Diamond Precision Engineering was tasked with making a giant guitar to mark the 80th birthday of Sir Paul McCartney.
Companies Collaborate to Build Giant Guitar Installation in Liverpool
Case Study from | Lantek
The installation at the entrance to the Beatles Story Museum at Albert Docks Liverpool is 4m long and is made from 6mm thick steel sheet, laser cut at Diamond Precision’s Birkenhead factory where the company uses Lantek Expert to nest and programme its two Mazak fibre lasers, an OPTIPLEX 4020 and an OPTIPLEX NEXUS 3015 and prepare quotations for its customers. The company branched out into laser cutting in 2014, complementing its 30 years of CNC machining and general engineering.
Oliver Pitt, Director Laser Division says, “With Lantek Expert we can import CAD data, nest parts in full sheets and remnants, generating the fibre laser cut path in a matter of seconds. On the laser cutting side of the business the company makes parts for many applications such as the railway industry, commercial vehicles and bespoke signs.
Simon Armstrong of Liverpool based Design Laser Play was commissioned to design the guitar to fit in with the budget for the project and a tight timescale for unveiling, “The guitar is a replica of the Hofner bass guitar that Paul McCartney plays, and the aim was to mark his 80th birthday and raise money for the Nordoff and Robbins charity which provides access to music therapy. The location for the guitar is quite narrow, so this guided the design. We have worked with Diamond Precision Engineering on a previous project called Winds of Change which was a 6.5m tall working windmill, located in William Brown Street, Liverpool. As the collaboration went well, Diamond Precision was a natural choice for the guitar project.”
Design considerations revolved around fitting the installation into a restricted site, right next to the entrance to the museum while maintaining safety for the public and meeting the cost and timescale limitations. Albert Docks where the museum is located is a popular venue in Liverpool and is busy all the time. Simon Armstrong says, “Firstly we wanted to discourage people from climbing on the structure so minimised foot and hand holds in the design. This cannot be entirely prevented, so it also had to be strong and stable enough to take the weight of anyone that does climb on it. Similarly, it had to have no sharp edges.” After discussions between Simon and Oliver, the thickness of the material was increased to 6mm and all edges were rolled. Most of the weight is in the base supporting the guitar and it is also bolted to the ground to ensure stability.
To keep costs down, rather than a full guitar, the installation consists of front and back guitar shaped panels connected together with an internal channel section along the full length and crosswise spars to maintain rigidity. The body and stock sections of the guitar were made in separate pieces to fit in a sheet of material for laser cutting and also fit into hot dip galvanizing tanks. After galvanizing, the whole structure is powder coated and finally vinyl wrapped with the graphic design. The vinyl wrapping could not be done on site due to windy conditions at Albert Dock, so was carried out in Diamond Precision’s factory.
Initially the design did not include the Vox amplifier, but this was added to minimise the danger of climbing and add stability and weight to the base of the structure, filling the long narrow site as much as possible. Simon Armstrong adds, “The front and back skin design for the guitar works well as you can only view the installation from directly in front or from behind, so it appears solid. This simplified manufacture, reduced cost and also made it easier to arrange a strong and reliable connection between the guitar and the amplifier/base assembly.”
To calculate the cost of the guitar project Diamond Precision used its Lantek Integra Quotes and CRM system. This keeps track of around 500 different customers for the company so that it can see the history of quotes created for each customer as well as details of previous jobs completed for them. It connects to the Lantek Nesting module in Lantek Expert so when generating a quotation, it knows how much material will be used and also how long the laser cutting will take. As part of the quotation, the system also includes other operations such as welding, painting and bending as well as subcontracted operations, recording a breakdown of the times for each element of manufacture, greatly speeding up and simplifying the whole process.
Oliver Pitt says, “We have a management system which works well for our machining and general engineering business but, we discovered that it was not suitable for fast moving laser cutting jobs, so we spoke to Lantek to find a solution.” Diamond Precision has five people generating quotes for laser cut parts and needs to produce around 400 quotes every month. Speed and accuracy are of utmost importance as there is a correlation between these factors and the chances of getting the job. He continues, “Moving over to Lantek Integra Quotes has made a dramatic time saving. Previously, we were continually double handling data, wasting effort and increasing the chance of human error. Having detailed times for each element of a job is a big improvement. Previously we could only have the total job time. Now, we can start with a CAD file and quote with detailed timings for each operation, automatically applying the margins allocated for each customer. For repeat work, the savings are even greater as all the process information we need is already in the system.”
Material allocation lets the company mix nested parts from different customers in one sheet or, for bigger parts, one or two items per sheet. The Lantek software records remnant material from previous jobs, so these can be reused in later production nests to minimise waste. Full sheets are catalogued by a sticker system for material grades and thicknesses, as are the remnants. With this information in the system. Diamond Precision has complete ISO traceability for the manufacturing process, a factor which is becoming increasingly important for customers.
Oliver Pitt says, “We worked closely with Lantek when installing the system and in customising it to our needs. One of the enhancements is an automatically generated packing list of parts for the customer. This comes with a matching tick list for the customer so that he can check and confirm that everything has been delivered. We are now looking at expanding our Lantek Integra system for fast invoicing and analysis of manufacturing performance. Lantek software has generated some dramatic improvements for us.”
Working in partnership with Design Laser Play has raised Diamond Precision’s profile in Liverpool. Oliver Pitt says, “We are very proud to be involved in some of the amazing art installations that are springing up around the city. We have built up a network of companies we regularly work with and Lantek is an important member of that network.”
The content & opinions in this article are the author’s and do not necessarily represent the views of ManufacturingTomorrow
Comments (0)
This post does not have any comments. Be the first to leave a comment below.
Featured Product
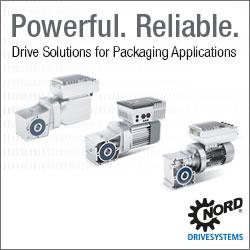