Warehouses are vitally important links in our supply chains and distribution networks — but they could always be more energy-efficient. Here's a look at some of the trends helping warehousing companies save money and reduce their environmental footprints at the same time.
Energy Efficiency Trends for Warehouses
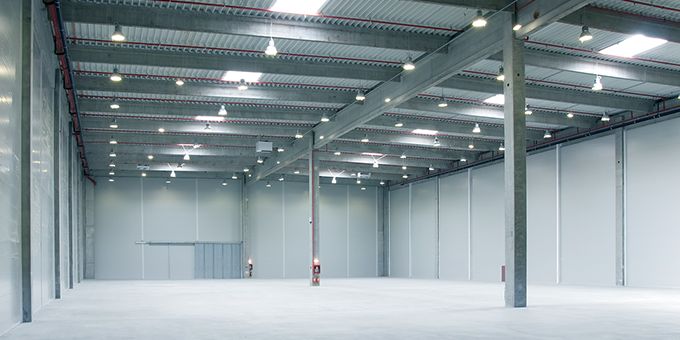
Emily Folk | Conservation Folks
Get an Energy Audit
Energy audits aren't a new idea, but they're receiving renewed attention as we become more mindful about wasteful consumption and missed opportunities in facility design.
There's a good chance your local energy utility companies provide onsite energy audit services you can take advantage of. And even if they don't, they (or a public group like the Environmental Defense Fund) probably keep a regularly updated list of best practices and things you can inspect for, or add, yourself. Things like:
- Replacing worn-out weatherstripping around windows
- Placing or replacing poorly placed or missing insulation
- Sealing other air leaks
- Properly sealing bumpers where trucks pull up to your docks
- "De lamp" in areas where maximum lighting isn't needed
- Install occupancy sensors for lighting systems
The point is, you work in this facility every day and you're likely to have some blind spots. But professionals are trained to find all of those little gaps and oversights that contribute to wasted energy and higher operational costs in a way that you're not. Enlist the help of the experts when you want to shore up your facility for maximum efficiency.
Establish Temperature Zones
Refrigeration and temperature control are two of the biggest energy-related expenses for warehousing companies.
As far are refrigeration goes, one of the most popular upgrades for warehouse managers today is variable-frequency drives for refrigerated areas. These allow more finely tuned temperature control in areas where you store perishable food, beverage or pharmaceutical products, and as a result help companies avoid spending money on energy they don't actually have to use.
Along with greater temperature control capabilities, companies are also turning to zoned refrigeration and climate control. Not every product requires freezing or the same level of refrigeration. And not every part of the warehouse needs its climate control engaged full-bore all day long. As a result, internet-connected HVAC systems and remote temperature controllers are an increasingly common sight in warehouses.
Making these investments doesn't just allow warehouses to save money by tailoring the environment to their needs — it also frees them to take on, store and distribute a wider variety of materials and products in the future.
Retrofit Machines for Performance
The electrical motors used under your roof in vehicles (pallet movers, lift trucks, etc.) and in material handling equipment (conveyors, etc.) are some of the biggest energy draws in your entire facility — up to 65% of it, actually. Gear reducers are one way to combat this, as they allow machines to function at close to full capacity but while drawing less power.
For these reasons, it's wise to prioritize energy efficiency as you make plans to upgrade any of the machines and other physical assets you rely on. Look for models that promise or are certified to deliver energy savings.
If your energy audit results do spark conversations about machine upgrades, know your options before committing any capital. If the entire potential Internet of Things industry is worth something like $1.7 trillion, then some say the "IoT retrofit" market represents about 22% of the entire pie. Adding IoT functionality to warehouse implements can yield insights about how to tweak their performance or usage to maximize efficiency. And retrofitting vehicles like pallet trucks to operate themselves can help eliminate wasteful idling and make pathfinding throughout the warehouse as efficient as possible.
Take Another Look at Your Distribution Network
Industries have unprecedented access to data visualization techniques and analytical services these days, including business mapping tools that can help you get to the bottom of delivery and distribution route problems and solve other bottlenecks.
Keep in mind that when we talk about the efficiency of a warehouse, we're not just talking about the building and the activities that take place there. We're also talking about the number of vehicles and the amount of time and fuel it takes to send trucks to this facility and then dispatch them again.
So take another look at your distribution network and discover whether there are ways to reposition facilities, add locations, or engage with redistributors or drop-shippers. You may not even have to make a huge change to realize operational and energy efficiency here — moving a facility just across the river, for example, might help vehicles avoid consistently congested traffic in a key area. Mapping your territory may even reveal opportunities to find new vendors, partners and delivery companies: ones that won't cost your business as much money in lost time and efficiency and unnecessary transportation.
There are many other trends in warehousing that are likely to bring greater efficiency, but this is a good starting point for any facility manager who wants to adopt a greener approach as a competitive advantage and a way to bring down costs.
The content & opinions in this article are the author’s and do not necessarily represent the views of ManufacturingTomorrow
Comments (0)
This post does not have any comments. Be the first to leave a comment below.
Featured Product
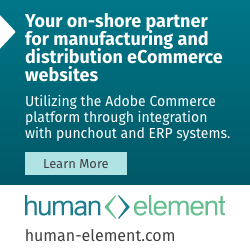