Machine data now serves as the conversation starter on the floor to uncover issues and identify solutions. The third and final phase for AMT will be an upgrade to the gold licensing level of DataXchange and a roll out to all machines.
Smart Manufacturing Takes Flight
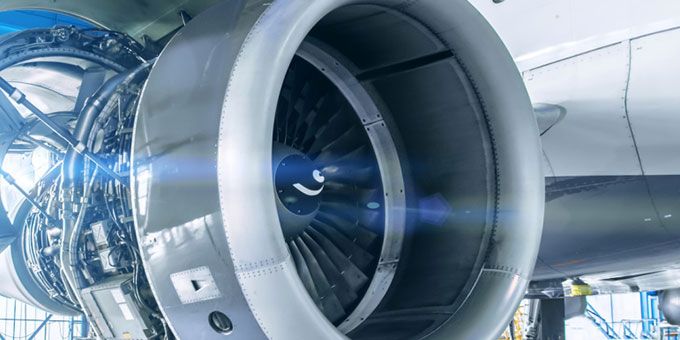
Case Study from | Shop Floor Automations
The indicators to diversify your customer base can present themselves in many ways to a company. For Senior Aerospace AMT, a leading manufacturer of commercial and aerospace parts, it started with one major indicator. A single customer of the company – albeit, one of the largest aerospace companies in the world – made up approximately 90 percent of AMT’s business. The company spun this sign into an opportunity to fine-tune its machining operations.
Tom Anderson, AMT Machine Process Engineer, explained, “We wanted to know, how much time are machines broken down? Which machines need to be replaced over others, and when? At the same time, we wanted to get a full sense of our capacity.” Once this visibility was gained, he figured, there would be a better chance to determine potential improvements to cost effectiveness and quality in an effort to retain current business and attract new prospects.
AMT partnered with Shop Floor Automations (SFA), a California-based provider of hardware, software and technical expertise, for options. The DataXchange machine monitoring solution, by Scytec Consulting, was recommended after an evaluation of AMT’s requirements. “We wanted to walk before we run,” he noted, sparking a pilot approach to the implementation of the software. Six machines, some with tablets or bar code scanners, were connected by the IT team at AMT during the first phase of the pilot.
“It was really easy, out-of-the-box,” he says. The tools and documentation available through the platform were enough for Anderson and his team to start setting up the program in-house. “You can collect infinite types of data, so we looked to simplify above all else.” For example, machine statuses were set up to indicate the lack of an operator.
Initially the team input 15-20 downtime options to select from; those options were then narrowed to 8-9 with a reason code and the ability to add a note for further information.
ESTIMATING WITH PRECISION
At the same time, the team decided to leverage the existing PCs at each work center so there wasn’t a need to train operators on new hardware in addition to the DataXchange software.
Then the production slowdown of Boeing 737 Max planes in 2019 hit the business. A year later came the onset of the COVID-19 pandemic. AMT went from 500 employees to 110. Supply chain disruptions rippled throughout the company, with machines out of service for six months awaiting electronic components. Still, AMT plodded on with the DataXchange implementation. Its second phase of the pilot expanded the machine monitoring solution to machines with PC displays. With long machine runtimes of 10-14 hours, operators can leave a building and receive a notification from his or her phone in the event of a machine interruption.
“Before we installed DataXchange,” says Anderson, “Thirty minutes or so could pass before anyone realized that a machine had stopped.” Now the operator, as well as machining operations, a supervisor and manager all get an e-mail with the machine status update. Anderson explains, “From the operator’s point of view, the DataXchange notifications save them time if they don’t have to head to a building unnecessarily.” AMT also explored how DataXchange could be applied to process data, which was collected and recorded manually with a stopwatch as machines were physically monitored one at a time. He learned that “if you can see it and you can tell DataXchange how you can collect it, you can do it [within the machine monitoring system],” he says. Today the ISO 9001:2015, 14001:2015 and AS9100-certified company tracks cycle times for parts, cutting tool data for large format machines and probing data. The impact has been transformational. “We no longer rely on anecdotal evidence to understand the effects of machine downtime,” reports Anderson. “And our estimating is more precise, as we’re able to adjust pricing based on the data.”
ON THE HORIZON
Machine data now serves as the conversation starter on the floor to uncover issues and identify solutions. The third and final phase for AMT will be an upgrade to the gold licensing level of DataXchange and a roll out to all machines.
As the company takes on customer diversification, AMT is making strides towards cost and quality enhancements with the help of manufacturing integrator SFA and the DataXchange system. “We’re making cutting parts profitable,” Anderson says.
The content & opinions in this article are the author’s and do not necessarily represent the views of ManufacturingTomorrow
Comments (0)
This post does not have any comments. Be the first to leave a comment below.
Featured Product
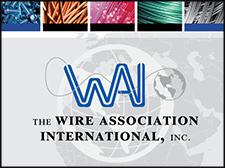