How efficient your production process is directly impacted operations and growth within your company. With the help of the right RTLS solution, your business will advance to the next level of efficiency! Let’s dive into the importance of improving process efficiencies.
Why Monitoring Utilization Improves Process Efficiencies
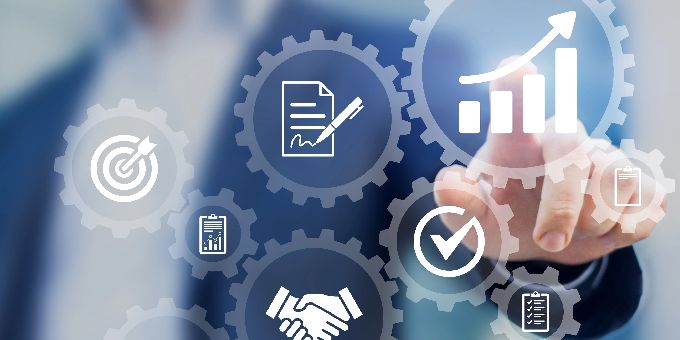
Article from | Link Labs
Monitoring assets and equipment utilization is an important step to take to improve process efficiencies. How efficient your production process is directly impacted operations and growth within your company. With the help of the right RTLS solution, your business will advance to the next level of efficiency! Let’s dive into the importance of improving process efficiencies.
What is the Importance of Improving Process Efficiencies?
Improving process efficiencies means that your company is always looking for ways to improve its offerings and day-to-day operations. An improvement mindset allows operators to see beyond the mindset of “this is how we’ve always done it” to “this is how we can improve.” Ultimately, this will give your company room for future growth and development.
Additionally, careful monitoring of process efficiencies will allow your company better to understand the sources of unanticipated improvement or deterioration. This allows you to better influence and predict the outcomes of experimental changes in the future.
How Utilization Contributes to Process Efficiencies
Utilization is concerned with how often assets and equipment experience both active use, downtime, and maintenance patterns. Your usage/downtime ratio affects process efficiencies by informing how often a piece of equipment or tool contributes to your operations. It also informs you on how much operation time isn’t being adequately capitalized on, which results in a predictable decrease in efficiency.
How an RTLS Solution Can Help Improve Utilization
Know what’s in use and what’s available at all times.
An RTLS solution can inform you what equipment is being utilized in real-time. If the required asset is available, it can be quickly retrieved rather than waiting on searches or risking the erroneous assumption that it is currently in use. If it is unavailable, a plan can be made for later use, with current efforts being reoriented to other, more readily addressed tasks.
Reallocate assets and equipment according to need.
By maintaining usage data, companies can address which assets and equipment are most needed at a given location and who typically needs them. This allows for effective reorganization for both single-site and multi-site businesses, informing where assets should be stored so they can be quickly retrieved by those who need them the most.
Eliminate unnecessary spending and waiting.
When assets are misplaced, they’re often written off as lost altogether. When assets are lost, naturally, they need to be replaced. This generates unnecessary spending when assets are not gone but simply not easily located. Further, placing orders for replacement equipment can cause a stall in day-to-day operations until the unneeded replacement arrives. Asset monitoring can help prevent this unnecessary spending and wait time.
Predict and prepare for necessary growth and spending.
Historical data on usage begets predictive data on usage. With RTLS asset tracking, companies can prepare for the growth and spending that comes with the improvement they’re working toward, smoothing the transition into the next stage of their business endeavors.
Work in Process Tracking
We have explained the importance of monitoring utilization and why monitoring utilization improves process efficiencies. Now, let’s look at what “work in process” tracking is and how it plays a significant role in improving process efficiencies. WIP refers to inventory that has entered the manufacturing process but is not yet finished. We know that juggling all the moving pieces can pose challenges, such as maintaining the right balance of inventory, identifying sources of inventory loss or damage, and forecasting product completion.
Our AirFinder OnSite is used as a WIP tracking system by attaching a puck tag to each set of parts as they make their way through the manufacturing plant. Splitting a facility into several zones allows plant managers to request detailed reports. These reports range from location to length of time in each zone.
With AirFinder OnSite, your company will be provided with many benefits that will ultimately lead to the overall improvement of your company's process efficiency. Here are a few benefits that come with WIP tracking through Link Labs:
- Cutting down time spent on reporting
- Identifying bottlenecks and choke points in WIP systems
- Gathering fresh data on production cycles and schedules
- Preventing unplanned downtime
Take Advantage of Asset Tracking Today
Link Labs’ AirFinder is a real-time asset tracking system provider that allows companies to track WIP and tools to improve process efficiencies. For more information on how our solution can bring you value, book a demo today.
The content & opinions in this article are the author’s and do not necessarily represent the views of ManufacturingTomorrow
Comments (0)
This post does not have any comments. Be the first to leave a comment below.
Featured Product
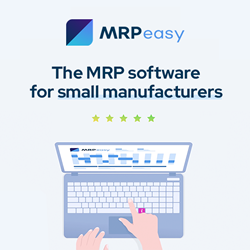