For a global manufacturing company specializing in industrial equipment for natural resource processing, unpredictability in their supply chain led to an immediate need for an agile system.
How a Global Manufacturer Automated Their Supplier Management Process in Days
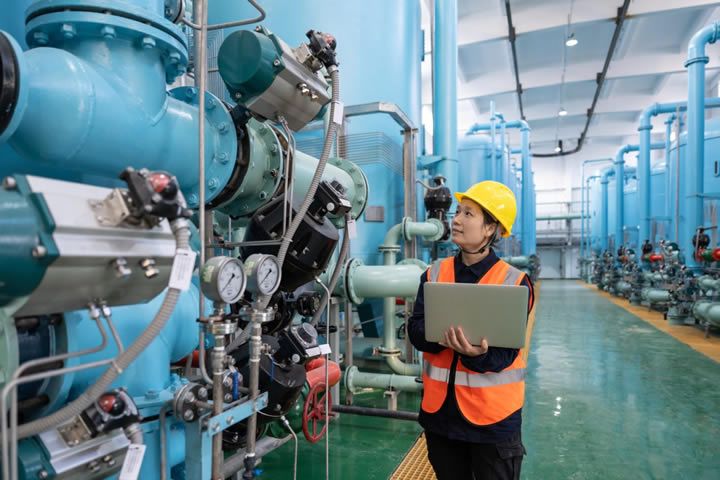
Case Study from Ray Waldron | quickbase
Streamlining supplier management processes benefits all companies. Unfortunately, taking steps to proactively solve supply chain challenges often get ignored until they threaten the health of your business.
For a global manufacturing company specializing in industrial equipment for natural resource processing, unpredictability in their supply chain led to an immediate need for an agile system. Faced with a lack of visibility into supplier and inventory data and a disjointed, complex order tracking process presented major challenges. However, their ability to adopt a suite of Quickbase supplier management applications enabled them to create efficiency and clarity in their supply chain in a matter of days.
Facing Challenges
Like many companies that handle complex orders, this manufacturer struggled to coordinate its order management processes with its engineering, purchasing, and planning processes. Order managers had to dig deep into the data for order history and status of open issues. Email was the primary tool used to assign order tasks as well as communicate between departments meaning assignments were easily missed and problems became difficult to track. These slow, manual ways of getting work done is known as “Gray Work,” which can
Contributing to their difficulties, information for their engineering and manufacturing processes were stored across multiple order management, planning, engineering, manufacturing process platforms, and an ERP. These disconnected systems presented a major hurdle when they were confronted with a shifting workforce and widespread product unavailability.
Finding a Solution
The manufacturer needed to streamline operations, and were battling against the clock. With the volatility of suppliers at that time, the manufacturer could not wait months to develop an application to unify systems and surface critical data.
In response, they built a suite of applications with Quickbase’s Dynamic Work Management Platform focused on streamlining the order management process. The custom applications offered flexibility and transparency by providing all team members easy access to critical information. The business was able to leverage experts in each line of business to build flexible solutions addressing their unique pain points.
Speedy implementation of custom-made applications was essential as supply chain efficiency became more important than ever. To deal with crises in a global environment, the company needed complex, tailor-made applications that could be developed in hours. They were able to achieve this with Quickbase.
What They Built
A new solution doesn’t always mean throwing away previous systems, especially when time is critical. To avoid disrupting the order intake process, new orders continued to be collected and stored in their ERP system, which contained large amounts of existing historical data. All order management, manufacturing process, and supplier data are exported automatically from their individual systems into a cohesive Quickbase application. This application gave order managers quick insight into order status ensuring on-time deliveries.
Inside the workflow, order managers can review each order and ensure that all the necessary engineering, purchasing, and manufacturing activities will be completed in time to match. If an order manager spots an issue, they can assign activities within the application to resolve it.
“With Quickbase, everything is out in the open, so it’s clear who is doing what, how much work is being done, and when it will be completed.” – Vice President, Global Operations Engineering and Order Management
Quickbase gave this manufacturer what they needed to begin building out customer reports and workflows rapidly. Their reports allowed order managers, their managers, and others to quickly drill down into orders to find any information they need to keep the process moving forward. It also surfaced areas of improvement and provided granular detail of process breakdowns in real-time, allowing for quick responses when problems would arise.
The Quickbase Solution
Quickbase’s Dynamic Work Management platform capabilities allow for users to adopt the unique solution they need quickly. Features like Connections and Insights allow businesses to serve different focus areas and build a connected suite of solutions. For this manufacturer, a single source for all crucial information and transparent, customizable dashboards were primary requirements.
Connections enables you to build an application which taps into your existing ecosystem with secure integration and automation capabilities. For our manufacturing client, Connections allowed for them to pull vendor data out of ERPs and legacy systems and into a singular location. In doing so, a holistic solution was assembled from existing data and the process was readily streamlined.
Insights helped them create customizable dashboards providing transparency into supplier performance, capacity, and more. This enabled them to receive real-time updates from suppliers and take mitigating actions or notify stakeholders when an order has been delayed. This level of speedy insight allowed them to pivot easily in the face of disruption.
Proactively Addressing the Future
Since implementing Quickbase, other opportunities to solve challenges became evident across the business. This led to improvements in factory-to-factory communications, inventory control, and engineering efficiency, all of which continue to be developed and improved upon. The team now has access to integrated manufacturing and engineering data in a single view, and are creating a culture of continuous improvement. The rapid development and implementation of Quickbase applications granted the manufacturer advantages in time savings, seamless supply chain management, and realignment of employee focus to better serve customers.
Quickbase’s agility platform uniquely enables manufacturers to make the most of the systems and data they already have rapidly. In a matter of days, an international manufacturing leader stood up a suite of applications to gain visibility into their supply chain, manufacturing status, and high priority orders.
The content & opinions in this article are the author’s and do not necessarily represent the views of ManufacturingTomorrow
Comments (0)
This post does not have any comments. Be the first to leave a comment below.
Featured Product
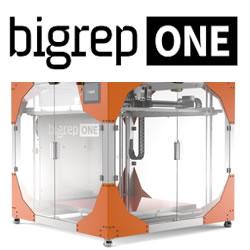