Cognitive technologies can be defined as methods that perform or supplement tasks, help to make better decisions, and complete objectives that usually require human intelligence, such as planning, reasoning, and learning.
Implementing Cognitive Technologies in Manufacturing
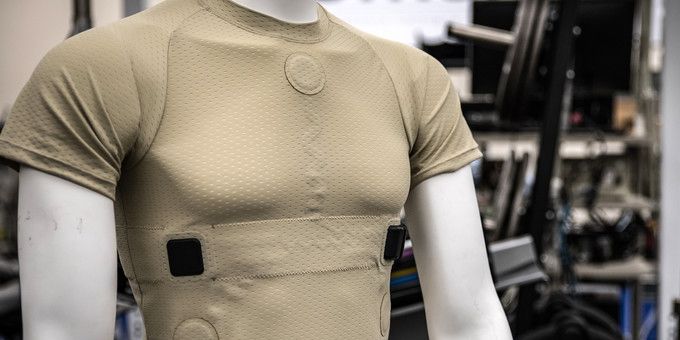
Len Calderone for | ManufacturingTomorrow
Cognitive technologies are influencing the way that we live and work. These technologies give businesses a competitive advantage, and have changed the way work is performed, and how employers interact with workers, customers, and suppliers.
Cognitive technologies can be defined as methods that perform or supplement tasks, help to make better decisions, and complete objectives that usually require human intelligence, such as planning, reasoning, and learning.
Cognitive language technologies consist of a set of statistical techniques that allow the analysis, understanding, and production of human languages to expedite interfacing with machines, using written and verbal situations.
Cognitive machine learning automates diagnostics using algorithms that learn from data without the need for precise programming.
Cognitive computer vision automatically mines, evaluates, and comprehends useful information from a single or sequence of images better than human vision.
Some manufacturers ask if there is a difference between artificial intelligence and cognitive computing. Artificial intelligence tells a manufacturer which course of action to take based on its analysis. A cognitive computer provides information to help the manufacturer decide on a course of action.
The volume of data will grow, as more factories utilize the IoT. IoT will be one of the principal drivers of digital transformation for years to come. The total number of IoT devices is projected to hit 10 billion by 2020. With this upsurge of growth, conversations around how to benefit from these devices and the data they create to better our businesses and our lives will be essential. Because of the large volume of data being disseminated, conventional computing will have a hard time keeping up. Computing must now become cognitive in order to manage, evaluate, and improve on the information.
Intelligent assets and equipment will be needed to utilize connected sensors and analytics. Furthermore, cognitive capabilities will be needed to recognize, communicate and self-diagnose problems in order to improve performance and cut down on unnecessary downtime.
Smarter resources and optimization will be needed to coalesce various forms of data from workers, various locations, and equipment usage with cognitive understanding to improve resources such as workforce and energy.
The development of smart robots using machine learning techniques will remain a leading area of attention for cognitive factories. The global industrial robotics market is expected to reach $70 billion by 2023. Smart robots are already equipped with an arrangement of sensors and fundamental technology that makes them easy to program. As these robots get smarter, they’ll be more responsive and autonomous.
They will help manufacturers meet production objectives by being more reactive to market changes, and customer preferences. These proficiencies will make smart robots highly advantageous in settings usually retained by industrial robots. In the near future, the durability, low cost and intelligence of smart robots will lead to extensive adoption of the technology in smaller factories.
Cognitive computing is another portion of the digital transformation that the manufacturing industry is embarking on. There are many different technology trends that are on the rise and every one of these can be applied in part or whole. Adopting new technologies can be something that can be done in phases and cognitive computing fits right into that form.
In the 1900s, we went from computers that could formulate sums to programmable systems in the 1950s, and now to cognitive systems. Utilizing self-learning algorithms that use data mining, pattern identification and managing language, the computer can simulate the way the human brain works.
Manufacturers have to tackle the challenge of maintaining anticipated rates of production, especially when it comes to creating projected levels of cooperation across manufacturing operations. Using deep search and detection, cognitive maintenance can expose critical patterns that can improve prognostic maintenance, preventing unplanned downtime. Cognitive approaches can also help with flexible automation for manufacturers confronted with configuring machines quickly to increase flexibility.
Shortages can be prevented using cognitive parts management with supplier details, weather and transportation information. This information keeps lines up and running and fosters business responsiveness.
Visual cognitive inspection eliminates defective parts and devices before they ship to the marketplace. It assesses key defect types during in-line processes and communicates with the systems that process and catalogs them. It also quickly reconfigures production lines.
When a piece of machinery is connected to a cognitive computing system, it begins producing data for analysis. The computing system then operates as the equipment's cognitive brain. If a supercomputer is added to the manufacturing equipment, it can use information from the sensors attached to the equipment and implement predictive analytics on things like motor or bearing failure. The machine-learning algorithms in the cognitive computing system look for glitches in a system’s performance and actions.
IBM’s Watson super computer
With a sensor added to a piece of machinery that monitors sound vibrations from a rotating shaft, it can automatically alert operators should the sound vibrations suddenly oscillate outside of what the cognitive computing system has determined to be the normal state. This would prevent a machine from being destroyed should a part fail.
The machine can actually schedule its own service call or turn itself off before a devastating failure occurs.
A cognitive computing system can draw parallels between process variables such as solder temperature and production levels of a manufacturing run. Extensive numbers of process and control system variables can be evaluated against manufacturing performance. Manufacturers can use cognitive manufacturing technologies to meticulously monitor and understand the many operational attributes that impact product quality to guarantee that all products shipped to market meet their companies’ quality requirements.
Providing employees with sensors that help ensure their safety is a persuasive purpose for cognitive technologies. Wearable sensors constantly monitor the employee’s health and endurance as well as their exposure to environmental or physical hazards.
Air Force wearable medical tech
Cognitive technologies integrate data from the sensors and other pertinent environmental sources to immediately identify difficult situations that might affect an employees’ health. The technology alerts the worker or supervisor of any problems that need a fast reaction.
Cognitive technologies have already brought amazing things to multiple departments in manufacturing. We’re just beginning to scratch the surface.
The content & opinions in this article are the author’s and do not necessarily represent the views of ManufacturingTomorrow
Comments (0)
This post does not have any comments. Be the first to leave a comment below.
Featured Product
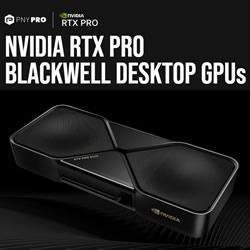