HORIZON INNOVATION RECOGNISED AS A KEY TECHNOLOGY AT FORMNEXT 2023
Following a successful Formnext show earlier this month, Horizon Microtechnologies is proud to have been chosen as a featured company in the Cool Parts Show, which in its latest film highlighted key technology innovations at the exhibition.
(29th November 2023, Karlsruhe, Germany) Following a successful Formnext show earlier this month, Horizon Microtechnologies is proud to have been chosen as a featured company in the Cool Parts Show, which in its latest film highlighted key technology innovations at the exhibition. https://youtu.be/dwDJ4OkOprw?t=290
Horizon's post-process coating technologies exploit the usefulness of a precisely made 3D microstructure (the template) for hitherto unserved areas of industry. Typically, the templates are derived from polymer micro-AM processes but parts from different machining processes and consisting of other materials can also be inserted into Horizon's coating process chain. Adding functional coatings to the template microstructure via the company's proprietary coating processes overcomes the functional limitations of the polymer material from which the micro-AM part is made. This "best of both worlds" approach is a real game changer for industry and broadens the versatility of micro-AM in an array of applications.
CEO at Horizon, Andreas Frölich says, "It is very important when the importance of our coating technologies for micro AM parts is recognised, and featuring in the Cool Parts Show is a proud moment for us at Horizon. The part that the film featured was a micro 3D printed electrical testsocket which we produced on our BMF micro AM machine. This part is very small with wall thicknesses down to 0.1 mm in places, tiny mounting holes and several hundred closely spaced vias of only 0.1 mm in diameter. Considering the part geometry alone, it would have been extremely difficult to make via micro machining, and challenging if not impossible to 3D print directly in metal. Micro molding was also not an economical option. However, the most important requirement was that the vias needed to be electrically conducting but isolated from each other. This ruled out any single-material approach to the making of this part since it would then be either entirely isolating or entirely conductive. Instead, we printed the part in a heat resistant isolating material and selectively coated the vias, the whole vias and nothing but the vias with conductive copper. It is a great example of how the versatility of micro AM when combined with our coating technologies opens up the use of 3D printing in application areas it has not been able to serve until now due to limited material functionality."
Horizon Microtechnologies' coating technology is capable of adding conformal, transparent conductive, environmentally resistant, and metallic coatings to polymer parts made by microscale additive manufacturing (micro-AM) and other three-dimensional precision- and microparts.
Adding transparent conductive and metallic coatings opens up the power of micro-AM for numerous applications such as electrodes and electrical connectors, 3D microfluidic devices, and MEMs and optics packaging. It is also possible to use the conductivity to eliminate the risk of static discharge.
Adding protective coatings to micro-AM produced parts is important because it enables the creation of microscale devices that are more durable, reliable, and better suited for use in harsh environments such as in the presence of aggressive chemicals and/or high temperatures. This can lead to improved performance and longer lifetimes for these devices, making them more suitable for use in a wide range of applications.
Frölich concludes, "Take a look at the Cool Parts Show, and see just how versatile and accurate our coating process is. Our ability to add coatings wholly or selectively to micro-AM parts is a real game changer. We can even coat difficult areas homogeneously such as long narrow channels with more than 100:1 aspect ratios, bends, branchings and also undercuts. Additionally, the ability to add copper metal coatings to a wide variety of complex-shaped 3D microparts consisting of polymer or ceramics means that for the first time, companies can produce parts with the surface functionalities of copper while also exploiting the bulk material properties, design freedom, precision, and resolution achievable through micro-AM."
www.3dmicrofabrication.com
Featured Product
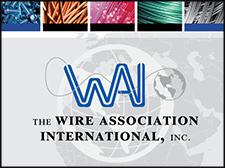