Matrox Imaging’s robust vision software and smart camera endows CNC machine to ensure precision cuts, enhance yield rates
Sharpening Alignment for More Accurate and Faster Machining
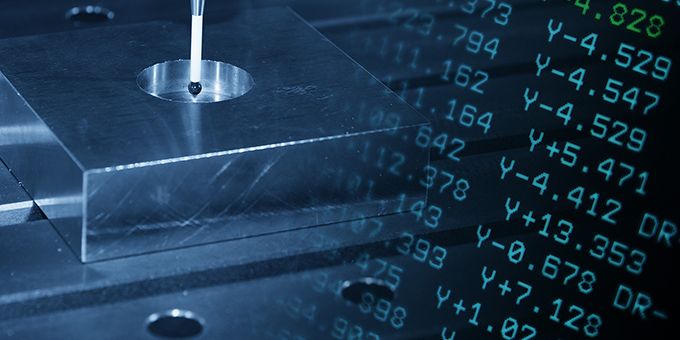
Sharpening Alignment for More Accurate and Faster Machining
Case Study from | Matrox Imaging
Founded in 2003, G4 Technology is one of the largest providers of machine vision components in the Taiwanese industrial imaging sector. Their principles are leading international manufacturers of machine vision and automation technology, delivering efficient, cost-effective ways of monitoring production lines and implementing automated quality assurance.
Backed by a team of experienced machine vision professionals, G4 Technology expertly helps customers—from OEMs to SI to end-users—develop solutions, integrate components, and provide prompt technical support to customers with wide-ranging application needs.
Getting the system into alignment
In cooperation with several computer numerical controlled (CNC) machine manufacturers, G4 set out to develop an alignment application for the machine tool manufacturing industry in Taiwan. CNC machines are material working tools that produce complex parts required by modern industries. The term “CNC” broadly refers to machines that utilize computer logic to control movements and handle the machining of metal or other rigid materials, such as glass or ceramic. CNC machines perform a variety of tasks, including cutting, boring, grinding, shearing, or deformation; CNC machining is a manufacturing process where a computer system runs programs that control how parts are manufactured.
“For CNCs to operate effectively, the object being machined must be correctly aligned before the machine goes to work; if the initial position or angle of the object is wrong, the machining process could fail, resulting in needless waste and loss,” noted Steven Ko, technical marketing manager at G4 Technology.
It is necessary for the machine to be physically well aligned before the machining begins; however, sometimes alignment is difficult to achieve due to imprecise adjustments using software parameters within the machine tool controller, or resulting from human negligence. G4 Technology sought to develop a solution that integrated a machine-vision-based alignment system directly into a CNC machine.
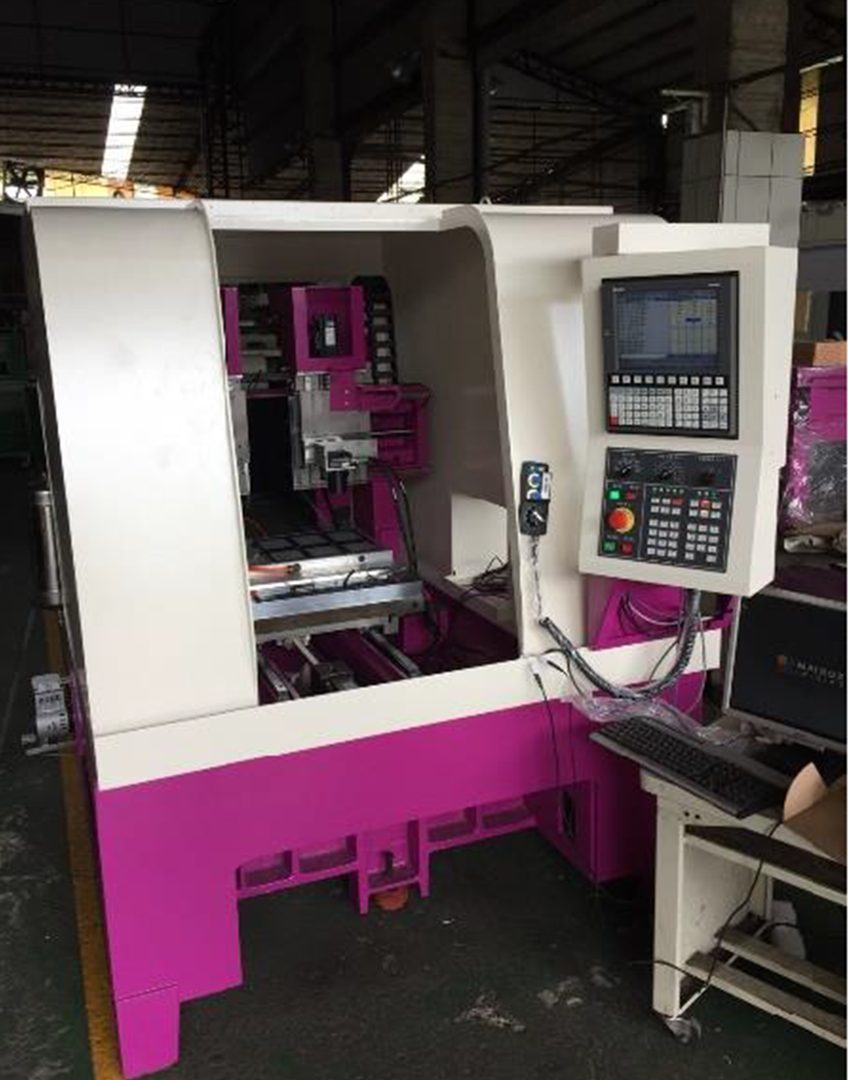
The CNC machine tool augmented with vision technology by G4, showing the workspace in which the Matrox Iris GTR smart camera is located.
