How AI is Revolutionizing Automation, but Humans Remain the Heart and Soul of Production
The Indispensable Role of Humans in Manufacturing
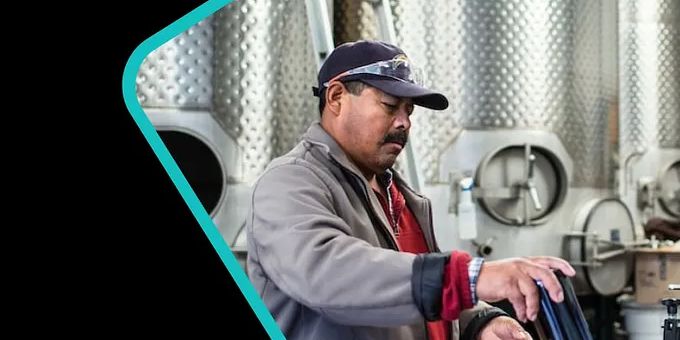
Alysia Brousseau, Marketing Manager | Pleora Technologies
Artificial Intelligence (AI) has become a game-changer in various industries, and manufacturing is no exception. The integration of AI technologies in manufacturing processes has significantly enhanced efficiency, productivity, and cost-effectiveness. Despite the advancements in automation, humans still play an indispensable role in manufacturing.
With its ability to process vast amounts of data, AI can optimize production schedules, reduce downtime, and improve overall operational efficiency. AI-powered analytics also provide valuable insights that help manufacturers make data-driven decisions for process optimization and resource allocation.
One of the challenges with AI deployment lies with resistance from employees and staff who fear job displacement due to automation. Overcoming the hesitation requires careful planning, initial communication, and effective change management, in addition to a focus on developing higher skillsets and learning higher-valued tasks.
The role of AI in manufacturing processes and decision-support
In supply chain management, AI algorithms can analyze historical data to optimize inventory levels, predict demand patterns, and improve logistics. AI-powered robots and cobots (collaborative robots) are revolutionizing assembly lines and manufacturing operations. These robots can perform repetitive and physically demanding tasks with precision and speed, freeing up human workers to focus on more complex and creative responsibilities.
Photo by Possessed Photography on Unsplash
AI also serves as a powerful decision-support tool in manufacturing. By analyzing vast amounts of data in real-time, AI algorithms can identify patterns, detect anomalies, and make recommendations for process improvements. This enables manufacturers to make more informed decisions, reduce defects, and enhance overall product quality.
The importance of human operators in automated processes
While AI and automation technologies have the potential to streamline manufacturing processes, human operators remain essential for successful implementation. Humans possess critical thinking and problem-solving skills that are difficult to replicate with AI. Human operators play a vital role in supervising and maintaining automated systems, troubleshooting issues, and using decision-making skills to ensure smooth operations. They also continue to be essential for quality control and inspection, where human intervention is still necessary for complex and subjective tasks. Humans detect subtle defects, assess product aesthetics, and make critical judgments that machines may struggle with on their own.
How humans add value beyond automation
While automation and AI technologies optimize efficiency and productivity, humans bring unique qualities that add value beyond automation. Humans possess creativity, intuition, and empathy, which are essential in problem-solving, customer service, and innovation. Innovation in manufacturing often stems from human imagination, as humans have the capacity to think outside the box and come up with novel solutions.
Additionally, humans excel in complex decision-making processes that involve ethical considerations, risk assessment, and subjective judgment. These qualities are particularly crucial in manufacturing settings where decisions can have significant impacts on product quality, safety, and compliance. Human operators can exercise discretion, adapt to unforeseen circumstances, and handle unique situations that often arise in manufacturing processes.
The future of manufacturing lies in the coexistence of humans and AI. While AI technologies continue to advance, human involvement and oversight are necessary for optimal performance and quality assurance. The collaboration between humans and AI creates a symbiotic relationship, where each complements the other’s strengths and compensates for their limitations.
Manufacturers need to embrace this synergy by fostering a culture that promotes collaboration and continuous learning. Organizations should invest in training, tools and programs to equip their workforce with the necessary skills to thrive in the new era of manufacturing. By leveraging the unique capabilities of both humans and AI, manufacturers can achieve higher levels of productivity, innovation, and customer satisfaction.
Training and shifting to higher-valued tasks
To fully harness the potential of AI technologies, manufacturers must invest in training programs that equip their workforce with the skills needed to work alongside AI systems effectively. Training should focus on areas such as digitization, data analysis, programming and workflow, and collaboration with AI-powered machines. Manufacturers should also promote a culture of continuous learning and adaptability to stay updated with the latest developments in technology. Employers can support this by providing opportunities for professional development, fostering a learning environment, and offering incentives for upskilling and reskilling.
By leveraging the capabilities of both humans and AI, manufacturers can unlock unprecedented levels of productivity, innovation, and customer satisfaction. It is through this collaboration that the true potential of manufacturing can be realized.
The content & opinions in this article are the author’s and do not necessarily represent the views of ManufacturingTomorrow
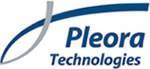
Pleora Technologies
Pleora is a leading supplier of AI, embedded, and sensor networking solutions. The company was formed in 2000 and has gained a well-earned reputation for technology leadership and innovation. Manufacturers rely on our products, standards expertise, and systems knowledge to bypass development and integration complexities in a diverse range of demanding real-time imaging application for the industrial automation, security & defense, and medical imaging markets. Visit www.pleora.com
Other Articles
Utilizing AI in the Manufacturing Space
Bringing AI to Electronics Assembly Inspection
AI for End-to-End Quality
More about Pleora Technologies
Comments (0)
This post does not have any comments. Be the first to leave a comment below.
Featured Product
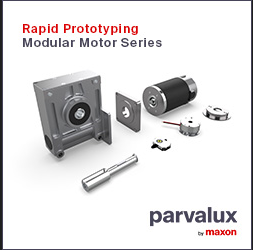