Manufacturers have long dealt with equipment failures. While they may be inevitable, equipment failures should not cause serious downtime, eat into profits or make manufacturers overspend their budgets.
From Downtime to Uptime - the Need for Predictive Maintenance
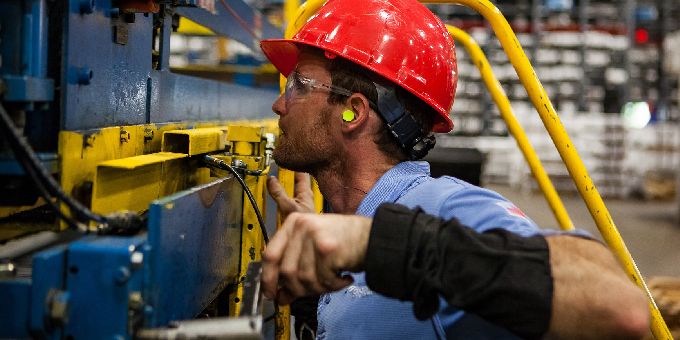
Claudia Jarrett, US Country Manager | EU Automation
“If it ain’t broke, don’t fix it” is a catchy phrase, but it’s not a good rule of thumb. Unscheduled downtime and poor asset quality costs manufacturing and process industries an estimated $20 to $60 billion each year. Unfortunately, such reluctance to embrace new technologies, due in part to the upfront cost, has hindered progress in operations. Here, US country manager at automation parts supplier EU Automation, Claudia Jarrett, explains why maintenance technologies can boost a plant’s profitability through increased uptime.
Manufacturers have long dealt with equipment failures. While they may be inevitable, equipment failures should not cause serious downtime, eat into profits or make manufacturers overspend their budgets. These are usually the worst-case scenarios — and the reasons why equipment failures must be avoided.
These challenges are compounded by the fact that today’s manufacturing facilities are far more complex than ever before, consisting of data networks, integrated hardware and a host of automated systems, and as a result most manufacturers do not have sufficient maintenance methodologies in place. In fact, a report from Infraspeak states that 93 per cent of companies consider their maintenance processes to not be very efficient.
This shines a light on the lack of effective maintenance programs in the manufacturing realm, leaving plants unsafe, less competitive and far less profitable. Thankfully, predictive maintenance offers a solution.
Predicting the future
Predictive maintenance is a way to predict every possible hardware failure scenario, identifying when maintenance is required and alerting maintenance staff, when necessary, as well as providing preventative solutions.
Anyone who operates within the manufacturing ecosystem will understand that failures and breakdowns happen day in, day out. The intention of predictive maintenance is not just to prevent or reduce these breakdowns, but to help manufacturing plants achieve high-efficiency standards and deliver quality products in the process.
A predictive maintenance program can reduce unexpected failure by up to 90 per cent, almost eliminating breakdowns. The first step to achieve this is ensuring your maintenance strategy follows best practices. For example, plant managers must schedule regular inspections, upgrades and troubleshooting to avoid breakdowns, forming a strong foundation for a predictive manufacturing program to build upon.
Sensing danger
To perform predictive manufacturing effectively, the plant manager should gather as much data as possible. This is crucial when implementing any preventative maintenance strategy, as the more data available to be analysed, the more accurate breakdown predictions will be.
A starting point would be to use smart sensors. Smart sensors, coupled with machine learning algorithms, help to detect anomalies in industrial machines. Plus, with better trained algorithms, software can accurately predict when machines are at risk of failure.
For example, smart sensors collecting data in industrial IoT environments can keep track of temperature, identifying worn components such as malfunctioning electrical circuits. Likewise, specialist smart sensors can perform vibration analysis on a particular component, identifying any cases of misalignment, bent shafts or other motor problems. As the technology grows more advanced, smart sensors can monitor more and more parameters, giving an increasingly accurate picture of the condition of a machine.
From this data, manufacturers can perform an analysis of the critical assets to establish failure modes. Here, the focus is on the frequency of failures, severity of machine failure and the difficulty of identifying failure.
By connecting condition monitoring devices to a CMMS, plant managers can set up alerts to inform maintenance staff of any faults or anomalies in the equipment. This provides the opportunity to plan for scheduled maintenance when parts need replacing, removing the chance of a serious breakdown from occurring.
For example, sensor technology can be integrated with several different low-level fluid power products — from connectors, hoses and tubing to pumps, motors, actuators and filters. Here, some of the diagnostic data generated from control valves could be vital in troubleshooting power issues.
On the uptime
A recent survey by PwC found that 95 per cent of respondents reported that predictive maintenance improved at least one key maintenance value driver, with 60 per cent seeing a clear improvement in equipment uptime.
However, for plant managers to see this success in their facility, using sensors to gather information on equipment is a critical component required. Recent machines usually come with different options for real-time data acquisition, but legacy equipment can also be retrofitted with inexpensive add-on sensors. Predictive maintenance can be a vital asset when dealing with ageing assets, which require careful planning to source obsolete spare parts.
This is where expert consultants at automation parts suppliers, like EU Automation, can help source parts and assist those in their predictive maintenance journey. Whether plant operators are looking for smart sensors to begin their predictive maintenance journey, or replacement parts to perform corrective maintenance on legacy machines, developing a relationship with a reliable parts supplier is essential.
While some extent of equipment failure is inevitable, it should not cause unscheduled downtime and poor asset quality, costing manufacturing and process industries billions each year. Instead, a fully-fledged and effective predictive maintenance plan will help to prevent and reduce downtime significantly, simultaneously boosting a plant’s profitably through increased uptime.
The content & opinions in this article are the author’s and do not necessarily represent the views of ManufacturingTomorrow
Comments (0)
This post does not have any comments. Be the first to leave a comment below.
Featured Product
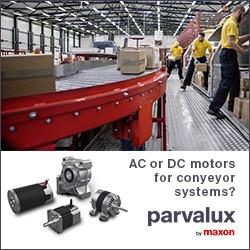