Every industry we serve—from high-performance computing and consumer devices to automotive, electrification and connected healthcare—is impacted greatly by user experience
State of Reliability and Hardware Design
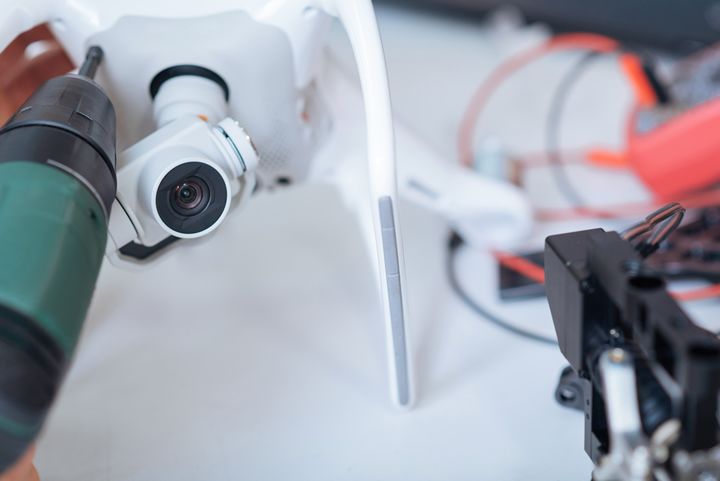
Q&A with Scott Whicker, SVP and President, Transportation Innovative Solutions | Molex
What did Molex’s recent survey on the State of Reliability and Hardware Design reveal as the biggest challenges facing system architects and design engineers in balancing expectations for reliability with other variables, such as growing product complexity, shrinking design cycles and manufacturing costs?
Design engineers and system architects face unrelenting challenges every day, which start and end with meeting or exceeding customer expectations for product quality and reliability within pre-defined cost targets. As a result, they need to align specifications for the highest levels of performance while making necessary tradeoffs based on a product’s intended use and ultimate lifecycle. In Molex’s transportation sector, which I lead, engineers must address stringent requirements to ensure products are reliable and rugged while addressing demands for increasingly smaller components. All of this adds greater product complexity while further straining packaging and manufacturing costs.
In Molex’s recent Reliability and Hardware Design Survey,, more than 750 system architects and design engineers cited cost (50%) and manufacturability (46%) over product reliability when making product design tradeoffs. Let’s face it, not every product is designed and manufactured to last forever, which is why it’s essential to understand projected product lifecycles before finalizing all the design attributes. Equally important is fully grasping intended use cases and applications as they will have enormous impacts on how products perform in real-world scenarios.
A great example of this relates to our connected mobility solutions, where Molex engineers are transforming vehicular antenna technology for 5G communications on the road with a focus on vehicle-to-everything (V2X) applications. We rely on various digital tools, modeling and simulations, including solutions from Keysight, an innovator in software-centric design, emulation and test solutions, to develop virtual vehicular antenna design environments in different configurations and conditions—before moving forward with prototypes. The ability to use predictive analysis and simulation not only saves significant costs and time, but ultimately empowers our design engineers to anticipate evolving product demands, so they can develop better-performing, next-generation antenna solutions.
According to the survey, more than a third of the respondents prioritize user experience over product reliability. How do you see user experience driving important product design tradeoffs when it comes to reliability?
More than one-third of those polled for the reliability survey prioritized user experience, even at the expense of a product’s reliability. Every industry we serve—from high-performance computing and consumer devices to automotive, electrification and connected healthcare—is impacted greatly by user experience. Across the transportation sector, I see daily examples of how adjacent industries are heavily influencing cars of the future, such as consumer electronics and data centers, as well as crucial technology enablers, including battery management, networking, data storage, semiconductors, and software.
Consumers are demanding ever-increasing levels of personalization in the products they choose, which puts pressure on our customers to include opportunities for customization into their overall product designs. Anticipating and designing products that align with evolving user preferences for fast, straightforward and intuitive operation necessitates close and regular customer communications to keep pace with changing end-user preferences.
At Molex, we believe in real-time customer collaboration, which is why we embarked on a multi-year digital transformation, including the adoption of data-driven solutions, digital catalogs and automated processes to unite Molex engineers with counterparts on the customer side. The goal is to make it easier for engineers to do what they do best — respond to emerging customer requirements with speed and agility. By enhancing our engineers’ digital experiences, we improve product design efficiencies while providing longer-lasting, mutual value for our customers.
Equally important is giving product designers freedom to use digital tools and technologies that streamline overall product development efforts.
Power consumption is on the rise as users demand faster, more feature-rich and more capable systems and devices. In fact, 25% of those polled placed power consumption near the top of their priority list. How can engineers design for “higher power” without compromising reliability?
Across the markets and industries Molex serves, power management has been an overarching product design consideration for decades. While power systems are becoming smaller, lighter and more efficient, they continue to pose significant product design challenges, especially when developing highly durable and capable power interfaces and distribution systems for specific applications and environments.
With power consumption on the rise, concerns about the impact on product reliability continue to escalate. According to a quarter of those polled in the reliability survey, power consumption placed near the top of their list of priorities. When it comes to power, heat is one of the greatest threats to reliability, which is why we are building upon decades of experience in thermal management to address increasing product design considerations. Additionally, our engineers are exploring how best to leverage special design characteristics, including increased use of large contact surfaces as well as low contact resistance to reduce heat generation.
Molex’s vast selection of power-delivery and distribution products in wire-to-wire, wire-to-board and board-to-board configurations are enabling performance breakthroughs for next-gen automotive, consumer electronics, medtech, industrial, data center and telecom applications. Ongoing investment in and expansion of our existing portfolio of reliable, durable and efficient power solutions ranges from very small, low-power micro-miniature systems to extremely large power distribution systems, delivering 500 amps of power—and everything in between. When it comes to power consumption, advancements in design engineering, materials science, testing and collaboration with power-industry players will prove invaluable in designing products for higher power without having to make major reliability compromises.
