Automate 2019: Guidance Automation to Showcase Autonomous Mobile Robot Technologies
Key Guidance, Navigation and Control technologies that drive mobile robots are on display in Automate Booth N6074.
LEICESTER, UK (March 28, 2019) — The latest industry-proven traffic management, vehicle control and localization technologies that guide and drive Autonomous Mobile Robots (AMRs) will be displayed by Guidance Automation (guidanceautomation.com), a part of Matthews International's Applied Technologies Group, throughout Automate 2019 in Booth N6074. The expo will be held in the North Hall of Chicago's McCormick Place, April 8-11, 2019.
The Guidance Automation exhibit will feature solutions for "Accelerating Autonomous Mobile Robot Development," particularly those utilized in logistics applications. In-booth displays detail Guidance Automation's 25-plus years of robotic innovations that help vehicle makers and automation solutions providers:
• Develop and deploy new AMRs and Automatic Guided Vehicles (AGVs)
• Upgrade existing AGVs from line-following technology
• Automate a wide range of electric vehicle types, including tow tractors, forklifts, pallet trucks, heavy lift platforms and more
"This is our first exhibit at Automate, and we are excited to showcase our AMR technologies and solutions," noted Peter Moore, Commercial Manager. "Our aim is simple. Advance navigation technology development in order to enable our clients to keep pace with increasingly demanding market needs. The only way to do this is to start with end user processes, understand their working practices, and develop technologies that respond to those utilizations. We focus on implementing integrated automation solutions that align with process need, ultimately delivering mobile robots that reduce errors and increase fulfillment speed, accuracy and scalability."
Featured technologies include:
SCENE: Laser/Vision-based Natural Feature Navigation for AMRs | An intelligent, laser-based Natural Feature navigation system that functions without wires, tapes or navigation marks. Instead, the technology allows AMRs to navigate by reference to existing features. The system utilizes advanced 2D/3D Laser contour scanning and mapping algorithms to generate a navigation map from the available features within the working environment. These mapped features are used to determine vehicle position during vehicle operation. SCENE may be specified with options for indoor and outdoor operation, and supports a wide range of laser types, including safety scanners and hi-fidelity 360° scanners.
moNitrav™: Scalable Traffic Management System for Material Handling Applications | Comprising dynamic task scheduling and route generation, moNitrav manages the movement of AMRs throughout the work environment to ensure optimal process throughput and effective use of resources. Harnessing the power of Industry 4.0, moNitrav provides:
• Dynamic route and task optimization for "always on fast track" operation
• Real-time adaptability to changing demands and throughput requirements
• On-demand task injection and prioritization
• On-route task cancellation/re-routing
• Easy interface to warehouse management, production management and a range of specialized materials handling systems (such as baggage handling)
kingpiN™: A Versatile, Industry Proven Controller Specifically Designed for AMRs | As a generic AMR controller, kingpiN supports all vehicle drive configurations and acts as the central component of a scalable Guidance, Navigation and Control solution. Specifically designed and built for robotic vehicle applications, the smart controller accelerates vehicle development without compromising the user's control of vehicle functionality. It works with a range of navigation/localization technologies, as well as with third-party traction and steer motor drives. A truly modular solution, kingpiN maximizes user choices and easily adapts to variable application needs.
Wednesday, April 10: On-Floor Seminar Presentation | In addition to the Automate display, Guidance Automation's Dr. Paul Rivers, Managing Director, will join two experts from Matthews Automation Solutions (matthewsautomation.com) to present a free, on-show-floor educational seminar in the co-located ProMat 2019 exhibition's South Hall. "Using Proven Material Handling Automation and Emerging Bot Technologies to Optimize Direct-to-Consumer (DTC) Order Fulfillment" will occur on Wednesday, April 10, from 10:30 a.m. to 11:15 a.m. in Theater I.
Rivers will draw on Guidance's 25+ years of providing robotic technologies to introduce today's state of the art autonomous solutions. This includes hardware and software advances designed to maximize intelligence, performance, safety and application flexibility.
"The front line of Autonomous Mobile Robot (AMR) and Automatic Guided Vehicle (AGV) development focuses on reducing errors, increasing throughput and maximizing operational efficiency, while doing so on a scalable, adaptable platform that flexes with changing demand and requirements," shares Rivers. "AMRs should further create opportunities to integrate and collaborate with proven material handling systems to optimize all resources."
Representatives from Guidance Automation's U.S. and U.K. locations will be available to discuss how the company's solutions can accelerate the development of AMRs. Visit Booth N6074 throughout Automate 2019 in Chicago's McCormick Place North Hall, April 8-11, 2019. Appointments may be scheduled in advance via bit.ly/GA_Appt
# # #
ABOUT GUIDANCE AUTOMATION
Guidance Automation (guidanceautomation.com), a part of Matthews International's Applied Technologies Group, has more than 25 years of experience developing advanced autonomous mobile robot technologies for the global robotic vehicle market and has thousands of systems in service.
Featured Product
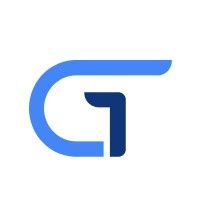
RCO Series x86 Super-Rugged Industrial Computers
Premio's RCO Series redefines rugged edge computing by offering comprehensive solutions optimized to meet the demands requirements of Industry 4.0 edge AI applications. With super-rugged durability, real-time performance capabilities with x86 Intel processors, extensive IoT connectivity, and scalable EDGEBoost technologies, this series of industrial computers are engineered to excel in diverse high-specification deployment challenges. From AGV/AMR deployments to smart manufacturing, the RCO Series is fully optimized to deliver 24/7 operational reliability and real-time AI performance.