Industry 4.0, or the fourth industrial revolution, has called for a merger between automated solutions and smarter, more effective operations through the application of real-time data collection.
What Machine Learning Trends Can We Expect for Manufacturing in 2020?
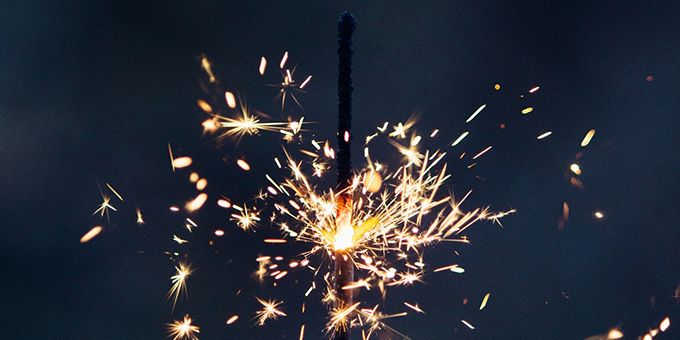
Emily Folk | Conservation Folks
Essentially, IoT and data-based technologies will feed real-time content into an AI platform, which will then use machine learning algorithms to analyze and extract actionable insights. Beyond that, the data solutions may support additional power systems by controlling robots or informing various processes to influence output.
In other words, machine learning and AI allow for a degree of autonomy in the field like never seen before. While they are incredibly promising technologies, they're still relatively new to the industry, which means manufacturers are looking for fresh and innovative ways to apply them. It makes a lot of sense, then, to consider some of the associated trends that will be taking hold throughout the coming year.
How will manufacturers apply AI and machine learning in the year ahead? What kind of improvements and innovations can we expect to see?
1. AI as a Service, or AIaaS
Rather than developing or building complex artificial intelligence solutions in-house, it’s now possible to employ one of many different cloud-based solutions. More importantly, the service-based solutions that do exist have come a long way in recent years, growing in reliability and accuracy as they ingest more and more data.
Google’s Cloud AI Platform, Amazon’s Web Services, IBM’s Watson and Microsoft’s Azure Platform are all excellent examples of AI and machine learning solutions based in the cloud. As we head into 2020, they will continue to dominate across all sectors. What this activity means for manufacturers is quite simple. Not only will it be possible to deploy cloud-based intelligence and neural network solutions, but doing so will soon become necessary to thrive in the coming landscape.
2. AI-Powered Quality Control
One of the biggest challenges modern manufacturers deal with is the act of maintaining quality control throughout the production line. It’s an incredibly involved process that requires active monitoring both during and after manufacturing.
With AI, however, most of the work can be automated. Primarily, it allows for real-time alerts and communications, backed up by a system that can also take action when problems arise. For example, a malfunctioning assembly line could be paused instantly at the sign of trouble. The appropriate alerts are then sent to floor supervisors and plant managers, who can take a look. They're given detailed information about the problem, why it’s happening and even potentially what fixes are relevant.
The best part is that machine learning and neural network solutions ingest data to grow smarter and more useful as time goes on. When they're applied to quality control solutions, it means every operation could see increasing levels of accuracy from the AI platforms.
3. Distributed Manufacturing
Thanks to 3D printing, mass customization is now possible for various products and goods. The technology also introduces a new opportunity in distributed manufacturing. It shifts processes like assembly, development and packaging closer to the end-users. Small- to medium-scale distributed manufacturing operations offer reduced costs, faster product-to-market cycles and increased personalization. That said, the coordination of such programs will need support — queue artificial intelligence and machine learning.
Using a combination of smart technologies — IoT included — and AI, manufacturers can deliver faster service despite incredibly nuanced orders. The AI solutions can help source materials to build the best product while also supporting extraneous operations like responding to consumer demand trends, identifying popular local markets and more.
4. Safer Work Environments and Smarter Cobots
Generally, advanced robots operate under a series of programmed patterns with various sensors used to interrupt services. An employee’s arm or finger that broaches a guarded boundary might shut down the machine, for example. While these kinds of systems are safer and much more capable than their predecessors, there’s still a degree of risk involved. If the sensors mentioned above break down or experience errors, the safety system in place might not activate in time.
Machine learning and AI, however, can add a degree of awareness and perception to collaborative robots. Mainly, such a development would allow for more reactive events, many of which border predictive systems. Operational robots can actually sense what’s happening around them to avoid disruptions, dodge danger and even avoid harming others. The sensors collect and transmit data in real-time, feeding into an AI controls system behind the scenes. Much like a self-driving vehicle, it powers the robot in a more streamlined way, thus creating a much safer work environment for all.
Unprecedented Levels of Efficiency Are Coming
As one may have noticed, many of the technology trends discussed point to an unprecedented level of efficiency and output in the manufacturing world. AI and machine learning will power many of the related solutions, allowing a genuinely hands-off approach for managers and executives. More importantly, the improvements will translate to better and higher-quality products for customers, as well as much safer and more favorable work environments for the average plant employee.
2020 is shaping up to be one of the most innovative years for manufacturing, at least in a long while.
If you like this article you may like "Predictive Analytics vs Machine Learning"
The content & opinions in this article are the author’s and do not necessarily represent the views of ManufacturingTomorrow
Comments (0)
This post does not have any comments. Be the first to leave a comment below.
Featured Product
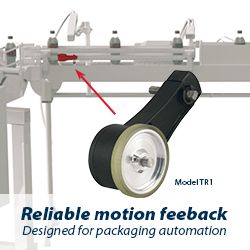