Making Additive Manufacturing a True Production Technology
euspen and ASPE are set to co-host a Special Interest Group Meeting that focuses on the areas of key concern to manufacturers as they move to the adoption of additive manufacturing as a serial production technology.
(Cranfield, United Kingdom, 8th May 2019) The use of additive manufacturing as a rapid prototyping technology has become universally accepted across all key industrial sectors, allowing design engineers and manufacturers the ability to assess the robustness of a design before pushing the button on full production. A rapid prototype can be held and assessed by all departments involved in the design to manufacturing cycle, and design iterations can be made before expensive tooling and associated processes are initiated.
However, to use additive manufacturing as a direct manufacturing process, there are numerous considerations that must be assessed, not least the fact that accuracy must be constantly maintained and measured to ensure compliance with design intent in what could be safety critical end-use applications.
It is in the area of dimensional accuracy and surface finish that the European Society for Precision Engineering and Nanotechnology (euspen) will be focusing on its upcoming Special Interest Group (SIG) meeting 16-18 September 2019. The SIG will this year be held in the Ecole Centrale de Nantes, Nantes, France, and represents the 6th time that euspen has joined forces with the American Society of Precision Engineering (ASPE) looking at important issues surrounding precision in AM.
It has been found that additive manufactured parts and components can exhibit issues related to dimensional accuracy. For example, prismatic parts show two types of errors — variation in the linear dimension and variation in the hole diameter. These errors and others that characterise other additive manufactured parts have to become the focus of intensive research and analysis to overcome the limiting effect they can have on the use of the technology in end-use production applications.
It is important that designers and manufacturers have a detailed knowledge of additive manufacturing processes (of which there are many) to understand where they may expect differences between expected and actual dimensional accuracy.
In general terms, there are two key factors that affect dimensional accuracy in additive manufacturing, the material out of which a part is to be made, and the design of the part — design for additive manufacturing (DfAM) becoming a critical area of focus, and one that is covered in depth at the euspen SIG.
The link between accuracy and material used is obvious. In some instances, for example, part accuracy is compromised in the quest to enhance a specific material property, i.e. more flexibility may be required than a standard AM material allows, and accuracy is reduced as flexibility increases.
But design is perhaps the key factor that affects accuracy. Design engineers must be cognisant of the advantages and disadvantages in terms of accuracy of each individual AM process, specifically the effect of variations in cooling and curing that result in internal stresses that can lead to shrinkage and warpage, the effect of part size on dimensional accuracy, and the effect of supports used during build not just on dimensional accuracy but also surface finish.
euspen draws on experts from across all disciplines that need to be considered when looking at precision-related issues in a manufacturing environment. The SIG looks at issues related to industry standards for AM that allow engineers to design to a known set of parameters and build a level of trust in the fulfillment and manufacturing process. They are part of the necessary evolution of the technology and are central to discussions at the SIG as AM moves from a prototyping tool to a production tool.
Metrology is also of central importance. The goal with all metrology is to keep processes under tight control, therefore improving quality, reducing scrap rates, and enhancing environmental sustainability. For AM platforms, new solutions are needed to ensure optimization of the technology as a truly integrated production alternative.
The local hosts and organising committee for the SIG are Prof. Alain Bernard from Ecole Centrale de Nantes; Dr David Bue Pedersen from Technical University of Denmark; Prof. Richard Leach from University of Nottingham; and Dr John Taylor from University of North Carolina at Charlotte. The AM SIG meeting chair is Prof. Richard Leach from University of Nottingham, and Dr John Taylor from University of North Carolina at Charlotte.
To find out more about the event please visit www.euspen.eu, or contact Dishi Phillips Business Development Manager at euspen on t. +44 (0)1234 754023 e. dishi-phillips@euspen.eu.
About euspen
The European Society for Precision Engineering and Nanotechnology (euspen) is an influential community linking industrialists, researchers, respected authorities, new, and established players worldwide. It provides an entrepreneurial platform that enables companies and research institutes to promote their latest technology developments, products, and services and keep up to date with those in the field. euspen's defined mission is to advance the arts, sciences and technology of precision engineering, micro engineering and nanotechnology; to promote its dissemination through education and training; and to facilitate its exploitation by science and industry. www.euspen.eu
Featured Product
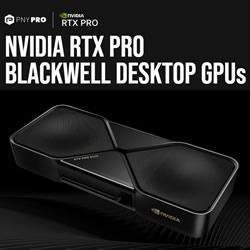