At the factory level (for tooling, jigs, fixtures, molds, and other means of production) it will allow faster, cheaper, and better-designed parts production. Eventually, 3D printing will transition into end-use parts and 3D printers themselves will become part of factories.
3D Printing Industry Outlook
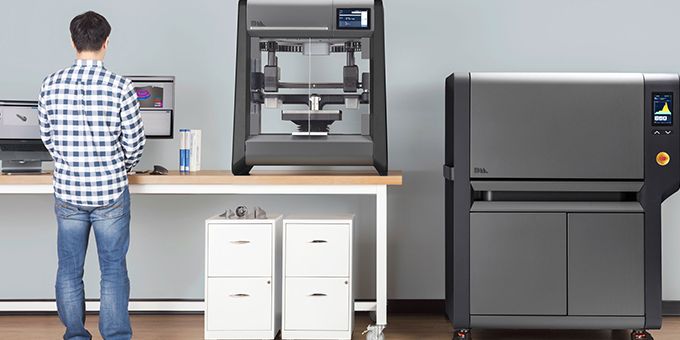
Douglas Krone | Dynamism
How has the 3D printing industry evolved?
Innovation and competition were unleashed in 2011 as various 3D printing patents expired.
Where are you seeing the most innovation?
In 2019, a second “Big Bang” in 3D printing as several factors has led to increased investment, innovation, and competition in industrial-grade 3D printing. New technology in industrial 3D printing is where the innovation (and investment) is happening.
How will industrial 3D printing affect the global marketplace.
At the factory level (for tooling, jigs, fixtures, molds, and other means of production) it will allow faster, cheaper, and better-designed parts production. Eventually, 3D printing will transition into end-use parts and 3D printers themselves will become part of factories.
Who are the biggest players in the industry?
The incumbents remain big: Stratasys, 3D Systems, EOS. But the innovators are driving the industry forward: Desktop Metal, Carbon, Ultimaker, Nexa, and others.
What are the most common applications in the industrial area?
Compared to machining, 3D printers can be faster for tooling, jigs, fixtures, molds. They can print in steel for a lower cost than machining steel. And they can print in carbon fiber for 90-97% savings in time and cost.
Which sectors are the most active?
Automotive is the most active, followed by other types of durable goods and consumer goods production.
Any predictions?
As more patents expire, more infrastructure is built, more companies design for 3D printing, large scale and rapid investment continues to flow into 3D printing, we will see better, faster, cheaper, more capable printers, printing in a wider array of materials, and eventually end-use parts.
What is Dynamism?
Dynamism is a leading enterprise-focused provider of 3D printing hardware, software, integration, training, and service. Our focus is to couple the best and most transformative products in the industry with world-class expertise and support.
Douglas Krone, CEO and Founder of Dynamism
Douglas Krone is an internet entrepreneur and the founder and CEO of Dynamism Inc. (www.dynamism.com), a leader in 3D printing solutions and services.
The content & opinions in this article are the author’s and do not necessarily represent the views of ManufacturingTomorrow
Comments (0)
This post does not have any comments. Be the first to leave a comment below.
Featured Product
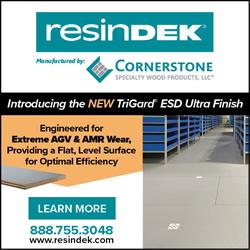