Henderson Sewing Weaves an Integrated Automation Solution with Smart, Collaborative Robots from Rethink Robotics
48-Year-Old Textile Giant Using Baxter as Part of Their Fully Automated Systems for Customers Worldwide
BOSTON, April 23, 2015 -- Henderson Sewing Machine Co. is filling the automation gap - and breathing new vigor into the textile industry - with smart, collaborative robots that pave the way for fully autonomous custom industrial sewing systems.
It's the latest production innovation for the 48-year-old Alabama distributor of industrial sewing machines, which is widely credited with consistently challenging the 'norms' in an industry battling global commodity pricing, complex products and the increasing need for skilled labor. Henderson has added two of Rethink Robotics' Baxter robots to their facility thus far, with plans to integrate the robots into its automated sewing systems. These custom systems are used by Henderson's customers for complex industrial sewing tasks, and will soon include Baxter as a bundled part of the solution.
"We build the machines that stitch together the world," said Frank Henderson, president of Henderson Sewing, and one of several family members involved with the company. "Our customers create the fabrics that make tires last tens of thousands of miles, protect astronauts in space, and make new medical devices safe and reliable. It's complex work, requiring human intelligence. Rethink's robots are letting us put our customers' people where they add the most value."
Henderson's systems routinely handle stitching, tabs, labels and webbing. But because humans are required to physically transfer essential materials at various manufacturing steps, the process couldn't be fully automated before -- something Henderson's customers would value. Now, Baxter will take on the task of loading and unloading materials for these systems, enabling an integrated automation system and freeing those employees to perform more value-added work in other areas of the plant.
"Henderson is a great example of innovation and American ingenuity," said Jim Lawton, Chief Product and Marketing Officer of Rethink Robotics. "Baxter brings the ability to automate tasks that couldn't be automated until now, allowing Henderson's customers to realize the benefits of a fully automated sewing solution - resulting in more up-time, faster turn-around, and higher margins."
For more information, please visit www.rethinkrobotics.com.
About Rethink Robotics
Rethink Robotics, Inc. helps manufacturers meet the challenges of an agile economy with an integrated workforce, combining trainable, safe and cost-effective robots with skilled labor. Its Baxter and Sawyer robots, driven by Intera, an advanced software platform, gives world-class manufacturers and distributors in automotive, plastics, consumer goods, electronics and more, a workforce multiplier that optimizes labor. With Rethink Robotics, manufacturers increase flexibility, lower costs and can invest in skilled labor—all advantages in fueling continuous innovation and sustainable competitive advantage.
Committed to accelerating robotics innovation in manufacturing and beyond, Rethink Robotics' Baxter Research Robot gives academic and corporate research environments a humanoid robot platform with integrated sensors and an open software development kit for creating custom applications.
Based in Boston, Massachusetts, the company is funded by GE Ventures, Goldman Sachs, Wellington Management, Bezos Expeditions, CRV, Highland Capital Partners, Sigma Partners, Draper Fisher Jurvetson, and Two Sigma Ventures. For more information about Rethink Robotics, please visit www.rethinkrobotics.com.
Featured Product
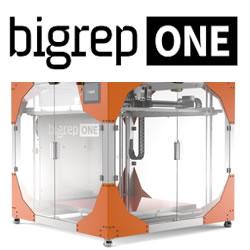
BigRep ONE: Large-Scale 3D Printing
The BigRep ONE is an award-winning, large-format 3D printer at an accessible price point. With over 350 systems installed worldwide, it's a trusted solution for prototyping and production by designers, innovators, and manufacturers alike. Featuring a massive one-cubic-meter build volume, the fast and reliable ONE brings your designs to life in full scale.