Often robots have enough mass, speed, and inertia that any contact with humans creates the primary hazard; process driven hazards, for example sparks/splatter and UV light in a robotic welding process becomes the secondary hazard.
Protecting Workers from Manufacturing Hazards
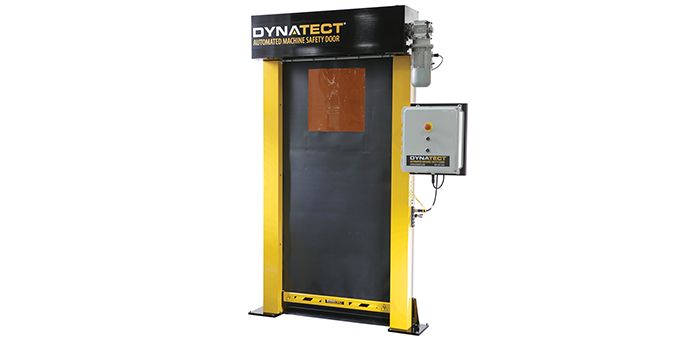
Article from | Dynatect Manufacturing
Manufacturing industries continue a strong trajectory of automation, especially for applications with dangerous processes. Even with automation, processes may still contain a human “interaction point” that requires additional safety and/or engineering controls for machine operator safety. When that interaction point is intermittent or exceptional, light curtains have been the traditional protective device. Their advantage includes allowing fast operator access without having to manually open a protective door. Light curtains, however, have limitations as they are not physical barriers ultimately increasing required space dedicated to safety. Additionally, they can be falsely triggered by the machine operator or other activity introducing further inefficiencies to an automated process. As a result, there is an increasing demand for the solid protection of automated high-speed doors which allow fast, periodic access without being victim to false triggers.
Typical hazards in a manufacturing application may include smoke, sparks, dust, weld splatter, debris, and fluid splatter. An additional hazard is the exceptional product assembly failure that can eject broken components in dangerous ways. It is ironic that sometimes in the process of the automation itself, like a large robot, can introduce another hazard. Often robots have enough mass, speed, and inertia that any contact with humans creates the primary hazard; process driven hazards, for example sparks/splatter and UV light in a robotic welding process become the secondary hazard. Fortunately, high speed doors can address all those issues where light curtains cannot.
There are many “product assembly” applications where the standard process has the operator bring raw materials or trays inside a work cell. Upon exit, the door closes quickly, protecting the operator from the moving robotics/automation in addition to the process generated hazards. Diverse industries use these doors including automotive, industrial, medical, and food processing. The applications range from light assembly, to palletizing, to robotic welding, to laser welding. The applications often need some customization, and this is where Dynatect’s modular design capability really shines. Here are a few examples:
- Lead Dust: An automotive application included production of lead-cell batteries, and a door was needed to limit the spread of lead dust. This further required sealing off the area between the door legs and a wall. For Dynatect, this wall adapter is a standard option and proved an easy addition to contain process generated hazards.
- Laser Safety: An automotive application used laser welding, which required the fabric roll up door to be replaced with a metal roll up door. The laser safety officer at the integrator and the end user both confirmed that the metal door exceeded the protection needs of the 4kW laser application.
- Palletizing: There are many applications where the last step is stacking the product on a pallet and shrink wrapping it via automation. During that process, operators must be protected via a door from the stacking and wrapping process – as well as the exceptional condition where the stacked product falls. Light curtains don’t protect from this condition, and the high-speed door still provides fast access by the operator and fork truck when the process is complete.
- Medical Applications: The pandemic is driving the increased need for automation in the medical sector. Dynatect has a recent application where an automated hypodermic needle manufacturing process also requires protection. In additional to high-speed access for operators loading and unloading the cell, the operators are also protected from the shrapnel created when the automated assembly has unexpected product failures.
- Saving Space: Many applications are space constrained, and the square footage consumed by safety protection devices can be significant. There are standard hazard formulas that define minimum safety distance between the safe-guarding device and the nearest point of operation hazard. In the case of light curtains, this distance is large since it isn’t a physical barrier, and the process must be stopped when the light curtains are triggered. This can be further complicated by the variations in light sensor density which may allow a finger vs. a wrist vs. an arm. All that complication is or can be eliminated with a fabric or metal door where the edges are firmly contained in the legs. This solid barrier allows the doors to be placed closer to the process and resulting in an average space savings of 27 square feet.
