro scanners and 3D Systems' Geomagic® reverse engineering software to deliver one-off custom parts for classic cars.
Terry Hill, CEO and founder, Rapid Application Group will share his work as an additive manufacturing service bureau using 3D Systems' SLS, Figure 4 and ProJet MJP 2500 IC 3D printers.
Mike McLean, general manager, 3dprintedparts.com will discuss conformal cooling design with 3D Systems' 3DXpert™ additive software and metal production of injection mold inserts, as well as part production with the Figure 4 Standalone 3D printer.
Featured Product
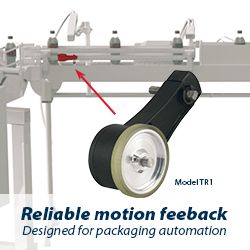