The adoption of automated systems should be based on a clearheaded commercial and technical analysis to strike the right balance between speed, cost, quality and value.
Readers Choice 2020: Strategic Approaches for Implementing Automation in Industrial Manufacturing
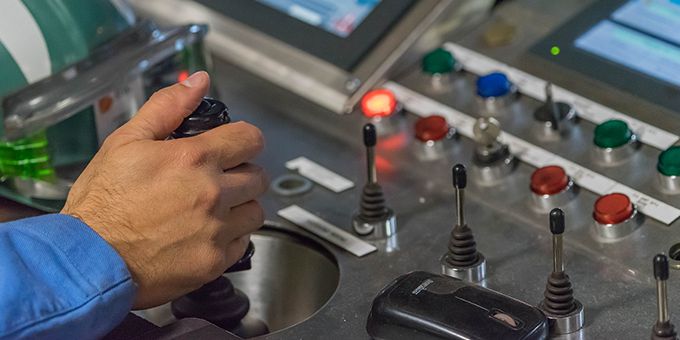
Mulugeta Abtew, Vice President, Technology Development | Sanmina Corporation
Automation has become a necessity for modern manufacturers to improve factory efficiency, ensure product quality and lower total costs. However, manufacturers should not fall into the trap of arbitrarily applying technology for technology’s sake. The adoption of automated systems should be based on a clearheaded commercial and technical analysis to strike the right balance between speed, cost, quality and value.
As new automation technologies emerge for industrial manufacturing, organizations should become more strategic about when they deploy automation, and when it does not make sense for their purposes. Whenever automation makes sense, it’s important to set up strict review gates at every step to optimize the technological and commercial gains.
Between the extremes of complete automation and no automation, varying degrees of automation can be applied to provide the best value at the right stage of a production process. For example, a single robot can be used to solder a product because it is a simple, redundant step that provides a good return on investment. Other examples include the use of robotics to lift heavy equipment and materials for products that are produced in high volumes, or autonomous factory vehicles that deliver materials to the factory floor at the proper stage of a production process.
Certain products require routine, pristine and error-free assembly to meet the needs of their original equipment manufacturers (OEMs), in which case automation is a good fit. Such products may include automotive controllers, or consumer medical devices such as heart monitors.
On the other hand, automation is not the best solution for large telecommunications assemblies that are made to operate within network infrastructures. Such low-volume products contain multiple heavy parts that require substantial investment in order to automate their production, making the return unattractive. In addition, complex medical systems such as MRI machines are highly sophisticated products that require precision assembly with strict tolerances. Attempts to automate such assemblies demand costly, custom automations with limited scalability.
Evaluation Checklist for Strategic Automation
Before deploying automation, manufacturing organizations should take several strategic steps. First, prepare a thorough audit of current manufacturing processes to gain a deeper understanding of how factory systems work, and how they can be improved. In this way, manufacturers can choose an optimized solution that consistently meets both the technical and commercial targets of the business.
The next step involves developing a strong business case to drive the initiative. The overall objective, vision and strategy for automation must be mapped out and aligned to the digital transformation strategy of the enterprise in a formalized process, along with the best ways to monetize its application. Projects that apply automation in a reactive manner without justifying their value usually fall flat on their investment, and the broader rollout of the technology can quickly lose momentum within the company.
The third step involves doing extensive research of the available market options. Organizations should look for automated systems with proven data collection capabilities that enable critical manufacturing data to be optimized for analytics, as well as predictive and preventative maintenance. Cloud-based manufacturing execution systems that aggregate, correlate and analyze data from machines on the factory floor provide the most flexibility and can be scaled up or down as needed.
Weighing Design Considerations for Automated Production
Another aspect of automating a factory involves a range of considerations that must be weighed by design engineers. They should conduct a full upfront design review, including a complete risk assessment and consideration of any commercial issues that could arise. If production is automated without undertaking a series of tests and validations to address any limitations, the process will result in technical gaps and a loss in product quality.
For this reason, design engineers must take several factors into account, including:
-
Volumes of Product Parts and Number of Assembly Steps. If a process is appropriate for automation, the number of parts and fasteners should be minimized, along with the corresponding number of assembly steps. It’s important to account for any tolerances, along with the inner spacing of parts. Even product colors and dimensions should be considered when making plans for automation.
-
Types of Product Materials. If fittings or screws are needed for an assembly, that can increase the number of needed parts while increasing the likelihood of production errors. For this reason, materials should be designed to be most suitable and efficient for automated manufacturing.
-
Enabling Real-Time Automated Inspections. Product designs should be developed in ways that can be automatically inspected, by collecting the right data to predict risks or prevent failures during the manufacturing process. The goal is to immediately identify any false errors on the production line, such as rejecting a good product or accepting a bad one.
-
Ensuring Controls for Product Handling. Lastly, the product must be capable of being easily handled and transported, so that a robot or technician can pick it up and place it in another location as it goes through the various production processes.
The goal of achieving a fully autonomous factory that runs by itself with little to no human involvement and zero waste, repair or energy loss remains a vision of the future for most manufacturing organizations. We are still not there yet as an industry. Until that day arrives, it is especially important to be strategic about when to implement automated systems, and when to stick with reliable manual processes.
The content & opinions in this article are the author’s and do not necessarily represent the views of ManufacturingTomorrow
Comments (0)
This post does not have any comments. Be the first to leave a comment below.
Featured Product
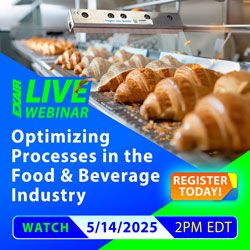