- Customization: Several applications may require the manufacturing cell to be accessed at different intervals or at different times to maintain production. This may necessitate the need for two doors side-by-side. Each door would normally have two integral support and curtain guide legs, but often there may not be enough room available. Our modular design allowed us to provide a common leg with channels for both doors to operate in the allotted space.
Dynatect has built our high-speed door by offering modular elements, durable design, ability to customize, simplified controls, and ease of installation. Dynatect is constantly providing personalized service to satisfy new applications for the metal and fabric high-speed automated machine safety doors.
Dynatect Applications:
Industry & Application: Automotive, Laser Welding
Primary Hazard: Laser radiation & robotic movement
Secondary Hazard: Intense light, smoke, sparks
Operator Access: Operator loads component pieces for robot, unloads complete product
Notes: Guarding entry/interaction point of 4kW laser welding application. MUST be light-tight and capable of withstanding operational specifications. The modular solution was reviewed by the LSO (laser safety officer) at both the machine builder/integrator and end user, meeting and exceeding operational expectations.
Industry & Application: Medical, Manufacturer of pharmaceutical manufacturing equipment
Primary Hazard: Motion of the robot during assembly/material handling
Secondary Hazard: Exceptional loose flying debris under malfunction
Operator Access: Operator loads component tray for robot, unloads complete tray
Industry & Application: Automotive, Lead Battery Assembly
Primary Hazard: Motion of automation
Secondary Hazard: limit lead dust/exposure and any other process driven hazards
Operator Access: Exceptionally access the process in the case of a non-conformance in the automation.
Industry & Application: Automotive, Automated line for rejected parts
Primary Hazard: Robotic & Automation movement
Operator Access: Had to exceptionally access rejected parts
Comments: Very large doors
Industry & Application: Automotive, Robotic Welding
Primary Hazard: Motion of the robot
Secondary Hazard: Weld UV light, smoke, sparks, splatter
Operator Access: Operator loads component pieces for robot, unloads complete product
Industry & Application: Automotive/Metals, Robotic welding of aluminum castings
Primary Hazard: Motion of the robot
Secondary Hazard: Weld UV light, smoke, sparks, splatter
Operator Access: Operator loads component pieces for robot, unloads complete product
Industry & Application: Consumer Goods, Material handling/end-of-line palletizing for health and beauty supplies
Primary Hazard: Robotic Palletizing and stretch wrapping
Secondary Hazard: Products being packaged can exceptionally fall
Operator Access: allows access by fork trucks to wrapped pallet/product
Industry & Application: Waste disposal, material handling/garbage disposal
Primary Hazard: Motion of the robot
Secondary Hazard: Exceptional loose flying debris under malfunction
Operator Access: Operator loads component pieces for robot, unloads complete product
Industry & Application: Material Handling, end of line palletizing operation
Details: Company specializing in automated warehouse solutions, including automated conveyer systems and pallet flow racking systems
Primary Hazard: Robotic Palletizing and stretch wrapping
Secondary Hazard: Products being packaged can exceptionally fall
Operator Access: allows access by fork trucks to wrapped pallet/product
About Dynatect
Dynatect Manufacturing delivers engineered protection and motion control for machines with deep application knowledge, diverse product offering, and a customer responsive sales philosophy. Dynatect provides engineering and manufacturing for custom applications which improve human-machine safety and machine uptime. Dynatect continues to build on its customer experience through improving service differentiation, expanding product portfolio, and reducing lead times.
The content & opinions in this article are the author’s and do not necessarily represent the views of ManufacturingTomorrow
Comments (0)
This post does not have any comments. Be the first to leave a comment below.
Featured Product
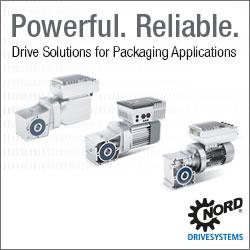