CES 16 - MarkForged Leads Explosive Growth in 3D Printing Technologies for Manufacturing
MarkForged, Inc - a company focused on industrial strength 3D printing for businesses - is announcing today a strong finish to 2015, with 400% growth in revenue year over year.
CAMBRIDGE, Mass.--(BUSINESS WIRE)--MarkForged, Inc - a company focused on industrial strength 3D printing for businesses - is announcing today a strong finish to 2015, with 400% growth in revenue year over year. Adoption of the worlds strongest 3D printed plastics continues accelerating within and across several vertical markets including: automotive; systems integration and installation; machining services; customized durable goods; industrial automation; small lot production; tooling for mass production; and aerospace and defense.
MarkForged Announces Explosive Growth for 2015
Tweet this
"Our customers are able to bring products to market faster because the Mark One prints high-strength components that endure where traditional plastics parts would just break.," said founder and CEO Greg Mark. "When we debuted this technology two years ago, our first customers were aerospace companies looking for cheaper composites, but over the last year we saw the largest growth from companies interested in high-strength, tough parts. We offer the only affordable 3D printer that prints these types of parts, and it is resonating in the market."
MarkForgeds patented technology reinforces tough nylon parts with remarkably strong carbon fiber, fiberglass, or KevlarⓇ, enabling one-day turnover and displacing parts typically machined in metal. The Mark One professional desktop printer offers a distinct competitive advantage versus traditional manufacturing techniques like CNC machining and modular fixturing, completing parts equal to or better in strength than aluminum up to 90% faster and 70% cheaper.
An Unfair Advantage
"We see a lot of users calling their Mark One their ‘secret weapon. The automotive industry is using the Mark One to create industrial strength fixtures for holding heavy parts. Machine shops that previously shunned 3D printing are adopting the Mark One as the only 3D printer able to replace or complement aluminum and steel and are beginning to ship 3D printed parts. In fact, a growing number of consumer and business products you see showcased at CES have standing behind them a Mark One printed part," said Director of Sales, Matt Katzman. "The icing on the cake for our customers is that the Mark One pays for itself in a year or less."
Come visit the MarkForged booth at CES 2016: Tech West, booth #72717.
About MarkForged
MarkForgeds mission is to bring high strength 3D printing to everyday engineering. Offering the worlds only 3D printing systems capable of automatically reinforcing engineering plastics to aluminum levels of performance and beyond, MarkForged enables every business to easily manufacture parts with structural strength right on the desktop. The Mark One Composite 3D Printer™ empowers professional users to affordably create workhorse 3D parts that solve real problems, as well as realize reinforced structures never before possible. MarkForged technologies are delivered with thoughtful, powerful software designed for collaboration, sharing, and scaling. For more information, visit https://www.MarkForged.com.
Featured Product
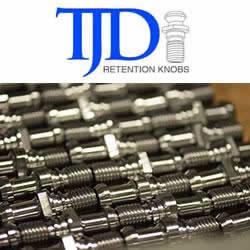