Manufacturers need to prioritize technologies such as 5G and IoT as they continue to develop and become more available throughout the organization in order to streamline their operations and survive In our digital-first future.
Manufacturers Making the Right Connections: IoT, 5G and Scaled Growth
Jasmeet Singh, Executive VP and Global Head of Manufacturing, | Infosys
Industry 4.0 is decidedly top-of-mind for manufacturers. Even the pandemic’s many hurdles did not deter them from continuing to push on their digital transformation plans. Now as they prepare for recovery and resilience, their aspiration although ambitious is tempered by pragmatism. The complexities of hybrid working, budgetary constraints, and in many cases teams wholly consumed with accelerating business have made the agenda harder. They are growing increasingly careful about the trade-offs they make between speed and scale, efficiency and growth. They know the quick fixes and savings-focused workarounds, from the pandemic-time, although necessary then, may end up needing time- and cost-intensive reengineering to scale and deliver continued value for the business. They are increasingly turning to hybrid cloud-based solutions and proven standardized platforms that they can rely on for much-needed quick returns but, at the same time, also scale on demand.
The prognosis is clear
By 2024, smart factory initiatives will play a pivotal role in driving manufacturing competitiveness and also completely change the way products are made. In fact, the global smart manufacturing market is valued between US$ 135-225 billion and by 2025, Industrial IoT (IIoT) will have the largest share of it. Already, IIoT, in conjunction with other technologies, such as artificial intelligence, augmented/ virtual reality and analytics, is yielding a vast number of use cases to streamline and automate manufacturing operations. Today, sensors are being deployed to monitor everything from equipment health and energy consumption to delivery fleet movement, cold storage temperature and the location of workers in hazardous environments. With the pandemic dislocating supply chains the world over, the industry is relying on IoT-enabled devices to run ‘smart’ inventory operations, from demand prediction to stock replenishment.
Predictive maintenance and digital twins are emerging as most value-generating use cases
By embedding IoT-enabled sensors in shop floor equipment, manufacturing companies can automate both detection of machinery malfunction as well as intimation to service personnel, to respond better to breakdowns and their associated impact. Beyond reactive detection and action, manufacturers, armed with historic data, can also predict, and thereby prevent issues. This averts costly downtime, and in addition enables businesses to anticipate service requirements and optimize their plans to staff for these requirements.
The ‘digital twin’, among this year’s top technology trends, is finding extensive application in the manufacturing industry. These applications include simulations for product design and development, predicting how materials perform under different conditions, improving shop floor operations and mimicking supply chains so businesses can improve them. In fact, companies that had invested in building digital twins of their supply chains and operations flow, before the pandemic, were greatly benefitted. They were able to test different scenarios easily and virtually, and shift to the most viable way of running the business when the pandemic brought several of their competitors to a grinding halt.
We’ll need 5G to give smart manufacturing a shot in the arm
Although smart factories have come far, their progress today is somewhat hampered by the inadequacies of connectivity. Wi-fi networks often suffer from interference in dense shopfloor environments, and fixed connections are difficult to manage in large manufacturing environments. But things are looking up with the entry of 5G technology, which will enable factories to control their machines and industrial robots wirelessly and take IIoT to its full potential for connected equipment in the field. Some of the biggest use cases of high-bandwidth 5G networks include improving the efficiency of visual inspection by enabling real-time edge analytics; enabling AR tools with real-time data processing capability to expand deployment possibilities; powering 3D printing of connected spare parts; and enhancing the adoption and performance of mobile robots.
Now’s the time to think growth and scale
Value grows disproportionately when manufacturers run not just successful IIoT/ smart manufacturing pilots but programs that can scale enterprise wide. This means evolving both legacy landscapes and mindsets - addressing the challenges of reengineering business processes for agility and nurturing the skills required to drive the transformation. Instituting governance and data security processes goes with the territory. Finally, orchestrating the tech layer with a microservices architecture that supports planned and unplanned growth, and devising a cloud strategy for resilience and flexibility, is what the sector needs to be more competitive.
.jpg)
About Jasmeet Singh, Executive VP and Global Head of Manufacturing, Infosys
Jasmeet Singh is executive vice president and global head of manufacturing at Infosys. His areas of expertise include business and IT alignment, transformational outsourcing and helping clients achieve their business goals. He brings a deep appreciation of business, business processes and the usage of technology as a strategic differentiator for his clients.
Prior to his current role, Jasmeet was the Industry Head for Financial Services in the Americas. Jasmeet started his career with Deutsche Bank as a banker post his MBA. At Infosys, he has progressed through various roles including starting out as an individual sales contributor to Head of Sales to Regional Head, Industry Head and to the current role of Segment Head of Manufacturing.
The content & opinions in this article are the author’s and do not necessarily represent the views of ManufacturingTomorrow
Comments (0)
This post does not have any comments. Be the first to leave a comment below.
Featured Product
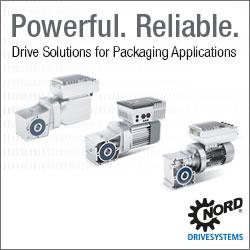