This article discusses how legacy manufacturing enterprises can harness the latest technologies, to optimize factory operations without having to ramp up infrastructure investment.
Transforming Legacy Manufacturing Enterprises With AI on the Edge
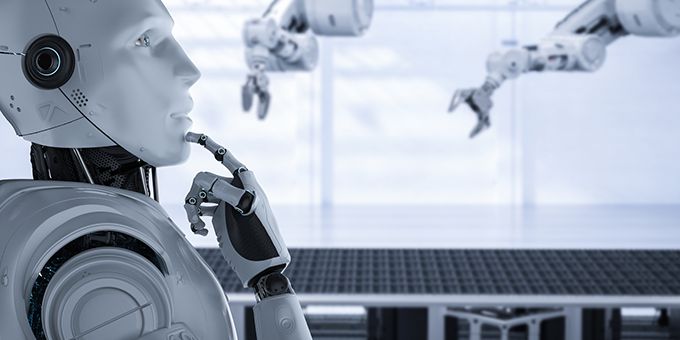
Rinat Akhmetov, ML Solution Architect | Provectus
Manufacturing enterprises often operate in a cut-throat environment. Pressured by competitors from abroad and at home, they seek new ways to improve the quality of their products, reduce production costs, and boost the efficiency and flexibility of their operations. Advances in such “smart” technologies as artificial intelligence, cloud and edge computing, and IoT, fueled by an explosion of data, have created ample opportunities for companies to not only stay in the game, but to gain a significant competitive edge. This article discusses how legacy manufacturing enterprises can harness the latest technologies, to optimize factory operations without having to ramp up infrastructure investment.
AI and Smart Edge Computing
Today, businesses know that data can be one of their greatest assets, provided it is collected, processed, and analyzed in a timely manner. And while this is also true for manufacturing, the challenges that manufacturers have to overcome are quite different.
In a manufacturing environment, the data points from machines, programmable logic controllers (PLCs), industrial IoT devices, and supervisory control and data acquisition (SCADA) systems are so varied that it becomes difficult to integrate the data for further processing and analytics. Manufacturing enterprises may have the tools to collect data, yet they often lack the technology to overcome connectivity, integration, and scalability issues, which limits multi-plant roll-outs of any AI- and analytics-powered “smart factory” solutions. This is where edge computing can help.
Edge computing is a distributed information technology architecture, in which computation and data storage are brought closer to data sources. This enables organizations to avoid handling all of their data in centralized servers, but processing it using on-premise edge computing devices. Only aggregate data, or metadata, is brought back to their central systems for advanced algorithm work and analytics.
In the context of manufacturing, the data collected from millions of connected devices is mostly processed on-site by edge devices (e.g. AWS Panorama, Azure IoT Edge) and is pushed to the cloud only when readings indicate a problem, like an unusual rise in temperature or slower machine response time. With edge devices on the factory floor, manufacturers gain the ability to quickly understand the data so that problems can be identified and solved in near real time. They do not need to implement and accommodate overly complex, expensive, and time-inefficient analytics systems that push data back and forth between multiple clouds and services, to report a problem or generate a prediction.
Speed, though particularly important in manufacturing where real-time interventions are a given, is hardly the only advantage of edge computing compared to cloud-based data processing and analytics.
Reliability of systems based on edge computing often tips the balance in their favor, too. Just imagine: You have a connection problem (i.e. cloud is not responding) but your automated assembly lines keep running. It means that you are going to lose data, which means missed defects, botched analytics, operation problems along the production line, and more. This is not the case with edge computing — edge devices will keep doing their job even if your connection is slow, off and on, or temporarily down. Another perk is that every edge device operates as an individual unit, adding reliability to the entire system; if one device goes down, it will not affect operations.
Profit margins in manufacturing are slim, and any technology deployed on the factory floor should drive revenue growth high enough to justify its expense. Fortunately, with edge computing, cost-efficiency is the name of the game, so long as it is implemented properly. Cost savings come from edge computing architecture, which lowers the cost of connectivity, data movement, and data processing.
Security is another strength of edge computing. Because edge systems are decentralized, they do not have a single point of failure. If one of your edge devices in the network is hacked, it can be easily isolated through specific security protocols, nipping the problem in the bud.