Nearly half of the survey participants listed AI, ML, simulations and data analytics as the best overall solutions for improving product reliability. Which use cases emerging from the rise in AI and data-based tools have the greatest potential to improve reliability?
Interestingly, only 33% of the survey respondents currently use data-based models to help evaluate design tradeoffs but 46% identified AI, ML, simulations and data analytics as being the best solutions for improving reliability. Of those surveyed, 83% expressed optimism in AI’s potential to improve the reliability of future electronics products, which echoes our positive sentiments in the emerging role of AI and data-driven solutions to transform product design experiences.
From our perspective, these emerging digital tools and technologies will help system architects, product design engineers—along with their customer counterparts—gain new levels of confidence in their designs because they will be able to simulate operation in nearly any environment and receive immediate feedback. For instance, Molex automotive engineers work directly with customers to simulate a vehicle’s operation and receive immediate validation on the impact of different factors on performance, including structural integrity, weight, package size optimization, current rating, thermal management, signal integrity, electromagnetic compatibility/electromagnetic interference (EMC/EMI), high-voltage considerations, the list goes on and on.
At our global reliability labs, we test an entire range of variables and capabilities to optimize product designs, eliminate rework and avoid excess costs through the use of sophisticated test equipment and accelerated failure models. Simulations and modeling help facilitate early troubleshooting while in-house anechoic chambers address the impact of unwanted electromagnetic energy on all types of electronic devices. Testing and analysis for signal integrity (SI) issues also helps identify potential reliability problems well before designs turn into working prototypes. Moreover, customers are part of the testing process, which ensures seamless collaboration while expediting the delivery of final, optimized designs.
Increasingly, modeling and simulations are getting very granular, enabling system architects to examine everything from the critical parts of the connector interface to how the connector comes together. Understanding the physics at subsystem levels through advanced simulations offers system architects much deeper insights into potential performance issues than previously possible.
Incorporating AI is an iterative process that requires testing and correlation to deliver maximum benefits. We are eager to harness the advantages, which is why we are so bullish about the impact of AI, simulations, and modeling to transform future generations of connectivity solutions.
While reliability impacts all industries, the automotive and transportation sector relies heavily on predictive engineering and digital twins to predetermine product performance in real-world environments. What can other industries learn from this vital industry segment to boost reliability while better managing cost and manufacturability?
In automotive, designing products to withstand the rigors of the road creates a daunting list of challenges. That’s why 71% of engineers from this sector ranked test engineering as the area they relied on most to ensure product reliability. At Molex, test engineering is enhanced using predictive engineering and digital twins, which enable us to virtually validate connectivity solutions while offering our automotive OEMs and Tier One suppliers valuable information that saves both time and money.
Molex embraces digital twins to improve vehicle designs by identifying and fixing problems much earlier in the design process—and well before any prototypes have been produced. One of the best parts of working with digital twins is the ability to share and collaborate on 3D models simultaneously using a single, constantly updated source of information.
There are so many obvious benefits of performing design iterations virtually instead of physically but perhaps the most transformative aspect of digital twins is the ability to build a more robust solution before you even get into the lab testing environment. In this latest survey, system architects prioritized test engineering, but in the future, digital twins and predictive engineering will have the biggest overall impacts. The opportunity to continually push technology envelopes will extend well beyond the automotive sector to address every industry Molex serves.
Using a product digital twin, engineers can work with customers to adjust and validate product specifications while using valuable data insights to improve next-gen products. As we look ahead, it’s clear that we have so much to learn from other business divisions and industries served by Molex, which is why we are leveraging automotive’s learnings from using digital twins and predictive engineering in designing and building connectivity solutions requiring ever-faster speeds in shrinking form factors.
Together, we expect to embrace all the digital tools at our disposal to shorten product development times while increasing performance of all types of connectors by enhancing capabilities across mechanical, sealing, thermal and electrical functions.
Suppliers play an increasingly critical role in ensuring reliability, which is why 96% of respondents have changed part suppliers due to reliability issues. What should suppliers do to keep pace with their customers’ growing demands, and what advice can Molex share on how best to address this challenge?
Our business philosophy is anchored by an unwavering focus on creating and sustaining mutual value for Molex and our customers—as well as our suppliers. We realize that it’s critical to pick the right suppliers with the right materials. It’s also essential to select suppliers with complementary cultures to enable continuous collaboration and process improvement. Fortunately, we have fostered excellent supplier relationships and openly share knowledge and data in support of our customers’ stringent requirements.
To keep pace with growing customer demands, we work with suppliers to validate product lifecycles and maintain a steady flow of innovative ideas related to improvements in materials and processes. Equally important is teaming to reduce supply chain and manufacturing roadblocks in order to deliver final products on time and on budget. All of our suppliers understand Molex’s commitment to product quality and reliability, and they work alongside our teams to apply lessons learned and employ best practices.
The best advice I can offer is to nurture trusted supplier relationships and recognize the vital role they play in your continuing success, especially when faced with constantly shrinking design cycles. In the world of connectivity solutions and electronics manufacturing, it takes a village to advance the latest technologies while anticipating evolving customer requirements as well as emerging application areas.
The content & opinions in this article are the author’s and do not necessarily represent the views of ManufacturingTomorrow
Comments (0)
This post does not have any comments. Be the first to leave a comment below.
Featured Product
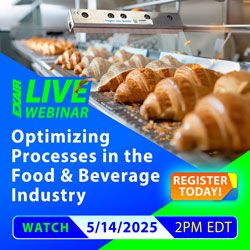