With each new IIoT device brought to market, manufacturers spent untold amounts of time and money making it live up to its potential. Time and again, they were building and rebuilding the same technology to enable data-based decision making, miles away from the device itself
What is “Platform as a Service” and How Does it Improve Efficiencies in IIoT Ecosystems?
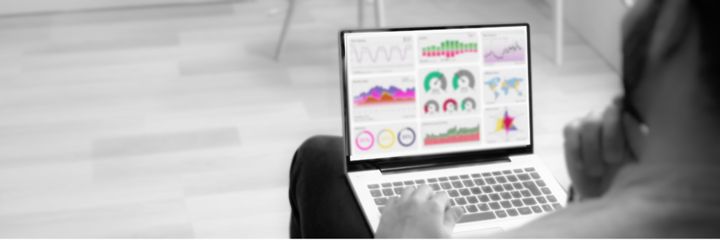
Richard Reisbick, Chief Technology Officer | FreeWave
What I’m about to tell you will change a year from now — and even by the time you read this: As I write, there are about 17.08 billion connected IoT devices worldwide.
That figure mushrooms daily. In fact, by 2030, the number of active IoT devices is expected to double. Put another way, according to IDC data, 152,200 IoT devices will connect every minute by 2025. Why am I mentioning these fun facts?
Remote asset monitoring is the most popular use case for IoT. Yes, the MOST popular.
At industrial production sites the world over, IIoT sensors (short for Industrial Internet of Things sensors, as IoT devices are referred to in such applications) continually measure pressure, temperature, water level, wind speed, air quality, ambient conditions, safety parameters — the list goes on.
I’ve worked with IIoT technology in various capacities since its infancy, so it’s impossible for me to see the proliferation of IIoT sensors and not envision the enormous potential the data offers to different decision-making levels, from engineers in the field, to regional managers, to top leadership.
But in recent years, as the IIoT sensors market expanded, the promise of efficiency was tempered by something else I couldn’t help but notice.
Wasted effort. And lots of it.
With each new IIoT device brought to market, manufacturers spent untold amounts of time and money making it live up to its potential. Time and again, they were building and rebuilding the same technology to enable data-based decision making, miles away from the device itself.
Essentially, IIoT manufacturers kept reinventing the wheel.
That is, until my colleagues and I saw the way to a solution.
Platform as a Service Comes to the Rescue
I live in Colorado, and while I’m not far from the woodsy mountains, I can honestly say I’ve spent zero time pondering the age-old question: If a tree falls in the forest, and there’s no one there to hear it, does it make a sound?
And yet I ask you to consider this: If an IIoT device on an offshore oil rig (or some other remote location) senses something amiss, and there’s no one onsite, does anybody hear?
For all practical purposes, the answer is no. The device itself is just a piece of hardware. It can emit a signal of sorts, but in order to be understood and acted upon by humans, the signal must not only be transferred but also translated into intelligible data. And just because a transmission is intelligible doesn’t make it meaningful. For that, the data must undergo software analysis on its way to a user interface, or point of human interaction. What starts out as zeros and ones becomes knowledge along the way.
Onscreen, the user sees an interactive IIoT dashboard, which graphically represents — or “visualizes” — data so as to provide at-a-glance, actionable insights regarding remote operations. So, when a sensor detects a pressure spike or something else awry, the aberrant measurement doesn’t fall on deaf ears but takes the form of an alert, which is “heard” and heeded at the end of the data chain.
At the start of the data chain — commonly called the edge — is your sensor. On the other end is the user interface. In between is a middle layer of sorts, which connects sensors to software and, ultimately, humans. This middle layer is called a platform, and every sensor needs one. The platform allows for the flow of information from end to end and also contains the tools needed for analysis. It gets the data where it needs to be, in a format that’s useful to the person receiving it.
So, for every IIoT device developed, manufacturers also built out a platform. Over time, a pattern emerged: Regardless of the manufacturer or specific type of device, the resulting platforms were mostly all the same. These platforms shared so many basic functions and requirements that their makeup was roughly 70 percent identical.
The remaining 30 percent of platform design varies by use case and other factors. Take, for example, a fictitious tech company called Joe’s Tree Growth Sensors (a nod to both my passions: Colorado and technology!). Several of Joe’s sensors monitor the growth of trees intended to provide shade in a public park. Elsewhere, Joe’s sensors monitor the growth of trees on a pine plantation. Sitting at his computer in the comfort of his office, the park manager wants to see his tree-growth data presented in a certain way, with emphasis on crown measurement. The sales manager of the plantation, however, needs to see alerts when the trees are ready to harvest. And across the hall from the sales manager, the plantation’s Director of Tree Health needs to see indicators that trees have a growth-stunting nutrient deficiency.
Still, the thought that every device represents a specific and representative platform gave me pause. That is a lot of dashboards, proprietary links, and so on. Data overload.
Clearly, it would be more cost-effective to invest resources on customizable parts unique to each application and end user while outsourcing the development of the platform’s all-purpose — or “generic” — design elements. And Joe can accomplish this feat by leveraging Platform as a Service (PaaS) as opposed to building a platform from scratch for each newly invented IIoT device. Joe’s tree-loving customers win big, too, because the platform, with its customizable dashboard, delivers data they predefine as relevant.
Introducing the First Customizable Data Platform for Industrial Operators
While Joe is imaginary, IIoT manufacturers and remote operators are already seeing real results with the very real and available FreeWave® Insights™ cloud-based data platform, which comes complete with user-friendly tools for dashboard creation and customization. (The words dashboard and platform are sometimes used interchangeably, but we consider the dashboard as the user interface within the IIoT platform.) The dashboard is both a control panel and a visual representation of key data your IIoT devices and sensors collect.
A well-designed dashboard conveys information hierarchically through charts and other data visualizations, empowering users to extract actionable insights, receive alerts, identify patterns and trends, and make projections.
The platform is the dashboard’s pre-built foundation.
FreeWave works with organizations of all sizes, from SMBs to Fortune 500 companies. Unlike the aforementioned city park, each of these companies might have hundreds of IIoT sensors, from various and sundry manufacturers, operating across several worksites. One advantage of FreeWave’s PaaS solution is that all of these devices are integrable with our platform.
FreeWave has been in the business of connecting devices for more than 30 years. Our Insights data platform is the newest link, readily connecting to our Fusion™ platform of radios, which provide IIoT device connectivity and data encryption as part of our zero-trust cybersecurity framework, as well as fast, reliable, uninterrupted satellite connectivity on land and sea.
Reinventing the wheel stops with the FreeWave Insights platform.
Learn how a scalable, customized, cloud-based data platform can help your industrial operations team analyze and act for true business transformation.

Richard Reisbick is Chief Technology Officer for FreeWave, provider of industrial wireless and IIoT solutions creating a frictionless path from operational data to extraordinary decision-making for business transformation. As an inventor, he has prioritized the user experience and engineering architecture of hardware and firmware for more than 20 products utilizing MCU, DSP, and FPGA technologies.
The content & opinions in this article are the author’s and do not necessarily represent the views of ManufacturingTomorrow
Comments (0)
This post does not have any comments. Be the first to leave a comment below.
Featured Product
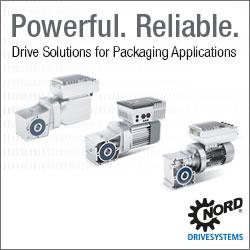