Other countries, as well as your competitors, are adopting new automation technologies that are allowing them to be more competitive. Look at automation concepts as an opportunity to keep yourself and company relevant.
The First Step to Automating Your Production Line
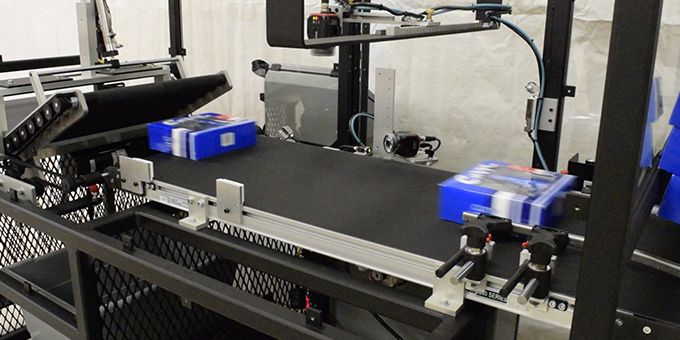
Lisa Maurer, Content Marketing Specialist | Trimantec
You won’t know if you have an aptitude for automation technology until you begin planning. Initial planning is as easy as determining whether your production line will be more efficient as a fixed, programmable, or flexible design.
Before you begin talking to your IT department about communication interconnectivity and software and hardware from the Internet of Things (IoT), start by looking over your current manufacturing floor set-up and think like a machine designer. Examine the efficiencies of your current system and look for bottlenecks. Encourage employees to share experiences and ideas for improving production line flow. Those on the front lines can provide a wealth of innovative ideas for creating automation efficiencies. Once you have an idea of the production areas in most need of improvement, then you can start to think about the machinery.
For an optimal rate of return on machine expenditures, a machine designer needs to know the following before automation can be designed:
-
Are products produced in units, batches, continuously, or in a mass flow?
-
Will workstations operate synchronously or asynchronously?
-
What is the total number of workstations needed?
-
What is the available manufacturing space? This will dictate machine layout—linear, rotary indexing, or both?
Once these questions are answered, the machine design will fall under one of these three categories:
Fixed or Hard Automation
Fixed automation equipment produces a large volume of the same product day in and day out. There is a fixed sequence of operations that does not require customization. Operations are directed by the layout of the machinery and components.
Pros —
-
Typically, a fixed system is a lower cost option when compared to programmable and flexible machine builds.
-
Fixed automation offers improved product quality through consistency.
-
Fixed equipment operates at a fixed high speed which increases production rates.
-
When using fixed equipment, ROI is positive due to a lower unit cost for each piece sold.
Cons —
-
The fixed machine layout is inflexible, so design alterations are costly and time consuming.
Programmable Automation
Programmable automation is for the manufacturer that requires a flexible production line for batch runs. This system allows for machine reconfiguration or reprogramming for different product specifications. Computer numerical control (CNC) automates machine control through software and is an example of programmable automation.
Pros —
-
This system is more flexible than fixed, therefore provides for some product variables.
-
This system is designed to run several dozen to over 1000 units.
Cons —
-
For product variables, system software and equipment re-configurations can still be time consuming.
-
With programmable equipment, upfront costs are higher than with general purpose machinery.
Flexible or Soft Automation
An extension of programmable automation, this system allows for even greater flexibility in running batches with less lost time. With this system, you will typically see cobots and robotic arms with a variety of grippers.
Pros —
-
Small batches can be created with minimal machine downtime.
-
Continuous production is enhanced by in sequence product variable programmed adjustments.
Cons —
-
This system requires the most upfront investment.
-
Components must be incorporated that allow for quick changes, such as, a robot arm that requires logic controllers, sensors, and lasers.
-
Skilled labor will be needed for parts changes, programming and maintenance.
-
No matter which system you choose, all your innovative ideas for new automation must work within the context of your organization and budget. But your pre-planning was not for naught. You’ve started the journey. You’ve calculated the benefits of automating your production line and are ready to begin implementing changes. Automation doesn’t have to be all or nothing; it can begin in increments. If you’re just starting to grasp the concepts from the IoT, don’t feel like you must start with a huge machinery update. Narrowing down your needs and starting slow will help keep development and testing manageable. This will also give you time to ingest and digest the new manufacturing technologies. You may be surprised at how quickly you catch on.
About Trimantec
Trimantec has a reputation as a leader in engineered solutions for manufacturers from a variety of industries that include pharmaceutical, medical, textile and automotive.
If you like this article you may like "Predictive Analytics vs Machine Learning"
The content & opinions in this article are the author’s and do not necessarily represent the views of ManufacturingTomorrow
Comments (0)
This post does not have any comments. Be the first to leave a comment below.
Featured Product
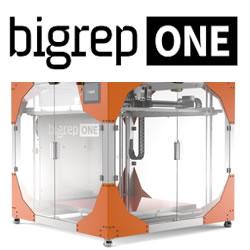