Toshiba Launches Microcontrollers for Home Appliances and Factory Automation Systems
- Enable dual control of two DC brushless motors at once -
TOKYO--Toshiba Corporation (TOKYO: 6502) today announced the launch of two microcontrollers, "TMPM470FDFG" and "TMPM475FDFG," as the latest additions to its ARM Cortex-M4F based TX04 series microcontrollers. The new devices can control two DC brushless motors simultaneously. In addition, "TMPM475FDFG" incorporates a CAN controller that supports a wide range of applications, from home appliances to factory automation systems. Sample shipments will start at the beginning of February.
Recent years have seen growing demand for lower energy consumption by motors used in home appliances and factory automation systems. Given this, improved vector control performance is required to achieve highly efficient motor control.
Based on the high-performance ARM® Cortex-M4F, "TMPM470FDFG" and "TMPM475FDFG" can operate at up to 120MHz.
Both incorporate two modules, each containing a programmable motor driver, 12-bit AD converter and vector engine. As a result, two DC brushless motors can be efficiently and simultaneously operated by one chip.
The "TMPM475FDFG" also integrates a CAN controller which is required for factory automation systems. This ensures a wide range of usability, from home appliances to industrial applications.
Applications
*Home appliances (air-conditioners, washing machines, or refrigerators)
*Inverter equipment for factory automation systems
*AC servo mechanism controls
Key Features of New Products
*ARM Cortex-M4F core. Operates at up to 120MHz.
*Interactive PWM, Minimum unit: 8.3 ns
*Two DC brushless motors operate with high efficiency and simultaneously.
*Two modules, each containing a programmable motor driver, 12-bit AD converter and vector engine, reduce load on software.
*A high-speed PWM implements 1-shunt current detection.
*Built-in 12-bit AD converter with a conversion time of 1μs.
*Built-in CAN controller(TMPM475FDFG)
Featured Product
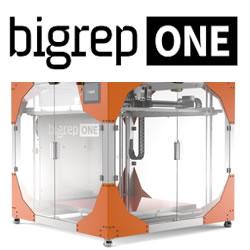
BigRep ONE: Large-Scale 3D Printing
The BigRep ONE is an award-winning, large-format 3D printer at an accessible price point. With over 350 systems installed worldwide, it's a trusted solution for prototyping and production by designers, innovators, and manufacturers alike. Featuring a massive one-cubic-meter build volume, the fast and reliable ONE brings your designs to life in full scale.