Digital Thermal Processing tools bring a sustainable approach and a new means of delivering applied energy for manufacturing. Allowing designers to build what they imagine, resolving the limitations of materials and processing temps on product design and manufacturing.
Advantages of Digital Thermal Processing
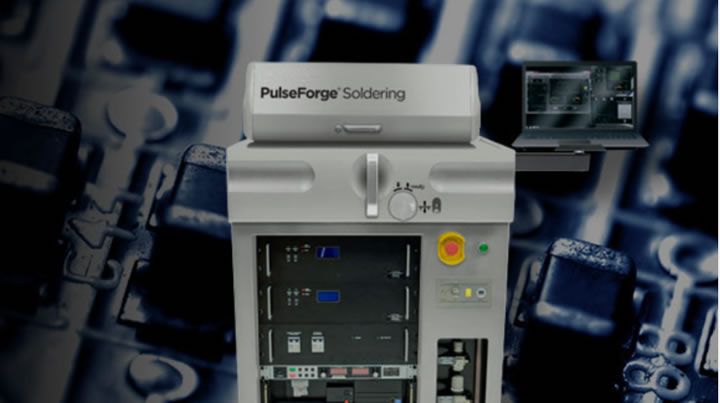
Q&A with Stan Farnsworth, CMO | PulseForge
Tell us about yourself and PulseForge.
My story and the PulseForge story are really inextricable, and actually began long before we started the company. My graduate school lab at the University of Texas had a group doing advanced electrothermal gun development work, and a curious powder residue was observed accumulating around the exit of the launch barrel. The powder turned out to be very unusual forms of nanoscale dust, which had interesting and, we thought, useful properties. So, in 1999 we created Nanotechnologies Inc, based on a pivot of the electrothermal gun technology into a nanopowder synthesis technology. One of the most frequent customer interests was in using the nanopowder silver for making electrically-conductive inks for the emerging printed electronics area. The inks were being printed on light-weight flexible substrates like PET plastic, but then needed to be heated to temperatures for processing that were higher than what the plastics could handle. So, we did another tech pivot and used the powder production technology to instead power very high-performance flash lamps. The flash lamps were engineered to be able to pulse with very high power and pulse rate to heat the materials. Physics was on our side and the inks heated faster than the substrates, enabling the conductive inks to be dried and sintered in milliseconds at high temps without damaging the substrates. We developed a new set of equipment to do this commercially, and PulseForge was born. Now, over 15 years after the first tool shipments, we have just this January 2022 spun out the tools business as a free-standing entity called PulseForge® Corp.
Can you explain what Digital Thermal Processing™ is and how it works?
The PulseForge tools selectively heat materials by taking unique advantage of the physics of heat transfer at shorter time scales, in a process we have named Digital Thermal Processing. The tools deliver very carefully controlled “doses” or bursts of energy which are used to establish very brief heating times, typically measured in milliseconds or perhaps a small number of seconds, wherein the materials that need to be processed are given just enough time to absorb just the right amount of energy to achieve the desired temperatures and achieve the desired results. The energy is delivered in such a way that the non-targeted materials are not given the time to absorb energy which would be damaging to them. As happy coincidences, this processing approach enables high-temperature materials to be processed without damaging thermally-sensitive materials, and also, by virtue of the very short non-uniform heating, utilizes a small fraction of the energy needed by conventional thermal processing. And, because the process is predicated on very short processing times, physics grants that the technique is inherently scalable, leaving it to engineering to in fact make it so.
At a higher level, PulseForge’s Digital Thermal Processing tools bring a sustainable approach and a new means of delivering applied energy for manufacturing. They allow designers to build what they imagine, resolving the limitations of materials and processing temperatures on product design and manufacturing. For example, the PulseForge tools can solder electronic components and batteries, actually melting the metallic solder, directly onto thin lightweight flexible plastic. It seems impossible but, works because of how we are using time and physics in our favor.
What industries can benefit from these tools?
A few industries have responded especially favorably, with electronics manufacturing being at the top of the list. Traditional soldering processes are at odds with the emerging opportunities in consumer applications such as AR/VR/metaverse, lifestyle and medical wearables, advanced conformable portable electronics, even reimagined and redesigned automotive interiors. Our technology enables next-generation light-weight versions of AR/VR goggles that look and feel more like eye masks than the awkward strap-on plastic boxes. It turns out that currently around 20 minutes is the rule of thumb for average consumer tolerance of wearing AR/VR goggles. Making the goggles lighter and more comfortable dramatically increases user tolerance, which in turn increases the opportunities for more involved commercial applications as well as more enriching user experiences around content and games. For medical wearables, sensors can be built directly on bandage-like patches, and not on detached test probes or cumbersome chunky designs. The benefits include more accurate, real-time monitoring of health conditions resulting in substantial lifestyle improvements and reduced health disruptions. There is a myriad of other potential non-electronics applications, and we anticipate growing into additional industries.
How are these tools different from traditional manufacturing?
In traditional thermal processing the entire set of materials is held to the same temperature, whether that temperature is increasing, being held steady, or decreasing. In fact, typically great care is taken to design thermal processing systems such that there are no hot or cool spots which might cause variations in how the materials being processed respond. The PulseForge tools with Digital Thermal Processing are taking a very different approach and are unlike any other traditional manufacturing tools.
