3D simulation and offline programming platform FASTSUITE from CENIT offers perfect technology integration for TRUMPF laser welding systems
Support for the complete process – from importing component and fixture data to error-free download to robot controller
Stuttgart, September 6, 2018 - The FASTSUITE Edition 2 platform from CENIT provides efficient support with optimized welding strategies and methods for those who have to meet high-standard welding requirements in mechanical engineering, plant construction and steel construction. The 3D simulation and offline programming platform offers a very high degree of automation and allows the reuse of proven welding parameters in a perfect combination with interactive optimizations.
Of course, this also applies to systems such as Amada FLW 4000 M3 and other systems. FASTSUITE Edition 2 software provides the optimal support to use the system efficiently and to receive high-quality laser welding programs. The software offers all functions for the complete process - from importing component and fixture data to offline programming (OLP), simulation and optimization, and error-free download to robot controller. In addition, CENIT experts support the calibration of the virtual cell to the actual cell, so that optimum process results can be achieved immediately with the OLP system. As a rule, reteaching on the system is no longer necessary, as the exact design of the devices and components ensures ideal conditions for safe operation.
Based on CAD data, FASTSUITE Edition 2 greatly supports users in the simple creation of fixtures for prototypes, the reduction of cycle times for production parts or the reduction of programming time.
For further information, please visit
http://www.fastsuite.com/technologies/welding
http://www.fastsuite.com/products/offline-programming
Featured Product
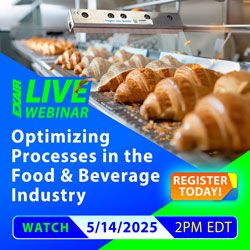