Solving for alignment
In collaboration with several Taiwanese manufacturers, G4 Technology built a vision system comprising a Matrox® Iris GTR smart camera and powerful Matrox Imaging Library (MIL) X software. “G4 has been a good partner of Matrox Imaging for years, and our engineers have lots of experience with these products,” Ko reported. “Moreover, Matrox Imaging is able to provide sales and support information in Chinese—our mother language—which is invaluable for effective, accurate communication with both the sales and technical side of our business.”
Selected because of its processing power, compact size, and IP67 rating, “the Matrox Iris GTR delivers a better solution overall, compared to similar options from different manufacturers,” noted Ko. CNC machines regularly use a cooling and lubrication fluid during their operation, so the degree of waterproofing the IP67 rating provides helps avoid this fluid seeping into the smart camera. Matrox Iris GTR leverages a dual-core Intel® processor running Microsoft® Windows® to execute inspection tasks, and the camera provides the necessary connectivity and ports to facilitate complete integration into an automation machine. The Matrox Iris GTR is equipped with a 0.4x macro lens from Tokyo Parts Center (TPC) in order to obtain the correct working distance and field-of-view.
Similarly G4 determined that MIL X provides the tool for accurate alignment. Ko notes: “We used MIL X’s Geometric Model Finder (GMF) tool to get the correct position and angle of objects using their geometric features or contours. GMF parameters can be adjusted and models can be edited to optimize performance. The software then sends the data to the Delta CNC controller, which controls, automates, and monitors the movements inside the machine.”
Lining up the process
With the loading complete, the Delta CNC controller triggers the machine to move the piece in question to the cutting area and triggers the Matrox Iris GTR camera, which takes a series of images and calculates the position and angle of the piece. The smart camera then performs the analysis, sending the results back to the CNC controller. If the data is correct and meets the previously determined criteria, the CNC will start cutting; if not, the CNC will revise the position and angle of the piece until it is correct, then begin capturing and analyzing the images again until successful. In the case of G4’s application, if the relative position between the GMF tool position and the position of the piece is incorrect, the controller can realign the piece multiple times until the position and angle are correct. Operator interaction with the system is minimal, with the operator monitoring the CNC as it works on the piece.
Engineering a solution
Development of this vision system involved three key individuals: an engineer from G4 Technology who wrote the sample code for the application, as well as an electrical/mechanical engineer and a software engineer from one of the CNC machine manufacturers who collaborated on this development. Said Ko, “We did not encounter any big challenges during the application development process. Still, it took time to think through and verify the algorithm to ensure we could get the correct cutting path in a consistent fashion.”
Shaving off time while enhancing accuracy
With their previous system, performing this type of machining alignment would take between 30 to 60 seconds per piece to get a correct processing path. With their new Matrox Imaging-based solution, Ko noted that “it now takes around 15 seconds to complete the same analysis, therefore we have increased the output speed by anywhere from two to four times. And, since the pieces being cut need to be scrapped if they are cut on the incorrect path, we have seen an increase in cutting accuracy of 5-10% with this new system. G4 Technology couldn’t be more pleased.”
Conclusion
Their application successfully developed and validated, G4 Technology had planned to showcase their success at the 2020 Taiwan International Machine Tool Show; however, the global pandemic has curtailed those plans. That noted, “the use cases for this application are wide ranging, and we anticipate finding other such applications for the machine tool industry, focusing on visual inspection and measurement. We also foresee many possible applications in the field of machine and robot guidance,” Ko concludes. “Thanks to Matrox Imaging’s machine vision tools, we can now be fully confident in delivering a precise processing path for machining, and improve customer yield rates while guarding them against material loss with this CNC upgrade.”
The content & opinions in this article are the author’s and do not necessarily represent the views of ManufacturingTomorrow
Comments (0)
This post does not have any comments. Be the first to leave a comment below.
Featured Product
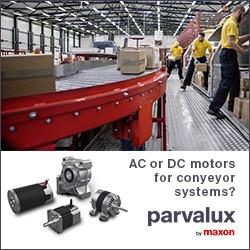
Strain Wave Gearheads by maxon - Highly precise, compact, and efficient.
Strain wave gearheads are ideal for use in applications requiring precision motion control and high torque transmission in a compact design. maxon strain wave gearheads are a specialized type of gearhead where precision and compact design are crucial. This type of gearhead is often used in applications in a confined space. With their advanced gear tooth design, maxon's strain wave gearheads provide high efficiency and good back drivability. Typical applications include:
Robotics, Aerospace, Medical technology and Optical systems
.