The materials have a non-uniform, crystalline structure, making components built with them much stronger than those built using a standard uniform lattice structure. So much stronger, in fact, that they can withstand seven times the amount of energy ...
New 3D Printing Material Builds Extra-Strength Parts
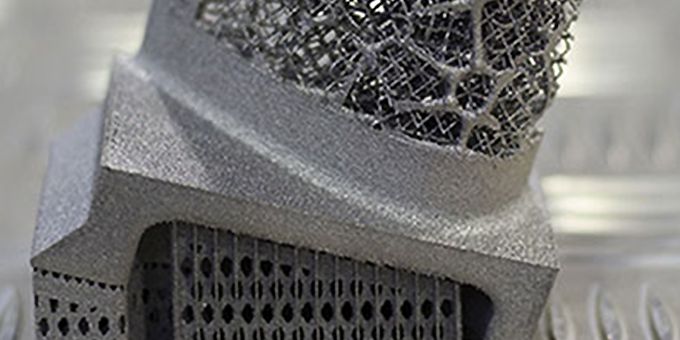
Nicole Hopper, Communications Specialist | Protolabs
A team of researchers from the University of Sheffield and Imperial College London have developed a new family of 3D-printed materials that they named meta-crystals. The materials have a non-uniform, crystalline structure, making components built with them much stronger than those built using a standard uniform lattice structure. So much stronger, in fact, that they can withstand seven times the amount of energy compared to structures built with single-crystal structure lattice materials.
The extra strength comes from the random nature of the lattice in the meta-crystal material. With uniform lattice structures, force from any single direction ripples through the entire piece. The random lattice alignment in the new material, modeled after the atomic structure of a polycrystalline material, means that a crack in any direction is slowed down or stopped when it meets a crystal with differently aligned atoms.
As 3D printing continues to transform manufacturing by allowing product developers to create unique designs impossible to attain through traditional manufacturing techniques, this material advancement is significant. It provides a new and innovative model for future material conception and development. And, the materials could be used in standalone structures, as well as in combination with other materials, expanding the variety of applications in which they’d be useful.
Fully-dense metal test components were built on the University’s Arcam Q20+ industrial-grade 3D printing machine. Photo Courtesy: The University of Sheffield.
“This meta-crystal approach could be combined with recent advances in multi-material 3D printing to open up a new frontier of research in developing new advanced materials that are lightweight and mechanically robust, with the potential to advance future low carbon technologies," said Dr. Minh-Son Pham of Imperial College London.
Beyond additive manufacturing, combining physical metallurgy with architected materials provides a new approach to overall material development. For example, engineers would be able to create damage-tolerant materials with strength and durability, while improving the material’s response to external loads.
The content & opinions in this article are the author’s and do not necessarily represent the views of ManufacturingTomorrow
Comments (0)
This post does not have any comments. Be the first to leave a comment below.
Featured Product