Scalability of edge computing is also great: you can deploy and manage as many devices as you need in a flexible manner, based on the factory’s size, throughput, and other production specifics. Because such solutions do not depend on centralized processing, every factory can address its implementation routine, based on its own requirements.
The ability to process data on-site in real time makes edge computing a perfect “smart factory” solution for legacy manufacturing enterprises. By deploying edge devices, companies can cost-efficiently collect, process, and analyze readings from their machines, video streams from cameras, and sensor data without the need to reinvent their entire infrastructure and workflow. Here is how these implementations may look from a use case standpoint.
Manufacturing Use Cases for AI on the Edge
Edge computing can be used in various scenarios. In manufacturing, its benefits are realized in three major use cases:
Predictive Maintenance. Every manufacturer knows that a good predictive maintenance routine results in fewer equipment failures, reduced mean time to repair (MTTR), increased asset lifetime, improved workplace safety, and increased ROI, just to name a few advantages. Edge computing can enable you to significantly improve predictive maintenance procedures through better data collection, integration, and processing. With the help of AI and machine learning algorithms, you can now take advantage of this data to not only “signal a failure,” but to predict when failures are likely to occur and when your machine is going to need maintenance. And bear in mind that, since “AI work” is done on edge, it is at least 10-to-20 seconds faster than centralized processing — a critical advantage on a production line.
Product Quality Control. In an industry where quality-related costs can eat up to 20% of sales revenue, it is critical to detect defects at the earliest stages of production. Manufacturers have been investing in defect detection and visual inspection systems for years, but only the more recent advances in computer vision (CV), machine and deep learning can help ensure that defects can be found early, with high accuracy. Edge computing allows the processing of data collected from automated optical inspection (AOI) systems, or they can be integrated with “smart” cameras that input visual data to CV and DL algorithms to identify defects. In other words, you can install edge devices but keep using your AOI or any other type of visual sensor to collect data; AI on the edge will do the rest.
Process Monitoring and Control. Edge computing can be used to collect and process data on various aspects of the production process. By analyzing visual data from cameras, it can help you monitor material and product flow through the production chain, control physical access to the premises, ensure PPE compliance, and collect and analyze worker performance metrics. The beauty of AI-on-edge solutions is that they are easy to implement, and they deliver actionable insights almost immediately. A straightforward system with just a couple of cameras and a single edge device can add visibility to your workflow and provide you with insights, to optimize operations and eliminate bottlenecks. You do not have to install dozens of cameras, develop state-of-the-art ML algorithms, and revamp how things are done at your factory to determine the best action to take.
What’s Next for Legacy Manufacturing Enterprises?
Visionaries say that the fourth industrial revolution is upon us, and it seems that even the sturdiest legacy enterprises will have to modernize and invest in new technologies. But does it make sense to completely reinvent your business?
It goes without saying that artificial intelligence, machine and deep learning, computer vision, cloud and edge computing, industrial automation, robotics, and other “smart” technologies can be quite challenging to implement. Nevertheless, they are already delivering value, and organizations will continue to expand the variety of use cases.
AI on the edge provides an alternative to more complex, cloud-based AI and analytics solutions. It harnesses “local” data, which resolves the challenges of connectivity. Edge devices collect data points in specific formats (based on predetermined requirements), which makes it easier to integrate data for further analysis and analytics. The devices come distributed and decentralized, which can dramatically accelerate multi-plant rollout.
If you are a legacy manufacturing enterprise, your future is at the edge.
About Rinat Akhmetov, ML Solution Architect
Rinat Akhmetov is the ML Solution Architect at Provectus. With a solid practical background in Machine Learning (especially in Computer Vision), Rinat is a nerd, data enthusiast, software engineer, and workaholic whose second biggest passion is programming. At Provectus, Rinat is in charge of the discovery and proof of concept phases, and leads the execution of complex AI projects.
The content & opinions in this article are the author’s and do not necessarily represent the views of ManufacturingTomorrow
Comments (0)
This post does not have any comments. Be the first to leave a comment below.
Featured Product
