More cost-effective than a milled part - The "door opener" for 3D printing in automotive series production.
The advantages of additive manufacturing (AM) best come in play when components are designed from the ground up specifically for this process. This fact is well-known. But how this aspect, combined with other optimization measures, can positively influence both the technical properties and the costs of the finished component, may come as a surprise to even some experts.
Now, Fraunhofer IAPT has carried out a redesign project using the example of a sports car door hinge to identify, step by step, the factors that influence the component's cost.
Aided by a special software tool which in the meantime is commercially available at 3D Spark (a successful spin-off of Fraunhofer IAPT), the Fraunhofer engineers first identified a suitable component.
At a very early stage of the design, the experts then determined the cost-optimal orientation of the component in the 3D printing process. Using the optimized orientation, it was possible, for example, to minimize the number of support structures required while maximizing the number of components that could fit on a build platform. The thus identified component orientation leads to cost savings of 15 percent compared to an additive manufacturing process without such optimization.
In the next step, the structure of the hinge arm was optimized in a targeted manner, using one of the benefits of additive manufacturing in that it enables completely new component geometries. This gave the component a basic shape that only contained material where the simulated force flow required it. In total, this reduced the weight of the door hinge arm by 35%. And because of the reduced material requirements and the shorter print time, the costs compared to 3D printing without structural optimization dropped by another 20%.
Any support structure that does not have to be removed saves time and thus avoids part of the significant costs incurred in the highly manual post-processing phase. Reducing the number of support structures in the design also has a positive effect on production time and material requirements, which cuts costs again by 10%. Skilful selection of the optimum metal powder material from the increasingly broad portfolio of 3D printable materials makes it possible to lower costs by another 10%.
Adjusting the AM process parameters provides additional ways to reduce costs. For example, higher layer thickness during printing, optimization of process parameters, and deformation of the laser beam profile significantly reduce build time. Even though this results in a slight loss of parts quality, (though still superior to that of cast parts), it enables printing costs to be reduced by a further 15%. Optimizing machine utilization by nesting and, if necessary, stacking in the build area, leads to further cost savings of 10%.
Summary of the results of the IAPT study: designing with additive manufacturing in mind and following a »Design to cost" approach throughout allowed the hinge arm to be manufactured at 80% less cost than a 3D printed part without the same optimizations. This overall percentage can be broken down as follows: Orientation and topology optimization as well as support optimization contribute 45%. Optimized material selection, speed parameters and workload maximization in the AM process reduce costs by a further 35%.
Fraunhofer IAPT was able to show that a cost reduction of additive manufacturing by a factor of five is feasible. In parallel, brought an increase in the technical performance of the vehicle through lower weight and improved optics. The most important point, however, is that this enabled the cost of manufacturing a small series of hinge arms for a sports car door to be reduced by 50% compared to conventional milling. Additive manufacturing is therefore not only superior to milling in terms of technical performance, but also significantly more cost-effective.
The results of this study on the systematic cost reduction of AM components can be applied to a wide range of automotive components. They demonstrate that additive manufacturing can already be used profitably in larger series of up to 5000 units.
Featured Product
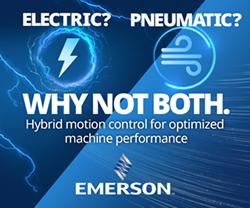
Elevate your manufacturing processes with data-driven insights
Join Emerson at Hannover Messe 2025, Hall 11, Booth C30 and discover how embracing a Floor to Cloud™ strategy can revolutionize your operations. This strategy integrates on-site devices and technologies with cloud analytics, providing the insights needed to enhance manufacturing efficiency, maximize workforce potential, and achieve sustainability targets. Our team of experts have a commitment to innovation and look forward to discussing your challenges to develop a customized solution. Claim your Free Ticket.