Cobots aside, there are many more ways in which warehouses can be improved to boost efficiency and productivity. Many of those opportunities also decrease associated costs, simply because of the benefits they offer.
10 Ways Warehouses Can Decrease Costs and Increase Efficiency
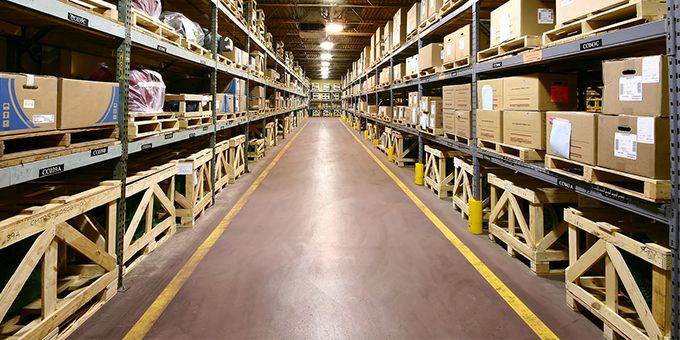
Emily Folk | Conservation Folks
A series of factors and events are leading to increased operations costs for the entire business sector. The average shipping and fulfillment warehouse is no exception to this change, with everything from labor costs to the general cost of electricity continuing to climb day in and day out.
It’s no surprise that many businesses and service providers are looking to reduce costs through continual improvements, specifically when it comes to operational efficiency. Amazon’s renowned shipping and order fulfillment centers are a prime example, which employs collaborative robots or cobots to work alongside their human counterparts.
Cobots aside, there are many more ways in which warehouses can be improved to boost efficiency and productivity. Many of those opportunities also decrease associated costs, simply because of the benefits they offer.
1. Automation and Advanced Robotics
Manufacturers and warehouse owners alike can employ advanced technologies to automate a lot of their operations. Research from Boston Consulting Group purports 1.2 million robots will be deployed in U.S. manufacturing facilities by the year 2025. They will introduce a bevy of advantages, namely lower operating costs and greater productivity.
When used alongside human workers, operations still have a human touch where necessary yet repetitive tasks can be automated to reduce errors, increase overall efficiency and boost output.
2. Smarter Use of Space
When extending storage space or applicable rooms many warehouse operations expand outward in terms of horizontal growth. But as is true of most production floors space can fill up quickly, many times even hindering worker performance and navigation.
There are solutions — like pallet racking and vertical shelving — which allow warehouses to expand up instead of out. With the help of those advanced robotics and smart shelving systems, this can even be achieved all while maintaining efficiency and safety.
3. Climate Control Improvements
Whether it's cold storage, or general climate controlled spaces the necessary HVAC systems consume lots of power.
Many improvements that can be made to cooling systems to enhance efficiency and lower resource consumption. Swapping out older HVAC and control systems, for example, can have a significant impact on operational costs. Compared to units from 40, 30, 20 or even 10 years ago, today’s systems are much more efficient which means they can run at the same temperatures — or lower — while using even less energy.
They can be improved even more through automation and IoT. For example, smart thermostats can be used to program a schedule, creating a more efficient adjustment process.
4. Streamlined Picking Processes
One of the more common tasks for warehouse workers is picking, whether for order fulfillment or inventory management.
IoT and RFID tracking technologies can make this entire process so much faster. It allows for the quick and accurate identification of various goods and will ultimately streamline the entire picking process.
5. Keep It Clean
A clean and more organized facility will see higher productivity. Workers can get around and complete their tasks faster. The inventory stored within a warehouse is much easier to locate and that improves picking.
6. A Fully Digitized Environment
In some warehouses — especially those converted from analog operations — inventory tracking tools are used only in a small area. Maybe the facility was expanded and the new areas were not integrated properly? Maybe the budget only covered upgrading a portion of the warehouse?
Whatever the case, this is a definite setback for efficiency. When a warehouse is digitized, it should be done throughout the entire facility, not just minor sections. Every room, space and storage area should use the same digital tracking solutions to monitor inventory and speed up regular operations.
7. Performance Metrics and Reporting Tools
How do you know things are going well if you have no way to measure performance? Be sure there are suitable tracking tools and systems in place, but also reporting solutions to relay necessary information to the workforce. It’s important to tell workers how they are faring in terms of productivity, as well as provide tips for how they can improve or better themselves.
This, of course, means defining expectations or goal levels so everyone knows what they should be chasing in terms of efficiency and performance.
8. Establish a Vendor-Compliance Program
Before goods come into the warehouse and after they go out, they’re the responsibility of partners and vendors. The fact of the matter is, a warehouse and its workforce can be completely efficient, but if a vendor is not on the same performance level it will create setbacks for everyone.
Every warehouse should have vendor compliance agreements in place, so partners understand exactly what they need to do and how it affects everyone around them. The ramifications of a delay, mistake or poor decision may not be known to external parties so it's an important distinction to make.
9. Inventory Management Is Crucial
While obvious, inventory management is instrumental in keeping a warehouse efficient. Implementing the appropriate management and tracking solutions is an absolute requirement if only to keep the entire supply process automated. The last thing pickers need is to discover certain items are out of stock because it will significantly hinder their duties.
10. Anticipate Scalability
Heightened labor costs also come from overtime and long hours, particularly from a limited or depleted workforce. It’s important to properly manage worker availability to deal with higher — or even lower — demands. Amazon offsets this in many ways with help from its cobot workforce. That may or may not work for all operations.
The main point is simply understanding and planning for workforce demands. That includes understanding the entire warehouse space and how much personnel it can support, in addition to everything else contained within. Sometimes, it may be necessary to open new locations or move to a larger facility.
If these tips are honored, the resulting warehouse operations will become much smoother and more streamlined.
The content & opinions in this article are the author’s and do not necessarily represent the views of ManufacturingTomorrow
Comments (0)
This post does not have any comments. Be the first to leave a comment below.
Featured Product
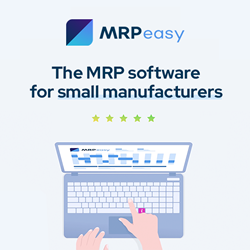