Explain what makes Digital Thermal Processing a more sustainable form of manufacturing.
Sustainable manufacturing unpacks into a few aspects. Because the tools use energy on demand and are not designed to provide as much energy as would be needed to heat an entire volume of material, the total energy needed is thereby greatly reduced versus normal thermal processing. Only the amount of energy needed to process the desired materials is used. Also, because of the very short processing times, collateral heating of the equipment and surrounding workspace is virtually non-existent, so HVAC power is not as crucial for maintaining the correct workplace conditions. Because the tools do not require any warm-up time at start-up, they can be turned on moments before they are needed, and then switched off when they are not in use. There is no non-production energy burn. All of these combined means that the tools use only 15% or less of the energy needed by conventional thermal processing and directly contribute to decarbonizing the supply chain. We ran some estimates and broader adoption of these tools could single-handedly drop global greenhouse gas emissions by 1% or greater in the next 10 years.
The tools also change the limitations on materials which can be used in manufacturing processes. Light-weight materials can be used, reducing costs associated with transporting them, or fuel needed to carry them when incorporated into transportation applications. When using PulseForge tools, recycled/recyclable materials such as PET plastics, paper, or fabric can be used as base materials in many electronics applications. We have already connected with groups such as Sustainable Electronics Recycling International (sustainableelectronics.org) to better understand the implications of this technology in down-stream electronics recovery.
Digital Thermal Processing is also an important boost for additive manufacturing, in that it allows benefits of properties achieved with high-temp processing, such as those found with ceramics or metals, in conjunction with low-temp materials such as flexible and light-weight polymers. Additive manufacturing overall of course is attractive due to more efficient materials use versus subtractive processes, and reduced/eliminated by-products such as seen by wet-etch processes.
How do you think Digital Thermal Processing will change the way of traditional manufacturing?
We do see some important opportunities to implement Digital Thermal Processing right away in certain applications and manufacturing of certain products. Responses to experiencing the PulseForge tools in person, on well-known and well-characterized manufacturing examples are pretty compelling. When people see this in person, they quickly realize how this impacts not only their current manufacturing but also future products and designs. Towards this, longer term we see a direct connection between opportunities to improve manufacturing sustainability with opportunities for starting with sustainable design. We like to work with early product and concept design teams to help them realize that the manufacturing capabilities which constrain their creative and market vision can be tossed aside, freeing them to move ahead with truly visionary product, advanced products which still achieve climate goals. We are enabling next-generation products to reach the no-compromise future to which we all want and urgently need.
Where do you see Digital Thermal Processing in the future?
We envision a world with new products currently unimaginable, enabled by Digital Thermal Processing, and built to provide improved health and lifestyle while at the same time being smarter and more responsible to the health of the planet and all those who live here. By offering designers and producers new manufacturing technologies, we can let them better tap into their creativity without being hampered by current manufacturing constraints.
As wearables, AR/VR, aerospace, automotive, and solar markets continue to evolve, along with consumer expectations for performance and sustainability, our technology is proving key to enabling these to collectively be achieved, without compromise. It’s extremely important to us that we evolve with the industry and provide earth-friendly solutions to the global market. By combining increased performance and design flexibility, plus manufacturing efficiency and throughput, with dramatic energy savings, and at equipment pricing similar to or reduced from current solutions, we will make the earth-friendly choice the right choice by any consideration. This will change how businesses and brands operate, and empower consumers to make earth-friendly purchase choices.
Stan has been bringing technology innovation to markets and applications for over 20 years, with emphasis on pulsed light thermal processing for the past 15 years. As one of the founding members of NovaCentrix (2008) he was instrumental in bringing world-wide acceptance of pulsed light thermal processing to markets such as consumer electronics, photovoltaics, and RFID, along with diverse technical and scientific applications. Today, an estimated 600+ million products have been produced using this technology. As a founding member of Nanotechnologies Inc (1999), an early pioneer and recognized leader in the nanomaterial space, he set product and application priorities for nanomaterials and dispersions and led deployments in applications such as conductive inks and antimicrobial wound care additives.
Stan earned his BS in mechanical engineering from Rice University and MS in mechanical engineering from the University of Texas, Austin, specializing in heat transfer and fluid mechanics. Currently, he serves on the board as Chairman for the OE-A – the leading international association for printed and large-area flexible electronics. He is also an active Mentor at Capital Factory, the leading start-up ecosystem in the Austin area, where he advises entrepreneurs on marketing and sales topics. For the past 10 years Stan has also been the chair of the STEM advisory board for a local Austin area high school. In this capacity, he has been working to increase diversity in STEM education and improve awareness of technology opportunities for all students.
The content & opinions in this article are the author’s and do not necessarily represent the views of ManufacturingTomorrow
Comments (0)
This post does not have any comments. Be the first to leave a comment below.
Featured Product
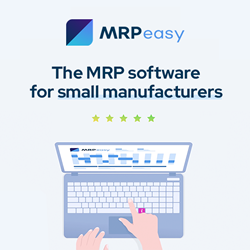