In a world waiting to take its next move after the COVID-19 pandemic, we'd like to offer you and your team design resources for injection molded parts to help keep skills sharp during this uncertain time.
eBook from | Xcentric Mold & Engineering
Will you be prepared to get back to business?
In a world waiting to take its next move after the COVID-19 pandemic, we'd like to offer you and your team design resources for injection molded parts to help keep skills sharp during this uncertain time.
- Design for Manufacturability eBook
- Injection Molding Best practices
- Leveraging Mold Flow Analysis to Improve Part Design
Why Xcentric?
We are the #2 rapid injection molding company in the USA,
located and made entirely in Michigan.
- Located and made entirely in the USA
- Prototype, bridge, and production
- In-house mold makers
We place on-site subject matter experts at every stage of the product development process, from CAD to production, to ensure your project is completed on-time, on-quality and on-budget.
Xcentric is a trusted partner for custom injection molding solutions. Please contact us to discuss upcoming projects, learn more about design best practices, or to share concerns regarding your post-COVID-19 ramp up.
If you have a project for which you need pricing or guidance, please request a custom injection molding quote and an Xcentric sales engineer will contact you within 24 hours.
The content & opinions in this article are the author’s and do not necessarily represent the views of ManufacturingTomorrow
Comments (0)
This post does not have any comments. Be the first to leave a comment below.
Featured Product
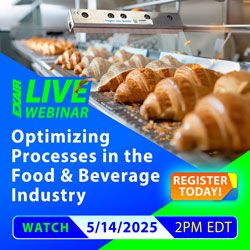