A Milestone in additive manufacturing: The world's largest amorphous-metal component at Automate 2019
HANAU, Germany, April 8, 2019- Heraeus Additive Manufacturing, a leading developer of special metals and the corresponding 3D printing processes, announced it would present a world record additive manufactured gear wheel made of amorphous metals at Automate 2019 in Chicago.
The gear wheel, the world's largest amorphous-metal component, was printed in a standard SLM system with material from Heraeus. With this new milestone, Heraeus is breaking through the boundaries of 3D printing and opening completely new design possibilities for a wide range of industries - from automation solutions and robotics to aviation, medical technology and the automotive industry.
The gear wheel printed by Heraeus eclipses all previous results. Produced by additive manufacturing, this compact machine part weighs two kilograms. Due to the required high cooling rates of mainly over 1000 Kelvin/second, only small parts could be produced from amorphous metals previously. Because the topology of the gear was also optimized during development, material and process experts were able to reduce the weight by 50 percent compared to conventional manufactured versions.
Heraeus has now redefined the existing limits of technology in terms of size and complexity, revolutionizing design possibilities, for example, in the automation industry as well as in robotics. Heraeus set this world record using a commercially available laser melt printer.
Amorphous metals allow completely new design possibilities and applications
In contrast to pure metals and classic alloys, amorphous metals are characterized by an irregular, non-crystalline structure. They combine properties within one material that normally are not feasible: extreme hardness and high yield strength with a high elasticity. Amorphous metals are characterized by good corrosion resistance, excellent wear resistance and the elasticity of polymers. They also have soft magnetic properties and are easy to magnetize and demagnetize. With this combination of properties, amorphous metals are superior to steel, titanium and many other materials.
Reduced weight thanks to precision manufacturing
High-precision layer-by-layer production with special materials from Heraeus also reduces material usage, saving weight and costs. Using 3D printing also reduces overall production costs. With conventional methods, making complex parts require numerous process and manufacturing steps. Several individual pieces have to be produced and then assembled into a unit. However, 3D printers accomplish this in a single process. Following assembly in the printer, moving parts are immediately ready for use and fully functional.
The world's largest printed amorphous-metal cog wheel can be seen live at the Heraeus booth at Automate in Chicago: April 8-11, 2019, McCormick Place, Booth 9619.
About Heraeus
A globally leading technology group, Heraeus (www.heraeus.com) is headquartered in Hanau, Germany. Founded in 1851, it is a family-owned portfolio company which traces its roots back to a pharmacy opened by the family in 1660. Today, Heraeus combines businesses in the environmental, energy, electronics, health, mobility and industrial applications sectors. In the 2017 financial year, Heraeus generated revenues of € 21.8 billion. With approximately 13.000 employees in 40 countries, the FORTUNE Global 500-listed company holds a leading position in its global markets. Heraeus is one of the top 10 family-owned companies in Germany. With technical expertise, a commitment to excellence, a focus on innovation and entrepreneurial leadership, we are constantly striving to improve our performance. We create high-quality solutions for our clients and strengthen their long-term competitiveness by combining unique material expertise with leadership in technology.
Featured Product
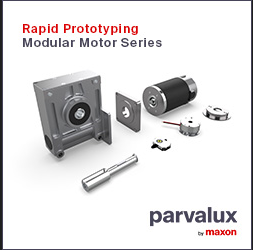
Rapid Prototyping with the Modular Motor Series
Quick to configure. Quick to build. Quick to deliver. Parvalux understands the importance of getting product in the hands of customers quickly and efficiently. The Modular Range does just that allowing customers to configure their own solution, selecting motor and gearbox, adding encoders and brakes to create a solution perfectly suited for their specific applications such as conveyor belt systems, picking systems, parcel sorting equipment, pallet shuttles and automated storage and retrieval systems (ASRS). Read our modular range guide for specifics.